Some products are used in some special occasions for its unique usage and special functionality. For a long life span and its durability, people require have a special process to the part. Wrapping plastic zinc die casting ball is common processing option. Sometimes using plastic to wrap metal part to reach a mild feeling and touch when people touch it. This is what I want to mention as the below, Rubber wrapping zinc casting part can provide more benefits and conveniences.
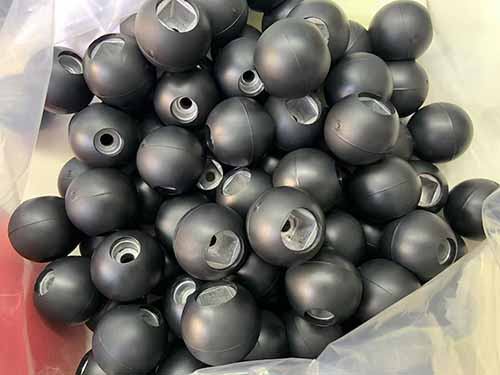
Required Raw Material
Zamk3 Zinc Alloy Ingot
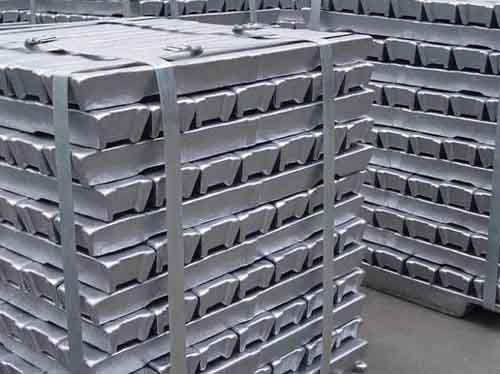
90 Degrees TPU Plastic material
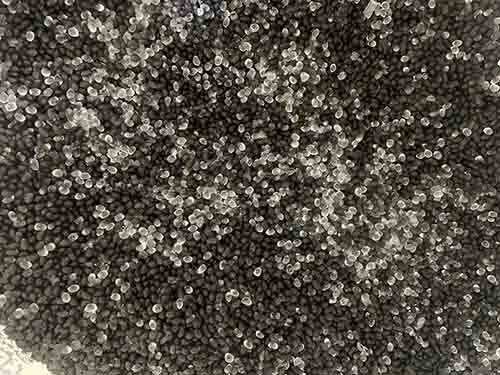
Precise Production Process Operation Step By Step
1. Provide zinc casting ball by hot chamber die casting machine
This kind of miniature parts die casting is more favor of zinc die casting, because they require a complex geometry and precision dimension, with a strong strength, durable as well. On the surface of the metal ball is designed with many slots so that enhancing fraction power between plastic cover and metal body. Avoid have a bad rotation when the rubber wrapping metal ball is operated by human. Added the TPU cover soft feeling, making have a mild feeling. This design is The Technique Of Supporting Casting Zinc Alloy With Hot chamber Die Casting Machines, it will finish the project in perfect.
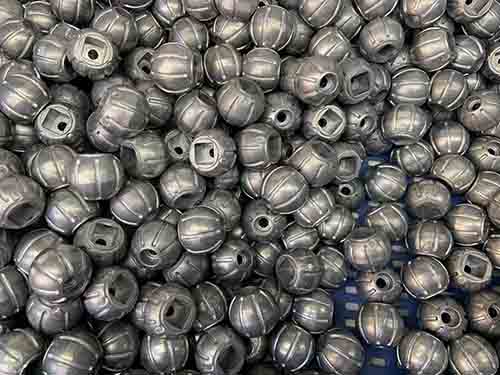
2. Warm up these casting ball with heater
In order to enclose the metal ball fully with rubber, these metal ball should be heated with heating machine before injection. The TPU melt point is at 220 degrees,zinc alloy melt point is much over it. So we don’t worry about it. When using wrapping rubber the zinc casting ball, you should warm up the ball to 120 degrees to match with cold shrinkage of TPU material during plastic injection, which is also the reason that scratches produce on the surface of wrapping cover. So we should be attended of difference of temperature between plastic and metal.
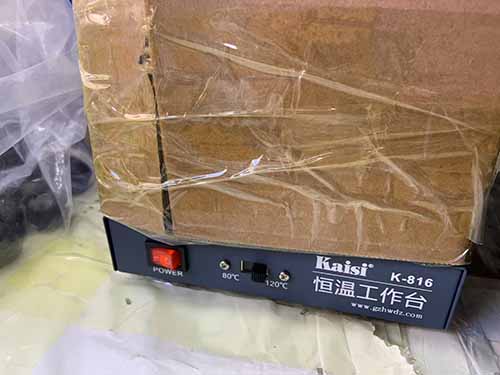
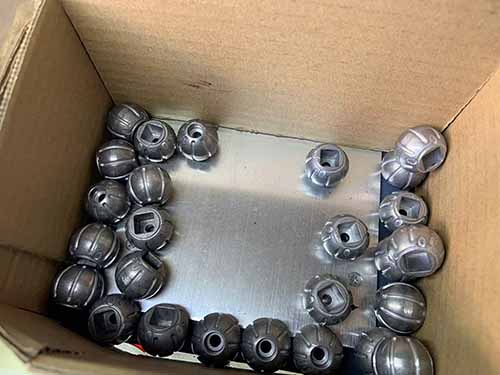
3. Putting the balls into the cavities of the plastic injection mold and Proceeding Process
Putting the heated metal ball into plastic injection mold, At this time, the mold designing should consider of draft angles adjustment and ensure the mold can be opened smoothly, meanwhile being sure that the surface of the injected combined body is smooth, even thickness plastic layer on the metal ball. Improving the imperfection rate of the mass production.
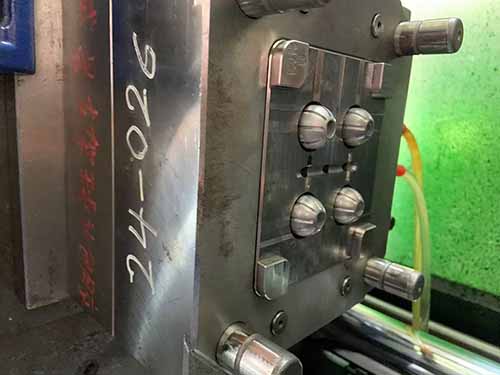
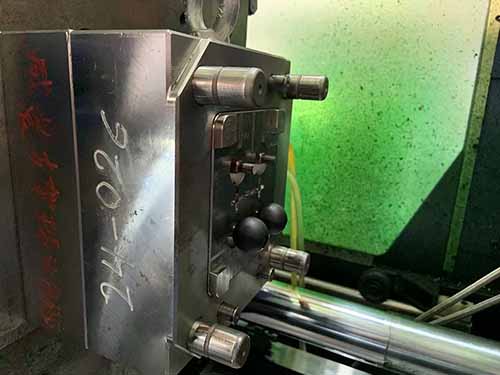
4. Checked by operator and sort out from good quality and defect
The wrapping rubber zinc die casting ball is ejected, they should be inspected. The operator use his own eyes to find some defect goods from the mass production. They find that some goods have blank area and scratches on the injected ball, and adjust that they are defect ones, and require to separate from all goods, put two different area respectively.
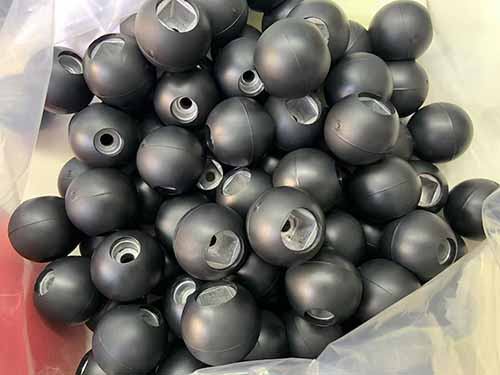
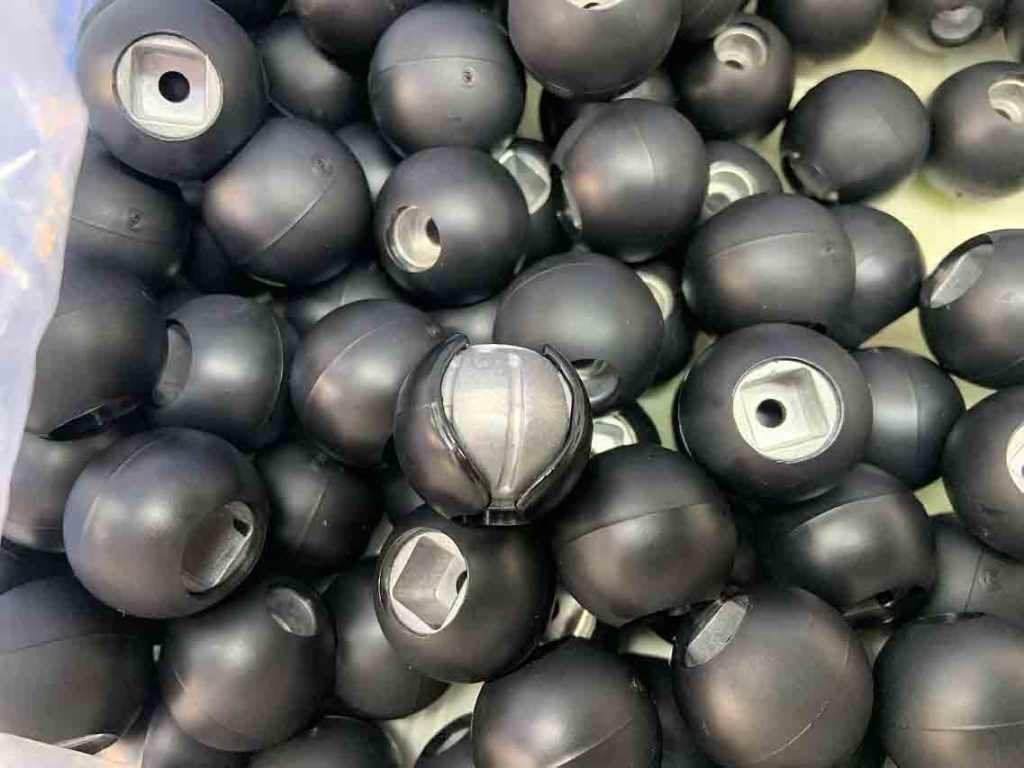
5. Packaging the good quality products and ready for shipment
Packaging the good quality wrapping rubber zinc die casting balls into plastic bag and ready for shipment in accordance with client requirements. This is last operation procedure. We choose high quality plastic bag to pack these good quality finished goods.
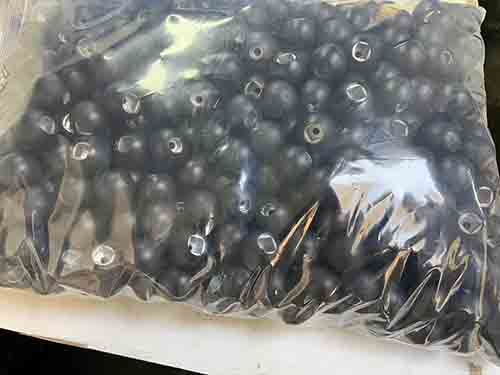
Avoid the scratches when wrapping rubber on the surface of zinc die casting ball
Avoiding scratches on the surface of a zinc die-cast ball when wrapping it with TPU (thermoplastic polyurethane), we should careful handle and control of several aspects. Here are some strategies:
1. Surface Preparation
- Ensure the zinc die-cast ball is polished to a smooth,its overall suface is even and smooth before TPU wrapping.
- Remove any dirt, grease, or particles from the surface of the ball. Any contaminants can cause wrapping layer is not even, and impact the wrapping ball integrated structure.
2. TPU Wrapping Process
- Ensure uniform heating of the TPU material, avoid partical heating on the ball’s surface and cause shrinkage and marks.
- Use a lubricant or mold release agent is compatible with TPU and ensure any stick residues on the surface of core and lead to any defects on the surface of the ball.
- Provide consistent and gentle pressure during the wrapping process, and avoid excessive force that might scratch the ball’s surface.
3. Equipment and Tooling
- Optimize wrapping tools consistently, improve any sharp edges or rough surfaces that could scratch the zinc surface and wrapping ball suface.
- Regularly inspect plastic injection machines and wrapping tools, avoid worn-out wrapping tools to increase the risk of surface sctaches.
4. Post-Wrapping Handling
- After the TPU is wrapped on the zinc ball, we should handle the ball carefully with soft or padded tools. and prevent scratching during transportation or assembly.
- Use foam or soft liners in packaging the finished wrapped ball and minimizing any frictions and scratching among them.
5. Testing and Quality Control
- Conduct small-scale tests to identify specific areas where scratches are likely to occur.
- Implement strict quality control regulations to inspect each product before and after wrapping process.
Additional Considerations
- Ensure that the TPU material is compatible and bond well to zinc alloy, avoid causing stress or damage to the surface.
- Minimize exposure to dust and particles in the workspace, and ensure these zinc ball surface is clear and smooth.
Implementing these measures will help you achieve a scratch-free finish plastic coating on your zinc die-cast balls wrapped with TPU. And ensure that the Wrapping Rubber Zinc Die Casting Ball process running in high efficiency and provide consistently high quality products in mass production.
Project Process Guide
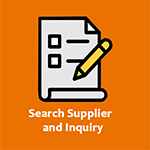
Client send his requirements to supplier, include of pictures and 3d files, need of a price.
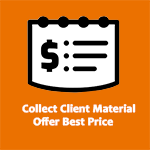
To get client’s inquiry, Collect client requirements and material, quote best price
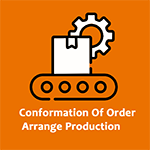
Client confirm the price and Place an order, supplier arrange the production of the order.
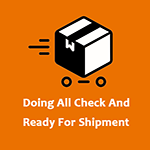
At last step, strict handle of the quality of product, doing all check , ready for shipment.