Surface finishes play a crucial role in enhancing the functionality, durability, and aesthetics of die casting parts. Proper surface finish options make die cast parts have beautiful appearances and more stronger corrosion resistance and gain an added value. Of course, Die casting parts can have many surface finishing options. As what we are often known of, that is about 7 types. The below content will introduce 7 top surface finishes for die casting .
Content guideline Table
What Are Surface Finishes For Die Casting?
The surface finishes for die casting means the texture, plating, powder-coated, painting, electrophoretic coating, anodized and passivation of the surface of a die-cast part. Die casting process is as an essential manufacturing process, which produces parts with excellent surface finishes with the mold. In order to add additional surface finishes, The die casting may be treated with various surface finish options. Here are some aspects of die casting surface finishes.
1. As-Cast Finish
The as-cast surface reflects the quality of the mold and the alloy material. In general condition, minor imperfections such as parting lines, ejector pin marks, or slight porosity and less hidden burrs produce during die casting process. But the surface of part appearance is fine and smooth.
2. Die Casting Surface Finish By Post Process
The surface of as-cast die casting part is often rough and need further processes to improve. Rough surface finishes can be improved through various post-processing methods, the below processese involved.
- Polishing: Achieves a mirror-like or highly reflective finish.
- Grinding or Sanding: Removes imperfections or smooths out rough areas.
- Shot Blasting or Bead Blasting: Creates a uniform matte texture.
- Plating (Electroplating): Adds a layer of metal like chrome, nickel, or zinc for corrosion resistance and aesthetic appeal so that extending the product life time.
- Painting or Powder Coating: Provides color, added protection, and a smoother surface and enhancing the corrosion resistance.
- Anodizing: Used mainly for aluminum parts, though less common for zinc.
- Passivation: Reinforce the finish surface of the die casting part, passivation help protecting the treatment layer better.
Die casting components require excellent surface finishes. To meet its functionality and specific requirements , they will be secondary processed. As the most commonly die casting parts surface finish, we will use the right suface finish approche to treat them, and ehance its duability and specific functions
7 Top Surface Finishes for Die Casting
Die casting may have too avoid on the surface of casting to better further surface finishing. In order to improve its surface and enhance the die casting parts durability, our experts suggest that die casting parts may do some surface finishes to enhance the life span and durability. Among current surface finishes, there is 7 top types to everyone reference as the below.
Polishing
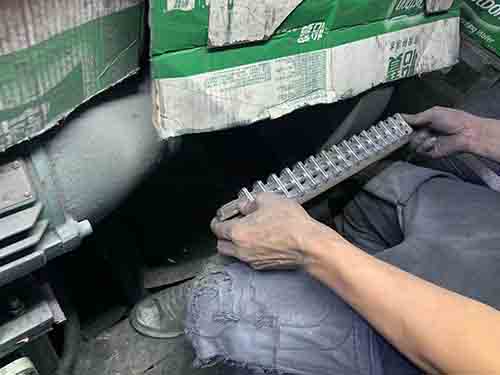
Enhances smoothness and reflects light, creating a shiny appearance and fine surface finish. Using cloth wheel or flax wheel.
Plating (Electroplating)
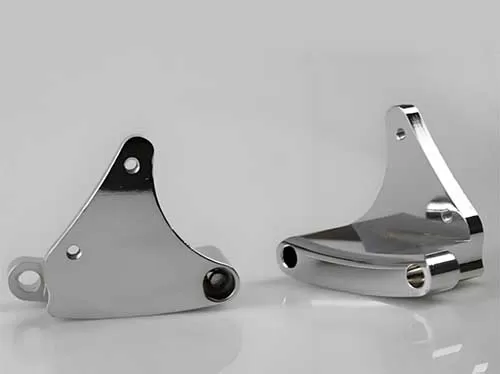
Chrome Plating: Shiny, Mirror-like finish
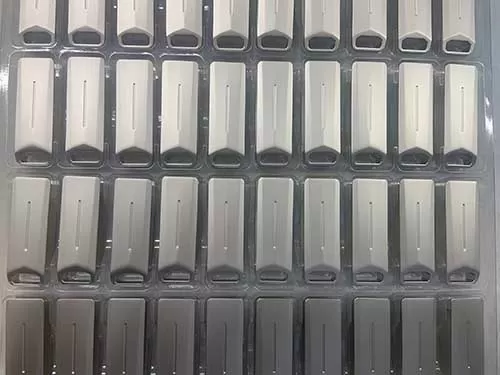
Nickel Plating: Improves hardness and corrosion protection
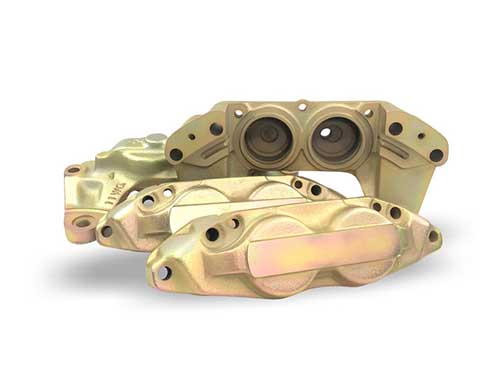
Zinc Plating: Provides Sacrificial Protection
Powder Coating
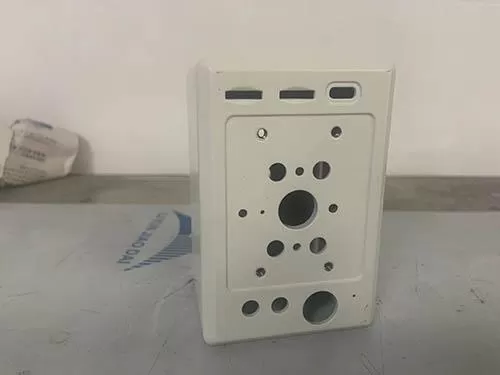
Offers a durable, uniform finish with excellent resistance to wear and corrosion. Prolongs the die casting part life time, Enchances corrosion resistance.
Painting
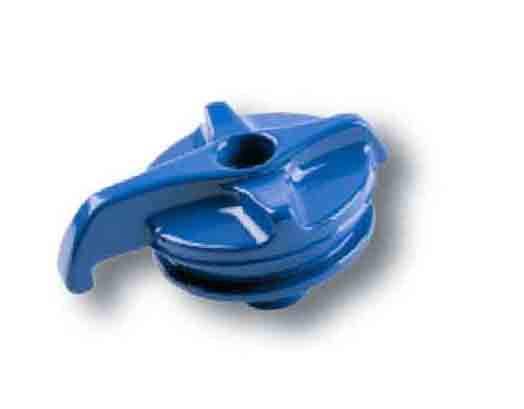
- Types: Spray painting, dip painting, or electrophoretic painting.
- Purpose: Adds color and a layer of protection.
- Applications: Appliances, equipment compoments and decorative parts
E-coating (Electrophoretic Coating)
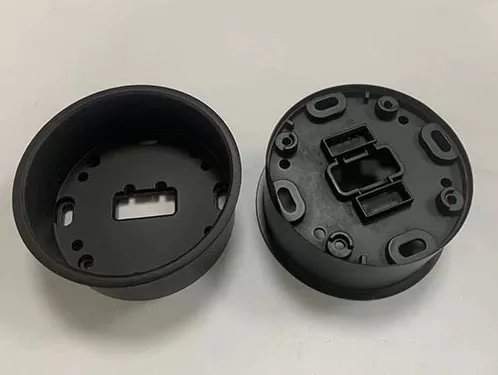
Apply a protective and decorative paint layer to metal parts. It is widely used in automotive, appliances, and industrial applications
Anodizing
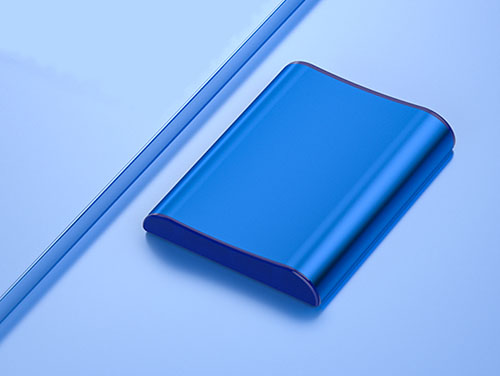
Uses metallic salts (tin, nickel, cobalt) in the anodizing bath, Generate Black, red, blue, gold, and custom colors. Then reinforce the color better, the passivation may done for enhancing wear resistance and color finishes.
Shot Blasting/Bead Blasting
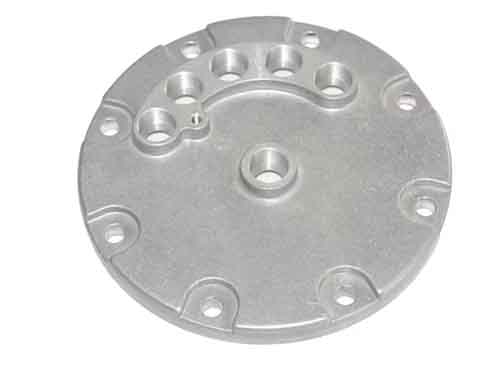
Using fast speed sand particle and tiny size steel beads to brush and beat off excess material on the surface of die casting parts.