We Found that the automotive zinc die casting market had an obvious growth since 2010. Because the requirement of automotive industry was transfering towards lightweight components and ECO-friendly Trendy. As a typical metal material , Zinc alloy had been used across vrious fields in modern industry. Zinc die casting stands out several advantages,which is its excellent mechanical properties, corrosion resistance, and cost-effectiveness and precision process technique. The process is regarded as ideal option for automotive components. When the market is to further expand as electric vehicles (EVs) is account for near half market of automotive sale. Zinc die casting will be applied largely on the electric vehicles. With The creation of automation and advanced manufacturing technologies, automotive zinc die casting market from 2024 to 2025 will have a good development momentum.
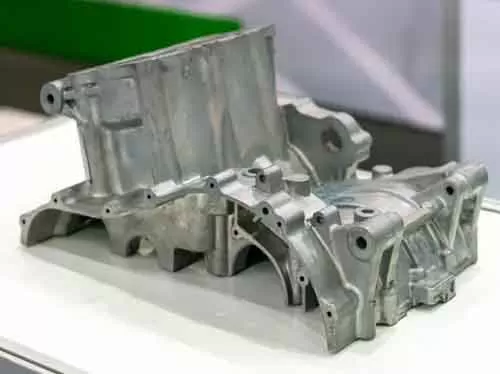
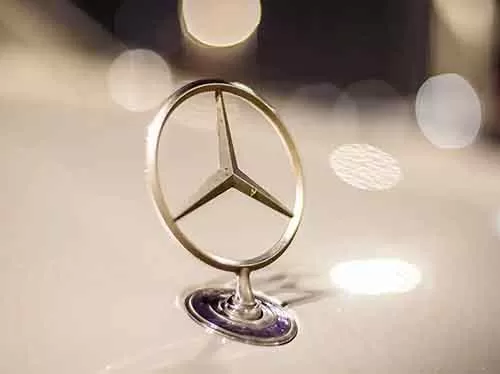
Zinc Die Casting Parts Applications In Automotive Industry In 2025
Zinc die casting parts have been used for various sectors in automtive industy with improvement and innovation of fuel-efficiency car and Electric vehicles. These parts are either bringing cost-efficiency and eco-friendly or providing durable and high performance automotive component. From its utilizition functionality, They will be devided into the below types in automotive components fields.
Transmission Housings
Zinc die casting provides the necessary strength and impact, which is essential for efficient vehicle performance. Compare to aluminum die casting, its cost is lower. This is beneficial to reduce overall price of a car when keeping vehicle high performance . So zinc die casting transmission housing is more suitable for vehicle and car structure.
Engine Covers
These covers benefit due to zinc’s resistance to corrosion and its ability to withstand high temperatures. This metal material, which has its own specific properties, so they are solid and durable. Zinc die casting covers can protect the core part of the car and vehicle well and prevent the engine crashing from dropping weight and impact.
Brackets and Supports
Zinc alloy is so easier to shape intricative zinc die casting parts. Also it is low melt point metal material, which can be melt into liquid material at lower temperature than aluminum one. It can be shaped into intentional shaped precision zinc die casting automotive component, fast cooling , something like this. It also save more labor cost. So it is low cost.
Electrical Connectors and Terminals
Depending on Zinc’s conductivity, along with its corrosion resistance, miniature zinc die casting electrical connectors and terminals are favor of automotive sensor housing and connector. Their properties ensure reliable connections, enhancing overall vehicle performance and longevity.
Door Handles and Lock Mechanisms
Automotive door handles and lock mechanisms are often made from zinc alloy due to its specific properties. These components that experience frequent used and exposure to the air, and uneasy to discolor and nodized because zinc alloy is durability and strong corrosion resistance. Additionally, zinc casting parts can be finished in various ways to enhance aesthetics, as a popular choice for visible parts like door handles.
Heat Shields
Zinc’s heat shield properties may protect sensitive components in automotive sector. These heat shields are common used for the follow applications.
- Heat Shield Panels: These flat or contoured panels protect sensitive components from engine heat.
- Mounting Brackets: Used to secure the heat shields in place, remain effective under various conditions.
- Insulation Plates: These parts may be integrated to further enhance thermal protection.
- Covers for Exhaust Components: Zinc die casting covers help shield specific areas from exhaust heat.
Fuel System Components
Corrosion resistance is crucial here. Zinc die casting is a suitable choice for fuel injectors and fuel line fittings. Automotive fuel system components include the follow components.
- Fuel Injectors: Zinc die castings provide strength and precision for fuel delivery, ensuring efficient engine performance.
- Fuel Line Fittings: These components require corrosion resistance and reliable sealing, This request high precision design and strict structure. Zinc die casting is ideal option.
- Fuel Pump Housings: Zinc die casting is ideal for durable and lightweight housings that protect internal mechanisms.
- Fuel Filter Housings: Zinc’s corrosion resistance ensures longevity and reliability in filtering contaminant vessel.
- Fuel Tank Components: Parts like brackets and connectors have a good corrosion resistance of zinc’s properties for structural integrity and resistance to fuel exposure.
Certainly automotive zinc die casting components,which enhance overall vehicle performance and reliability. Meanwhile zinc casting process are used to make various automotive vital components for reliable applications. These applications highlight zinc die casting’s versatility and effectiveness in meeting the demands of the automotive industry.
Top Zinc Die Casting Manufacturer Provide High Quality Automotive Components In 2025
Top zinc casting manufacturers, TangSheng Hardware Technology will provide complete engineering and design service and high quality automotive components, Although it is one private company only, it has its ability to meet some unique demands, and provides high-quality automotive components. The below advantages as show:
- Advanced Casting Technologies: Renowned for precision die casting and high-performance parts for the automotive sector. Offers advanced die casting solutions with a focus on lightweight components and complex geometries.
- Well-experienced Engineering Team: Specializes in custom zinc die casting design and manufacturing, Accept various OEM and ODM projects.
- Automation streamline production: Advanced die casting machines equipped with smart robitic hands and surface finish post-process precision equiment.
- Strict Quality Control System: ISO 9001 and IATF 16949 , these certificates is based of producing high quality automotive components, so its quality is guaranteed.
The manufacturers focus on precision, durability, and adherence to industry standards, meet optimal performance of automotive components. Our zinc die casting components is to meet automakers requirement, In 2025, Also we will produce high quality and precision casting parts.
Conclusion
Predicting From 2024 to 2025, automotive zinc die casting market is to grow significantly, driven by the demand for lightweight materials and the rise of electric vehicles (EVs). Zinc die casting offers advantages such as excellent mechanical properties, corrosion resistance, and cost-effectiveness. This makes it suitable for critical components like transmission housings, engine covers, and electrical connectors. The market will also benefit from advancements in automation and sustainable manufacturing practices, as companies seek to reduce environmental impact. Overall, zinc die casting is positioned to play a vital role in meeting the evolving needs of the automotive industry during this period.