These die casting parts come to the electroplate factory after they have passed a few post processes from the rough die casting parts from die casting machine. If the surface of these die metal casting parts is electroplated there some strict requirements and standards should be executed. and ensuring that its surface should be very smooth, evenly smooth, and without any oxidation, dirt, oil and sand holes. This will ensure that electroplated surface of casting parts is shiny and perfect. So die casting parts electroplating needs a strict required standard.
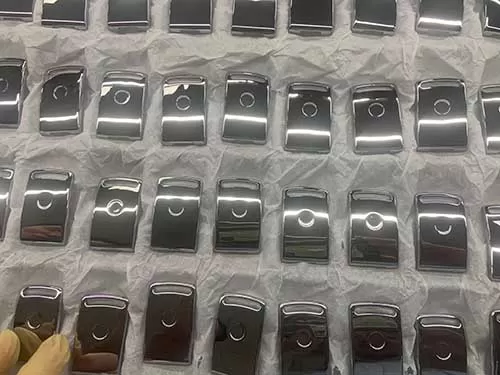
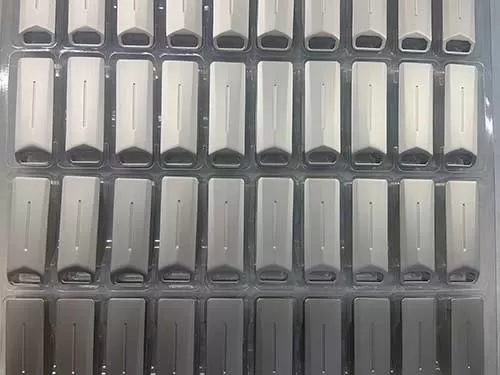
Overview Of Metal Die Castings Electroplating
The Process Of Die Castings Electroplating
Electroplating is the process of coating a metal part with a thin layer of another metal through electrode. That is a chemical reaction procedure. As one essential types of metal die casting part’s surface finishes, We have a general guide on how to electroplate a metal die casting part.
1. Preparing For Die Castings
Firstly Use a degrease agency or solvent to remove any oils, greases, and dirt deposited on the casting part. Then dip the part in an acid solution (like hydrochloric or sulfuric acid) to remove rust or oxide layers. and makes the part suface clean. With water to clean chemical residues on the surface of the part. If necessary, polish the part to achieve a smoother surface, ensuring a good adhension for the plating layer.
2. Choosing The Electroplating Metal
Selecting the follow treatments to do electroplating metal.
Nickel is corrosion resistance and wear resistance, has shiny and matte finish.
Chrome is Often used over a nickel layer. provide a high-shine, durable finish, harder protective film, supperious wear proof.
Copper is used as a base layer or to improve electrical conductivity of the metal part.
Gold/Silver is used for decorative or electronic applications. also some luxury goods.
Zinc provides rust protection.
3. Soak Appropriate Electroplating Bath
After electroplating material is selected, The electroplating for the part will start, We will choose Electrolyte Solution from the follow items
- Zinc (Zn): Cost-effective corrosion protection.
- Nickel (Ni): Wear and corrosion resistance.
- Chrome (Cr): High hardness and decorative shine.
- Copper (Cu): Improves conductivity and acts as an undercoat.
- Gold (Au) / Silver (Ag): Premium conductivity and appearance.
4. Setting up the Electroplating Circuit
Attach the die casting part that you want to plate to the positive terminal of a power supply, Adjust the electricity voltage and current according to the metal type and size of the part. Too high voltage may lead to poor adhesion or uneven plating. While too low current can cause slow deposition and poor adhesion. So we should control electrici current and set up the electroplating circuit depend on the metal type and size of the part .
5. Electroplating Process
Place the metal die casting part and the electroplating material in the electrolyte solution, and ensure the part is fully submerged. Electroplating process is a chemical reaction, then the metal ions in the solution will be transfered toward the casting part and deposit onto its surface. The duration of the plating process decides the desired thickness. The longer time produces the thicker coating, so careful not to overplate. With our past decades work experiences, these plated parts will be romoved from electroplating bath after dipping for some time. and dry them in a space place.
6. Post-Electroplating Finishing
After the electroplating process is complete, we will take the part from the bath and rinse it thoroughly with water. This removes any remaining solution on the part, until the part to dry completely. Sometime you may need to polish the electroplated part to achieve a high-gloss or matte surface finish. A clear protective lacquer or sealant is applied to enhance corrosion resistance or maintain the shine of the part.
7. Quality Control
Check the surface for uniformity, shine, and thickness and bond of the plating. We use micrometers or thickness testers to measure precise accurancy and tolerance. Doing A bond test with common transparent adhesive tape. Carefully look at the plated parts under high light, check if these parts are uniform coating and shine. Maybe find some leak coating areas on the plated parts. This step, we should handle quality control strictly.
The Benefits Of Die Castings Electroplating
Metal Die Casting Parts Electroplating bring more benefits, not only enhances the parts wear resistance and corrosion resistance, prolong their life span, but also improves the appearance and aesthetics of the parts. Whenever zinc die castings or other metal die castings plating, this will improve and enhance the real applications.
1. Improved Corrosion Resistance
The common zinc and aluminum alloy die casting parts we often use, they may expose in the corrosion environment and moisture air. Electroplating them with metals like nickel, chrome, or zinc (through zinc plating or zinc-nickel) provides a protective barrier layer, significantly extending the part’s lifespan.
2. Enhanced Wear Resistance
To enhance the glossy of these metal die casting parts, electroplating chrome, nickel is common surface finish methods. These hard metal desposited on the surface of parts, enhance the impact properties and wear resistance of them. This makes the parts shiny and aesthetics appeal appearance for a long time.
3. Better Electrical Conductivity
In some specific conditions, these metal die casting parts can be plated with copper, silver, gold and other rare metal and improved the parts electrical conductivity. Like connectors in electrical stwich to remain the electric circuit connection and ensure the equipment running smoothly.
4. Improved Aesthetic Appeal
Metal die casting parts used for a wide range, depends on the different functions and applications in various industries. Especially in Consumer electrics and cloth accessoires industries, these die casting parts need an improved aesthetic appeal result. So they may be plated with shiny metal layer and aim to their target.
5. Better Adhesion for Paint or Powder Coating
To reach certain applications for metal die castings, We need add other surface finish on the plated parts. To enhance their suface adhesion for paint or powder coating high efficiency, the parts should be plated with zin metal and produces a better bond with paint or powder coating.