In order to seeking for better aesthetic and luxury appearance of gift and decoration product at lower price, people invent to coat a metal layer on the surface of plastic part. The plastic parts electroplating process makes the plastic product looks shiny and more attractive to eyeball. Meanwhile enhance its wear resistant and corrosion resistant in harsh environments. Compare to metal die casting products electroplating, its cost is lower much. So plastic parts electroplating become more and more popular, that is a creative process of surface treatment.
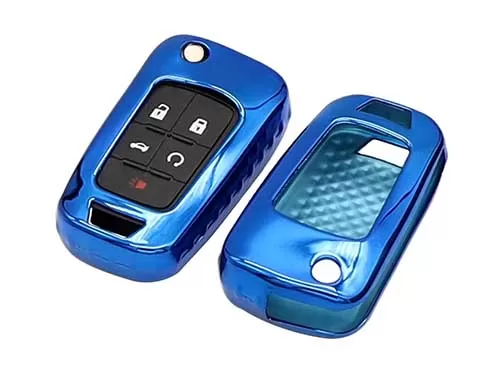
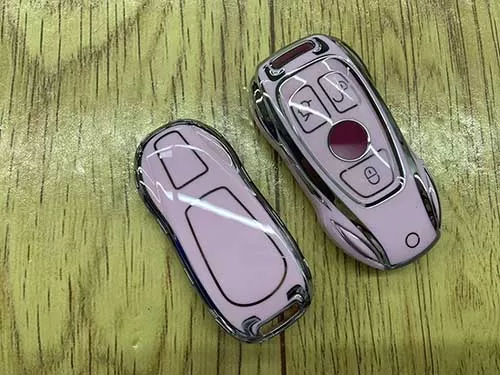
What is Plastic Parts Electroplating?
Plastic parts electroplating is a process for coating a thin layer of metal on the surface of plastic components, typically for decorative, protective, or functional purposes. Of couse this process provides the aesthetic appearance and prolongs the durability and life span of these plastic parts. But maintaining the lightweight and versatile properties of plastic and added other functional properties.
Characteristics of Plastic Parts Electroplating
- Aesthetic Enhancement: Electroplating provides a metallic finish to plastic parts, and makes the plastic more durable. Such as automotive, consumer electronics, and home appliances.
- Enhance Durability and extend life span: The metal coating enhances the hardness, wear resistance, and corrosion resistance of the plastic parts, extending their service life.
- Conductivity: Electroplating can make isolated plastic parts conductive, which is useful in electronics and electromagnetic shielding applications. and prevent or avoid static electricity shock to human being body while applying these electronic consumer products.
Applications of Electroplated Plastic Parts
- Automotive: Electroplating is widely used to create chrome-plated components like grilles, emblems, and interior trim in automotive industry.
- Consumer Electronics: Like mobile phone cases, buttons, and other functional components in consumer electronic. They are all treated to metallic finish, either have a good look or prevent hit human from static electricity shock.
- Home Appliances: Handles, knobs, and other decorative or functional parts of appliances in our home, which are electroplated. And make them more durable and wear resistance.
- Plumbing Fixtures: Like faucets, showerheads, and other fixtures in our daily life. These plastic parts electroplated looks more attractive and luxury.
Electroplating Process for Plastic Parts
The electroplating process for plastic parts is different from that for metal parts. Therefore, several crutial steps are necessary to prepare the plastic surface for electroplating.
Common Plastics Used in Electroplating
. Commonly, Some plastics that bond well with metals are chosen for an excellent and aesthetic apperance of plastic parts.
Common Plastic Types | Character | Applications |
---|---|---|
ABS | Excellent adhesion, | Used in automotive trim, consumer electronics, and decorative parts. |
PC(Polycarbonate) | its strength and impact resistance, Electroplating enhance its hardness. | Suitable for phone casings, automotive parts, and industrial components. |
PP(Polypropylene) | is difficult to plate, but chemically modified PP (with fillers/additives) can be plated. | Used in bumpers, containers, and chemical-resistant parts. |
Nylon(PA) | Require surface activation plating treatment, | Industrial and mechanical parts needing wear resistance. |
PEEK (Polyether Ether Ketone) | high-temperature & chemical resistance after plating | Aerospace, medical, and semiconductor industries. |
Summary
Plastic parts electroplating enhances the appearance, durability, and functionality of plastic components by coating their surface with a thin layer of metal. The difference from metal parts electroplating, it requires additional step that is treated with a palladium or tin chloride solution to make its surface bond to the metal coating. This will increase the cost of plate, but the plastic part is cheaper than metal one, Overall final product cost is still lower. So plastic parts electroplated may be instead of some metal part plated in some cases.