There are some dirt , oxidation residues, parting line and flashes on the surface of them when die casting part is formed by die and ejected. So these rough parts should be processed and make their surface looks clear, smooth and even areas. Then they are ready to deliver to outsourcing factory for doing surface finish. This makes the meal die casting parts more solid and durable. Because metal casting parts coating can produce some practical functions of corrosion resistance and anti-oxidation. Of course, metal casting parts coating also allows various coating types to finish their coating targets. In accordance with different applications and functionality, Manufacturer can choose the best metal coating method to treat these metal parts.
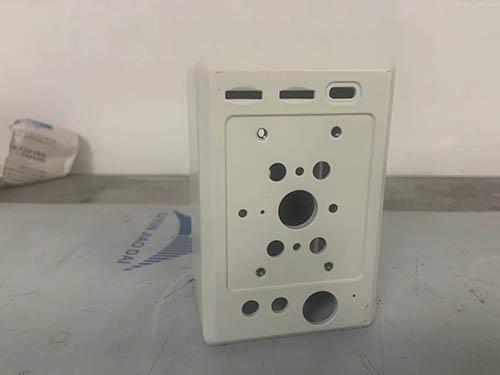
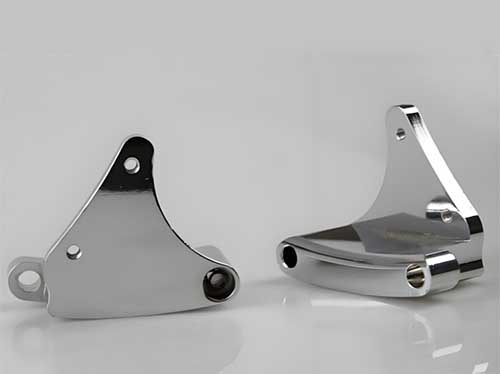
What is Metal Coating ?
Metal coating is the process of using a protective or decorative layer onto the surface of a metal to enhance its durability, resistance to corrosion, wear, or aesthetic appearances. In fact, there are various methods for coating metals, each suited to different purposes and environments. Below is a general overview of the steps involved in coating a metal.
General Steps in Metal Coating Process
Surface Preparation
The metal surface is cleaned and remove dirt, grease, oil, or oxides (rust). The surface may be treated by using methods like sandblasting, shot blasting, or chemical etching. And create a roughened texture for better adhesion of the coating. The metal is thoroughly rinsed to remove cleaning agents and is dried to avoid contamination.
Coating Types
A spray gun is used to cover a thin, even layer of the coating (e.g., paint or powder) on the suface of metal part. The metal is dipped into a bath of liquid coating (common in galvanizing or electroplating). By electrode, transfer metal ions and deposit on the suface of the part, form a thin metal protective film. Coating is manually applied with a brush for small or detailed work. Powder or liquid is sprayed with an electrostatic charge. Makes the coating particles to adhere to the metal surface. form thin coatings like vapor deposition. Then the metal is placed in a vacuum and the coating material is vaporized and deposited on the surface of parts.
Curing or Drying
After the coating is implemented, it needs to cure or dry. By heat (e.g., baking in an oven) or chemical processes, deposit a thin harder layer film on the surface of the part. This step helps harden the coating and make it durable.
Final Inspection
The coated metal parts are inspected for these visible defects such as uneven thickness, bubbles, pinholes, or incomplete coverage. Proper inspection ensures that the metal achieves a high quality standards.
Metal Casting Part Coating Types
The following listed methods are common metal coating process. In accordance with different requirements from client, we can make some reasonable surface finish. Its aim is to make metal products more durable and solid , and is used for more longer time.
Paint Coating
A simple and cost-effective way to protect metal surfaces from corrosion and wear. Applications: Structural steel, automotive parts, appliances. Good examples Wireless Charger Supporting Base
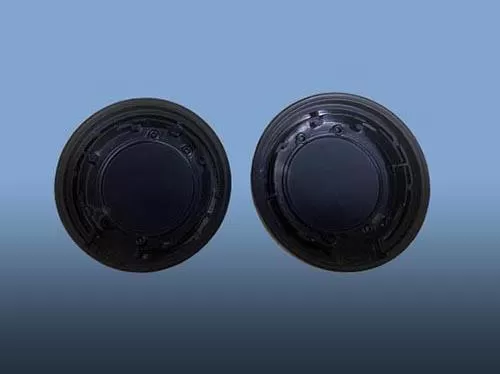
Powder Coating
Electrostatically charged powder (usually polymer) is sprayed onto the metal surface and then baked in an oven by heat, and create a hard, durable surface finish, cover the part. Good example Camera Housing ect are often treated by this process.
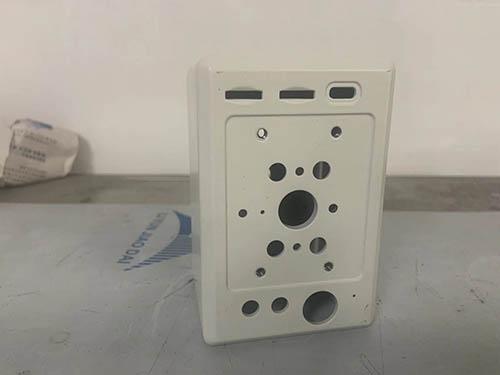
Electroplating
This is Die casting part Electroplating Process. Place both the casting part (cathode) and the metal anode in the electrolyte solution, and ensure the part is fully submerged. Electroplating process is a chemical reaction, Then the metal ions in the solution will be drawn toward the casting part and deposit onto its surface. The duration of the plating process depends on the desired thickness. A longer time produces a thicker coating, so careful not to overplate. In accordance past abondant work experiences, these plated parts will be romoved from electroplating bath after dipping for some time. and dry them in a space place.
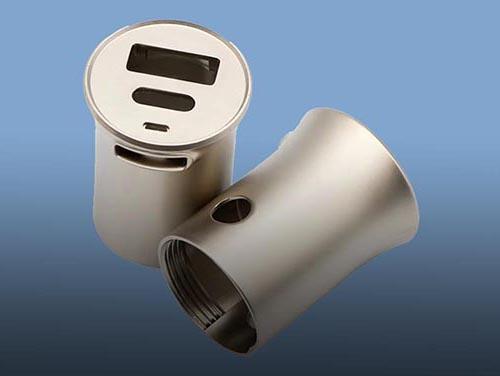
Anodizing
A process mainly used for aluminum. The metal is placed in an acidic bath, and an electrical current is applied, form a thick, protective oxide layer on the surface of part,which enhances corrosion resistance, and can also be dyed for aesthetic purposes. Commonly used in Aircraft parts, consumer electronics, architectural components.
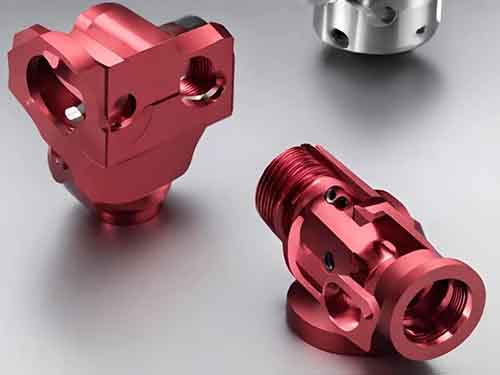
Vapor Deposition (Physical or Chemical)
In Physical Vapor Deposition (PVD), metal is vaporized in a vacuum and then deposited onto the surface of the metal. Chemical Vapor Deposition (CVD) belong to the chemical reaction of gases that deposit a thin film on the surface. Vapor deposition is suitable for Precision tools, electronic components, and optical devices.
Hot-Dip Coating
This method in which metal is dipped into a molten bath of coating material (like zinc or aluminum) ,and form a protective layer. The coating process is used for Galvanized steel structures, automotive components, and roofing materials.
Thermal Spraying
Metal or ceramic particles are heated and sprayed onto the surface of the base metal, and cover a protective layer on the part. That improves wear, corrosion resistance of the part, or its high-temperature resistance. These parts are utilized for Engine parts, aerospace components, pipelines.
Benefits of Metal Coating
- Corrosion Resistance: Protects the metal from rust and strong corrosion in harsh environments.
- Enhanced Aesthetics: Coatings can improve the appearance and appeal aethetics of metal by providing color, gloss, or texture.
- Improved Durability: Coatings increase resistance to wear, impact, and environmental factors. extend part life span.
- Added special functionality: Metal is coated by gold, silver and copper material, enhances electricity conduction of part in electronic and telecommuniction industries
- Reduced Friction: Coatings can make the metal surface smoother and reduce friction in mechanical parts. And also enhances wear resistance.
Conclusion
In Summary,the above coating methods have their own unique characteristic respectively. Each metal coating needs different coating layer depends on the actual applications and functionality of part. The metal casting parts will be treated by different coating process, In some case, metal casting parts coating also allows multi- layers coating and reinforce its coating layer, so that ehance the metal casting parts wear resistance and corrossion resistance in special environments.