Camera Housing is often made of aluminum alloy material, due to main reasons that it has a good heat sink and light weight. But its cost is very high, request expensive raw material cost and high machining cost. So aluminum camera housing spend more expense. If this kind of camera housing can be replaced by other cheaper material, That will save much expense. Zinc alloy material have been selected, Zinc alloy die casting camera housing may replace aluminum alloy camera housing. Application functions is same , but its cost is lower much than aluminum one.
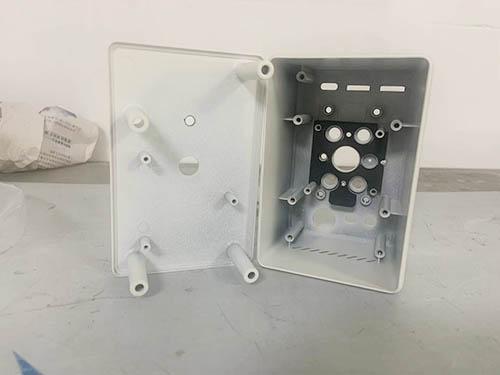
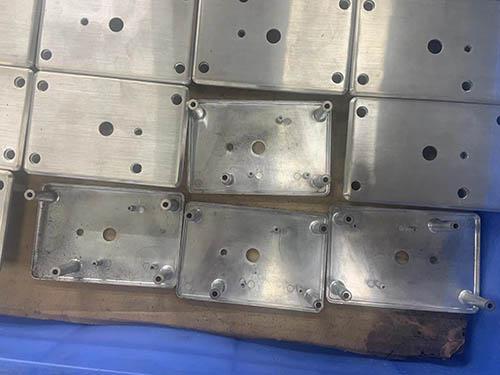
Zinc Alloy Die Casting Camera Housing
Zinc alloy material is pressed into metal die under high pressure, then formed various shapes parts and be cooled into solid metal desired parts. This is metal die casting manufacturing procedure. As custom zinc alloy die casting part, which can be formed into metal parts at reasonable temperature. About 450 degrees at the temperature. Compare to aluminum alloy casting part, which is melton and formed at 800 degrees, That is too easy and lower cost saved.
With delication development of the industrial demands, People are also exploring more zinc alloy products to be used in more fields. Like some precision zinc alloy die casting parts, they are durable and lower cost. But they also have many common properties of other metal materials. Also zinc alloy is recycled and eco-friendly and being friendly to the environment. So zinc alloy material is made of their products is up to ISO 14000 ISO and European Union Rohs and Reach standards etc.
Hot-Chamber Die Casting Machines Advantages
- Suitable for low melting point metal : Primarily used for zinc, magnesium, and other low-melting-point alloys, including most Zamak alloys.
- Setting gooseneck mechanism, simply process steps: In hot-chamber die casting, the metal is melted in a furnace integrated with the machine, create a “gooseneck” mechanism when the molten metal is injected into the mold (die) using hydraulic pressure.
- Fast Cast Cycle and High efficiency Mass Production: This method is faster, with shorter cycle times. It is well-suited for high-volume production of small- to medium-sized parts with intricate details and fine surface finish.
- Lower Mold Wear and Repair: The low melting point alloys keep a lower temperature mold, and decrease the wear from high temperature, endure a longer time molding running and save more metal mold repair and maintenance expense.
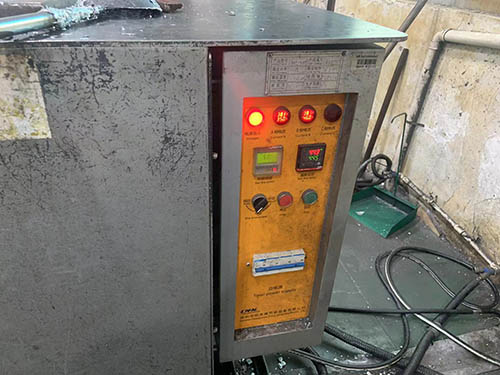
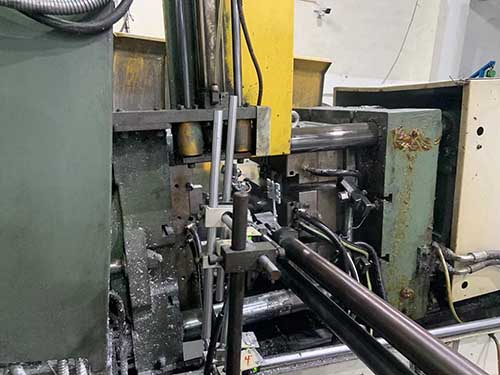
Hot-Chamber Die Casting Process is more suitable for Zinc Alloy Casting Camera Housing
This zinc alloy casting camera is just belong to small and medium size of parts, Casting zinc alloys with hot-chamber die casting machines offers several main advantages as below
1. Faster Production Cycle
Hot-chamber machines have fast cycle times because the molten zinc is directly injected into the mold from an integrated furnace. This minimizes downtime between casting cycles and leads to high-volume production. Zinc alloys solidify quickly, further speeding up the production process.
2. Cost-Effectiveness
The rapid cycle times reduce labor and machine operation costs. Because zinc alloys flow easily and fill molds efficiently, the process has fewer rejections and defects, minimizing material waste. Since the furnace is part of the machine and the molten metal remains ready for injection, energy consumption is optimized, making the process more efficient compared to cold-chamber casting.
3. Excellent Surface Finish and Precision
Zinc alloys cast with hot-chamber machines offer excellent precision, allowing complex, intricate shapes and thin-walled parts to be produced without defects. The process results in a high-quality surface finish, which often eliminates the need for extensive secondary machining or finishing operations.
4. Reduced Wear and Tear on Equipment
Zinc alloys have a low melting point (around 380-400°C), which is ideal for hot-chamber casting. The low temperature reduces wear on the machine’s components, prolonging the life of the molds and other parts. Because zinc alloys are less abrasive on molds, they increase the mold life, reducing tooling costs and downtime for maintenance or replacement.
5. Minimal Material Waste
The hot-chamber process allows for the continuous reuse of molten zinc. Any excess metal can easily be recycled, reducing waste and material costs. The precision of the process often produces parts that require little to no additional machining, which reduces scrap material.
6. Compatibility with Complex Designs
Zinc alloys have excellent flow characteristics, which allow for casting parts with intricate designs, sharp edges, and very thin walls that might be difficult or impossible to achieve with other metals or processes. The high fluidity of zinc alloys ensures even distribution of the molten metal, resulting in consistent and defect-free parts.
7. Strength and Durability of Zinc Alloys
Zinc alloys provide a great balance of strength, toughness, and corrosion resistance. When cast using hot-chamber machines, these alloys maintain their structural integrity, making them ideal for a wide range of industrial and consumer applications. Zinc naturally resists corrosion, extending the lifespan of parts produced, particularly those used in outdoor or harsh environments.
8. Environmentally Friendly Process
Since the casting process is fast and uses lower temperatures than other metals (like aluminum or brass), it is more energy-efficient. Zinc alloys can be easily recycled, and the casting process itself generates less waste, making it a greener choice for manufacturers.
Coating Double Layers: Electroplating and Powder-Coating
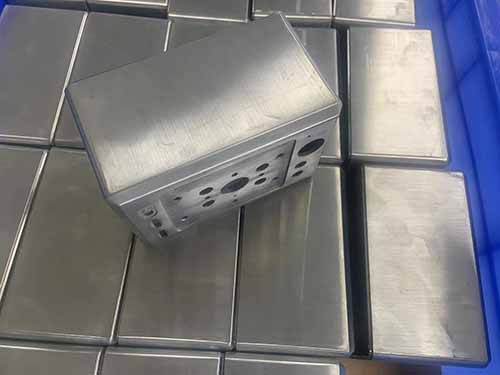
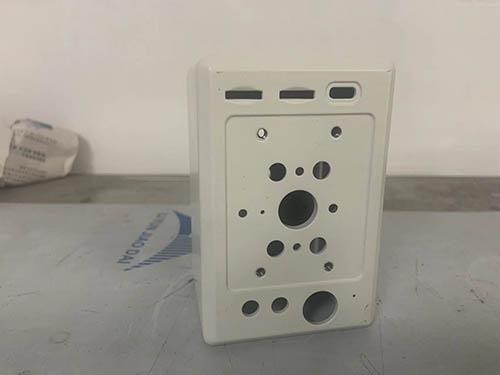
For aluminum alloy products, oxidation is the best way for its surface treatment in order to prevent its corrosion of the product from acid in the air or acid rain. Like former extruded aluminum alloy camera housing, which is anodized on the surface of housing. However Zinc alloy casting housing, its surface is also treated in order to prevent corrosion from acid. So this zinc alloy camera housing is coated by double layer: electroplating and powder-coating.