Die casting machines that we often see are mostly belong to hot-chamber die casting machines if main products are all made of zinc alloy material in the factory and enterprise. Zinc alloy can be melt and formed into various shape casting parts at lower temperature and melting points. These casting parts cools and solidifies quickly. Ejecting pins them from the die smoothly. gain smoother surface finish parts with high precision and accuracy dimensions. All of these, due to advantages for casting zinc alloy with hot-chamber die casting machines.
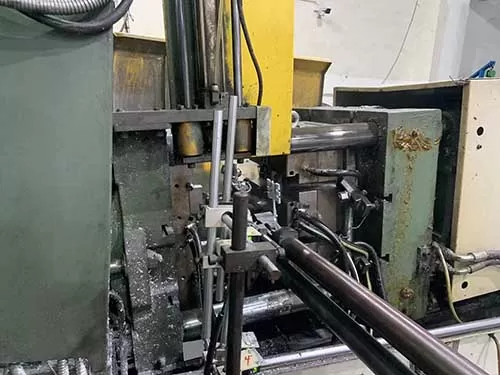
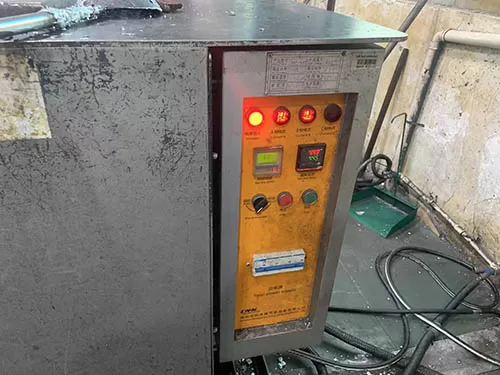
Content of Table
- What is hot-chamber die casting machine ?
- What are advantages for casting zinc alloy with hot -chamber die casting machines ?
- Conclusion
What is hot-chamber die casting machine ?
A hot-chamber die casting machine is a type of die casting machine used in metal casting processes, particularly for metals and alloys with lower melting points like zinc, magnesium, and lead. It is one of the two main types of die casting machines, the other type is the cold-chamber die casting machine. The hot-chamber process is characterized by its high effeciency, dimension stability and suitability for high-speed production of small to medium-size casting parts.
Key Components and Process
Furnace/Crucible: Furnace built in the machine, the molten metal is kept in an attached furnace or crucible. The metal is always kept in a liquid state and ready for casting. The furnace works with electricity power, either eco-friendly or hygienic.
Gooseneck: A “gooseneck” mechanism is immersed in the molten metal. The gooseneck serves as the passage to force the molten metal from the furnace to the die. It is connected to a piston system that drives and injects the molten metal into the mold under high pressure.
Injection System: The piston forces the molten metal from the gooseneck into the die cavity under high pressure. This pressure ensures that the molten metal fills entirely the cavity and maintains high dimensional accuracy and smooth surface finish.
Die/Mold: The mold (or die) is a steel cavity and core of the shape for casting part. Once the molten metal fills the mold, it cools and solidifies, forming the shape of the part.
Cooling and Ejection: After the molten metal is injected, it rapidly cools and solidifies inside the die. The mold is then opened, and the part is ejected from the mold or die using ejector pins.
Hot-Chamber vs. Cold-Chamber Die Casting
Hot-Chamber
- Used for metals with lower melting points like zinc, magnesium, and lead.
- The molten metal is kept in close proximity to the injection system, allowing faster cycle times.
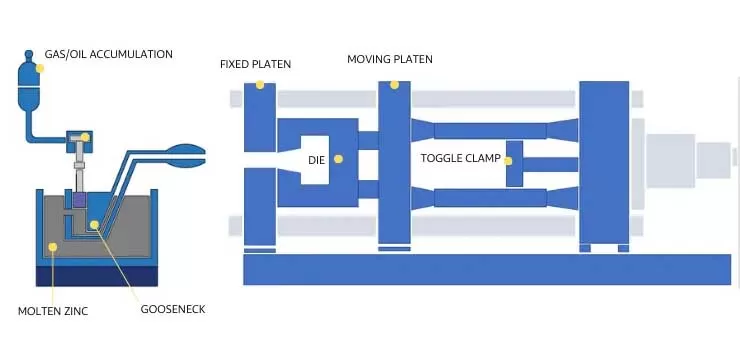
Cold-Chamber
- Used for metals with higher melting points like aluminum and copper alloys.
- The molten metal is manually ladled into the injection chamber from an external furnace, leading to slightly slower production speeds.
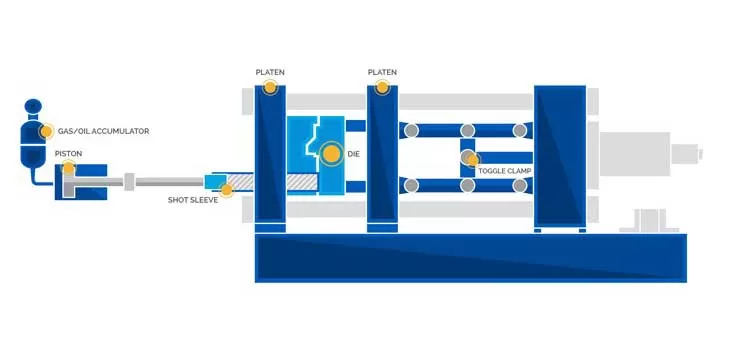
What are advantages for casting zinc alloy with hot -chamber die casting machines ?
Casting zinc alloys with hot-chamber die casting machines offers several advantages that having a best choice for many manufacturing factories. With the enlargement of zinc die casting parts application range, more custom die casting parts in industrial and automotive components are required to process, becuae zinc die casting parts benefits from both cost and design. It includes faster production, cost savings, excellent material properties, and process efficiency. Below are the main advantages.
1. Faster Production Cycle
Hot-chamber machines have fast cycle times because the molten zinc is directly injected into the mold from an integrated furnace. This minimizes downtime between casting cycles. Zinc alloys solidify quickly, further speeding up the production process.
2. Cost-Effectiveness
The rapid cycle times reduce labor and machine operation costs. Because zinc alloys flow easily and fill molds efficiently, the process has fewer rejections and defects, minimizing material waste. Since the furnace is part of the machine and the molten metal remains ready for injection, energy consumption is optimized, making the process more efficient compared to cold-chamber casting.
3. Excellent Surface Finish and Precision
Zinc alloys cast with hot-chamber machines offer excellent precision, allowing complex, intricate shapes and thin-walled parts to be produced without defects. The process results in a high-quality surface finish, which often eliminates the need for extensive secondary machining or finishing operations.
4. Minimal Material Waste
The hot-chamber process allows for the continuous reuse of molten zinc. Any excess metal can easily be recycled, reducing waste and material costs. The precision of the process often produces parts that require little to no additional machining, which reduces scrap material.
5. Compatibility with Complex Designs
Zinc alloys have excellent flow characteristics, which allow for casting parts with intricate designs, sharp edges, and very thin walls that might be difficult or impossible to achieve with other metals or processes. The high fluidity of zinc alloys ensures even distribution of the molten metal, resulting in consistent and defect-free parts.
6. Environmentally Friendly Process
Since the casting process is fast and uses lower temperatures than other metals (like aluminum or brass), it is more energy-efficient. Zinc alloys can be easily recycled, and the casting process itself generates less waste, making it a greener choice for manufacturers.
7. Easy to Realize Automation streamline
Hot-chamber die casting processes are well-suited for automation. It allows manufacturers to streamline production, reduce human intervention, and further enhance efficiency and consistency.
Overall, casting zinc alloys with hot-chamber die casting machines is highly efficient for producing small to medium-sized, high-precision parts, making it a top choice in industries like automotive, consumer goods, and electronics.
Conclusion
Hot-chamber die casting machines are highly efficient for casting zinc alloys due to zinc’s low melting point, excellent flow characteristics, fast cycle times in the unit process and prolong the life of steel casting die. For industries that require mass production of small to medium-sized, high-precision metal casting components to various demands from different fields. With the rise of AI technology, production automation in industrial manufacturing will experience more intelligent operation, the zinc die casting components will be produced in high efficency and stable quality consistence.