Die casting parts surface finishes have multi- methods on surface of casting parts. Include of polishing,electroplating, powder coating, anozide and shot blastering finishes etc. Different surface finish, request different suface preparation , for example, the requirement of powder coating is not so strict, only the surface of casting part is clean and not any dirt or other burr and regardless of smoothness and uneven areas. die casting surface finish levels is not need of strict requirement and standards. But the requirement of electroplate is very rigid, the surface of metal part should be smooth, even area and clean surface. Otherwise, The casting part is no qualified goods, lead to its shorter durability and applications. These die casting parts surface finishes are decided by die casting surface finish design and client’s requirements.
What is The Finishing Process Of Die Casting?
The Finishing Process Of Die Casting is typically the appearance, texture, and smoothness of the surface of the cast part. Diversity surface finishes for die castings, which can be realized through secondary processes, which involve of Polishing, power-coated, plated, anodized, shot blasted, cnc machining, painting and passivation etc. We will choose right surface finish method to treat die castings in accodance with requirements of die castings’ functionality and applications in various industries.
As The follow we list main options for die casting surface finishes:
1. As-Cast Finish
This is the natural finish of metal die casting part directly from the die casting mold. It is original die casting part,which may have a matte or slightly glossy look. These die castings may carry some small burrs ,such as flashing , part lines and sharp edges , it is necessary to do post-process after casting them, and improve its surface finish better.
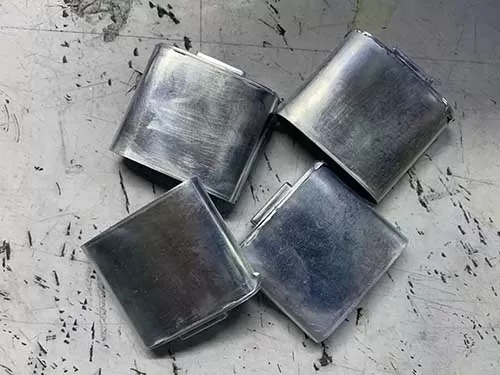
2. Machined Finish
Die casting surface that machined by machining process to gain a higher level of precision and smoother surface finish with very smooth and uniform . The rough surface of die castings should be processed by cnc machining, and ensure fitting the requirement of component installment. Its tolerance is deciced on which functionality and actual usage.
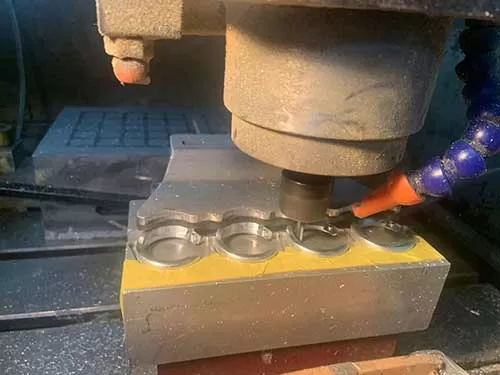
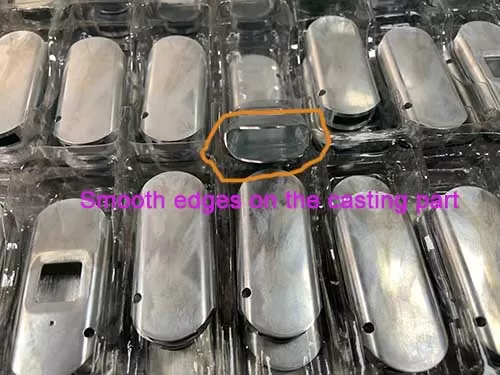
3. Polished Finish
Polishing the die-cast part improves its suface smoothness and gloss . The die casting part polishing process is indispensable in treating the surface of metal casting parts. Such as Glossy, reflective surface, with a smooth texture. These polish finishes effection will be decided by the demand of next surface finish can be proceeded smoothly. Precision electric components, Decorative parts, consumer products like exquisite gift, automotive trim, and other components requiring a sleek appearance.
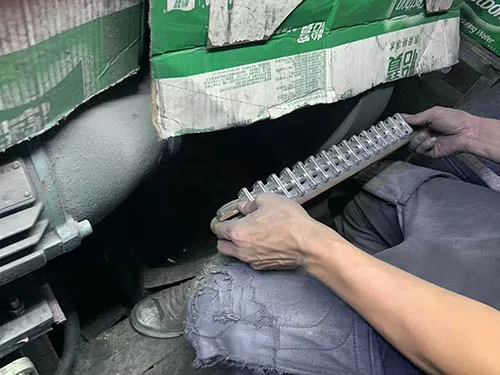
4. Shot Blasted or Bead Blasted Finish
Shot blasting or bead blasting means bombarding the surface with small particles to generate a uniform, textured surface. It is one types of effective treatments that improving the surface of metal die castings. More rugged or matte finish is required, such as industrial equipment, non-decorative housings, and outdoor applications.
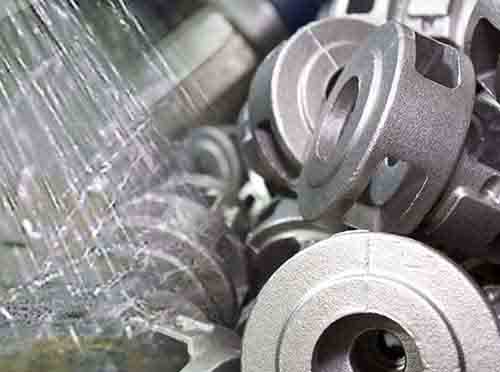
5. Plated
Die-cast parts electroplated have various finishes, such as chrome, nickel and zincto plated enhances corrosion resistance, wear resistance, or aesthetics. Die Casting Parts Electroplate is super surface finish level process method for metal die casting part, coating nickel, copper, gold and chrome on the surface of metal casting parts. These die casting surface finish material is expensive, but the effection is best. It can create a metallic look (e.g., chrome-plated). Consumer goods, automotive parts, and appliances components are all electroplated in real life.
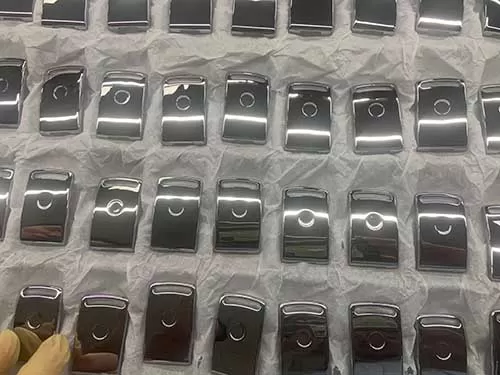
6. Painted or Powder-Coated Finish
Painting or powder coating finish means coating a protective or decorative layer of paint or polymer powder on the surface of the die-cast part. As Metal Casting Parts Coating, Sometimes it also need painted and powder-coated finish in order to prolong the life of the castings and decorative appearance. Powder coating offers a thin, durable protective finish. They are suitable for consumer products, outdoor equipment, and parts exposed to harsh environments.
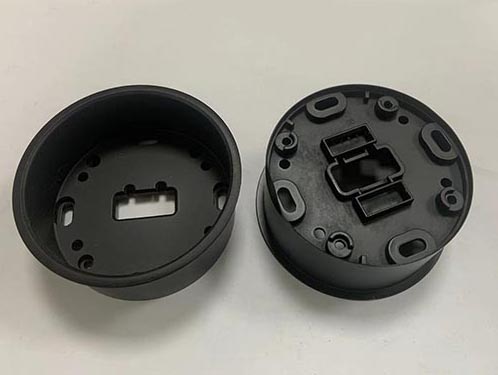
7. Anodized Finish (for Aluminum Die Castings)
Anodizing is an electrochemical process, which create the oxide layer on aluminum die-cast parts. Enhance corrosion resistance and allowing for coloring. Matte to semi-glossy, from natural silver to black, gold, or other custom colors. The matte may need shot blastered to treat contrast matte surface effection. These anodized aluminum die castings are used in Electronics, consumer products, automotive trim, and architectural components.
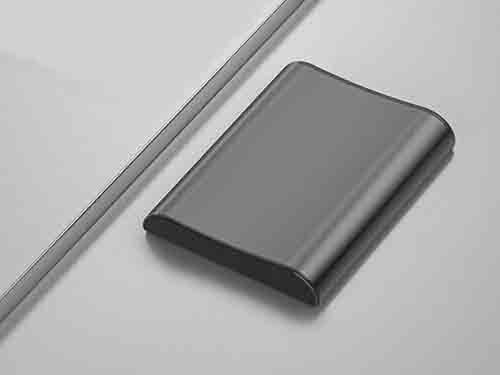
8. Textured or Patterned Finish
Some die-cast parts must carry with specific textured or patterned surface on it directly during the casting process. Text finish is very common surface finish, in term of making texured surface on the cavities of the mold. From sand-like textures to more intricate, decorative patterns or custom logos.
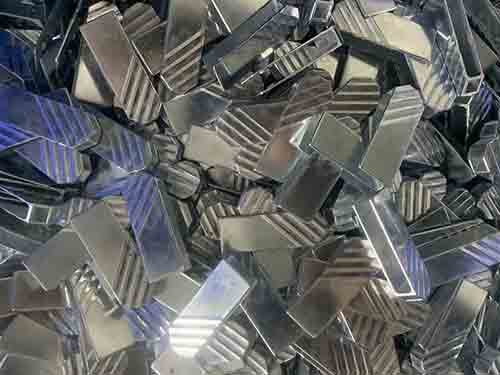
Why Choose TangSheng Die Casting Services ?
Who We Serve
Professional Services and High Quality
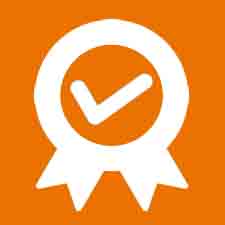
High Quality Parts
Precision casting die and automated streamline high quality parts. And insist on conducting strict quality contol on each process phrase. We permamently maintain 100% inspection.
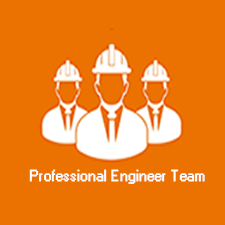
Engineering Team Support
Well-experienced Engineering team supports die casting part and casting die design and precision process for high speed steel die manufacturing. Ensuring mass production in high efficiency in high volume. With consistent high quality product output.
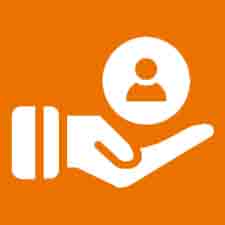
Meet Various Requirement
Meet various requirement of die casting parts in many industries, such as automotive, commnunicatioin, electronic consumer, medical and heavy industrial equipment. The comany passes international industrial authorized certified system,like ISO 9001 and IATF 16949.