This is a common process procedure for die casting part. Especially Zinc alloy casting part, made out from die. Its surface has uneven rough areas, casting seams and some sharp edges. Before they are sent to electroplate factory, these casting parts should be deburred, or sandblasting or polishing so that removing the sharp edges and keep its surfaces smooth. In case they can’t be treated well, so the lots of casting parts should be arranged to rework. Die casting part polishing process is indispensable.
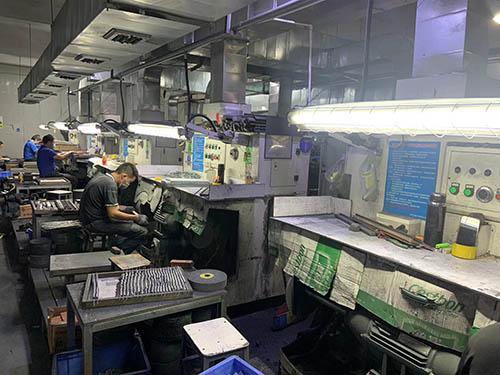
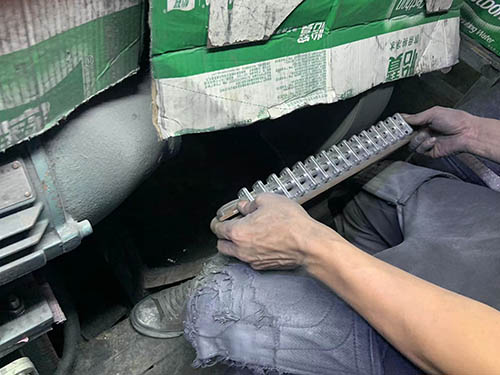
How to polish metal after casting?
In a metal process factory, polishing metal after casting is a multi-step process that improves the surface finish, removes imperfections, and can give the metal a smooth, mirror-like shine. Such as Zinc alloy die casting parts polishing process, As custom die casting parts, Here’s a step-by-step guide on how to polish metal after casting.
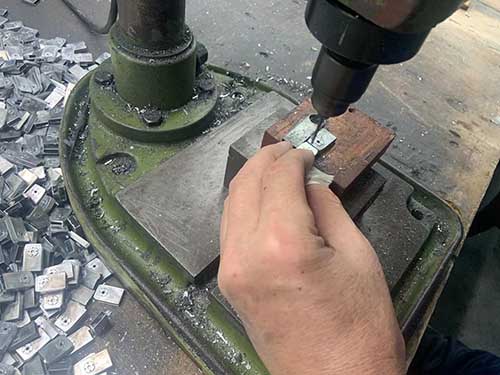
1. Initial Cleaning
After casting, the metal surface may have rough areas, oxidation, or casting residues and excess burrs. we should clean the residues and excess burrs on the surface of the parts:
Remove Scale and Oxides: Commonly with wire brushing, acid pickling, or sandblasting to clean off the residues on the surface of the parts.
Deburring: If there are burrs or sharp edges on the parts , use a deburring tool or file to smooth out these imperfections and excess burrs.
2. Rough Grinding
Rough grinding removes these obvious surface defects like visible seams, flash, or uneven surfaces.
Abrasive Wheel/Grinder: Using a coarse grinding wheel (such as 60-80 grit) to grind down high spots,grindering down casting seams.
Angle Grinder: For larger castings, an angle grinder with a grinding disc can grinder flat rough areas.
Hand Files: For smaller, more delicate parts, use metal files to remove excess material and hidden burrs.
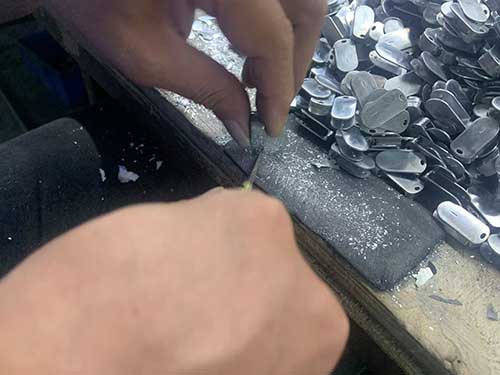
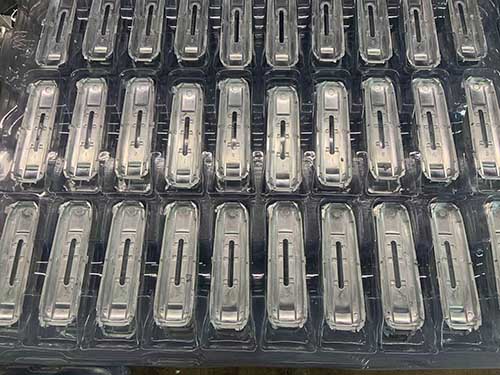
3. Fine Grinding
Once the surface has been roughly smoothed, fine grinding is need to process in further.
Abrasive Wheels/Discs: Choose finer grit wheels with120 grit, more perfect result is achieved with 240 grit.
Belt Sanders: belt sanders with fine-grit belts is neccessary.
Hand Sanding: For intricate or high tolerance smoothness, with fine-grit sandpaper (120-240 grit) by hand, to reach smooth the metal surface.
4. Sanding
Sanding smooth the surface, for metals like aluminum, brass, and steel.
Wet/Dry Sandpaper: Firstly,Using wet/dry sandpaper starting from 400 grit. then moving to finer grits (600, 800, 1000, or higher). Wet sandpaper is better
Sanding Blocks: Use a sanding block to flat even flat surface of parts.
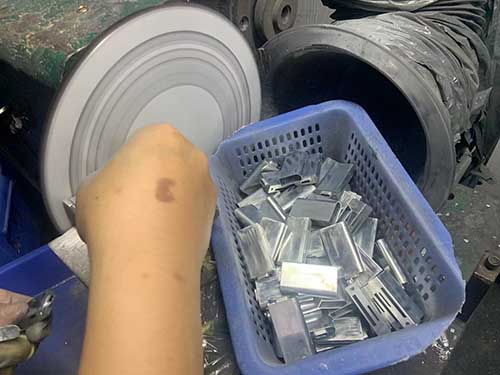
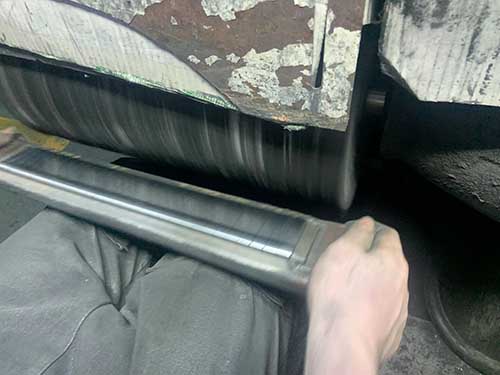
5. Polishing (Buffing)
To have finer abrasives to create a smooth, shiny surface.
Buffing Wheel or Polishing Wheel: Use a soft buffing wheel on rotary tool ,add polishing compounds on it. We will use different polishing compound according to polish different material parts. Sometimes, and polishing wheel is alternative due to achieve different efective surface result.
6. Final Polishing
the hemp and cloth wheel to create a smooth, more shiny surface results.
Hand Polishing: For fine details, use soft polishing cloth wheel or pads, to polish creams to reach small areas that are hard to buff with a wheel.
Microfiber Cloth: Use a clean, soft microfiber cloth to polish off excess compound, buff in further the surface to a shine.
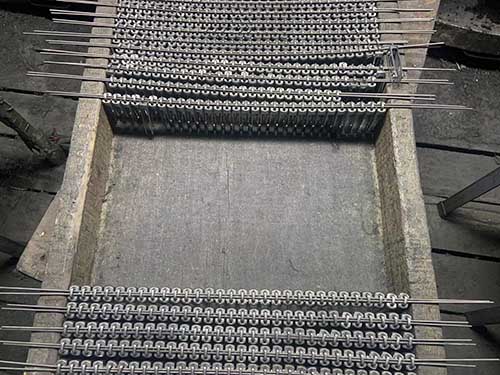
When die casting part polishing is finished, the treated casting metal parts will be sent to outsourcing factory for a good coating so that getting a good appearance.

What’s Your good idea?
Do you really want to find one of professional metal casting factory to finish your project? If you want, please contact us by Email , We also hope to have a chance to work with you