In the world of plastic injection molding, the production of high-quality parts goes beyond the initial injection process. After a plastic part is injected into the mold and ejected, it often requires additional processing to ensure that it meets the necessary quality standards. One such crucial post-production step is deburring. Deburring plastic parts is an indispensable process because it remove the imperfection burrs that are often created during the molding process. These unwanted burrs or rough edges can impact the functionality, appearance, and safety of plastic parts. This makes deburring a critical procedure in the injection molding process.
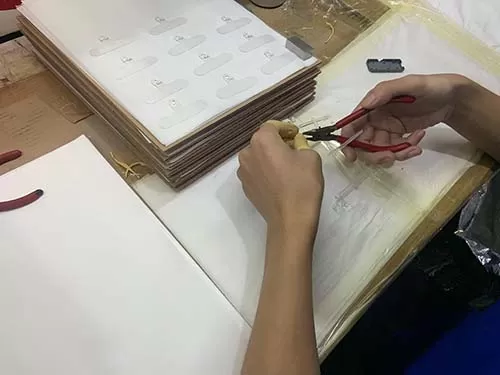
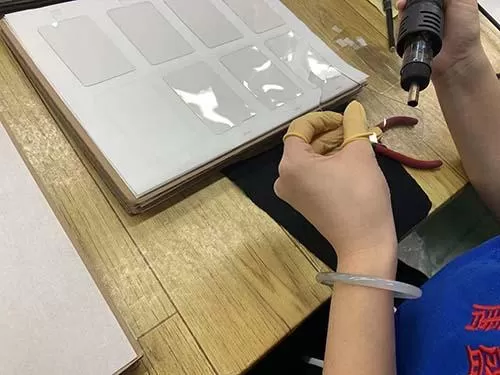
In this article, we will explore the importance of plastic parts deburring process , the methods and techniques employed to remove burrs. The challenges involved, and how deburring plays a vital role in enhancing the quality of plastic injection-molded parts.
What is Plastic Part Deburring?
Plastic part deburring means the process of removing or smoothing out sharp edges, raised areas, or burrs from rough plastic parts. These burrs can occur at various statuses where the mold halves meet, without seamless molding close, lead more flash on the plastic parts or no precision cores and cavities of the mold causes jagged pieces.
Burrs are typically sharp edges, jagged pieces of material that can form along the edges of a part’s surface and thin flash on the parline of the plastic part. They are natural execess of the injection molding process. Burrs can impact the appearance of a plastic part, especially in consumer-facing products. It can cause interference with the fit of assembled components or its functionality. Sharp edges impact safety, especially the area of the part are handled by consumers or workers.
Deburring can improve imperfection parts, ensure the overall quality, safety, and functionality of the plastic parts. Its methods include manual deburring, tumbling deburring, sanding and grinding deburring , thermal deburring and lasering deburring etc. Of course , Which method is chosen, it will be decide by the requirements of plastic parts.
Methods for Deburring Plastic Parts
We are known that deburring plastic parts is an indispensable process. So in Deburring, there are several methods of deburring plastic parts, each of which is suited to different types of burrs, materials, and part designs. Which method selected is depends on factors like the complexity of the part, the material of the plastic, the volume of parts, and the desired level of finish.
Manual Deburring
Manual deburring is a straightforward method. By using hand tools such as knives, files, or abrasive pads to remove burrs, largely improving the appearance and the quality of the plastic part. As a labor intensive process, it is suitable for low volumes or highly intricate plastic parts and prototype making. Flexible control over the deburring process. Time-consuming, inconsistent results, and not good for high-volume production.
Tumbling (Vibratory Deburring)
This process allows placing multiple parts in a tumbler with abrasive media. When the machine vibrates, smooth out the burrs from the plastic part. The fast speed process is suitable for high volumes of plastic parts. Compare to highly complex or delicate plastic parts, which generate rounding of edges if not properly controlled.
Grinding and Sanding
With grinding tools, such as rotary burrs or sanders, remove burrs and smooth edges on the plastic part. This method is suitable for those obvious visible burrs on the surface of the part need to be removed quickly. But the operation should attend extension of grinding, requires skill to prevent over-grinding, lead to damage the parts.
Laser Deburring
It is a high-energy laser beam to vaporize burrs from plastic parts. This process is precise and automated, fits complex, small parts which not easy to handle by hand or for high effeciency mass manufacturing. The precison deburring process is ideal for small, intricate parts with high precision. But it is high cost.
Water Jet Deburring
Using high-pressure water jets to remove burrs from the part’s surface. The process is particularly effective for plastic parts with tight tolerances and complex geometries. By specialized equipment and a water filtration system, under comupter digital control, finish deburring the precison plastic part. The cost of process very high.
Cryogenic Deburring
Cryogenic deburring means that freezing plastic parts in liquid nitrogen, and removing the burrs of the surface of the plastic parts. This method performs well parts with a complex geometry, and is suitable for parts with low thermal resistance. So whether crycogenic deburring is used depends on the material of the plastic part. It also need specialized equipment and has a higher operational costs.
Thermal deburring (TD)
Thermal deburring (TD) is a specialized process used for deburring,improving flash, or other excess material from the partline on the surfaces of parts. This process is often employed to treat those plastic parts are not efficient or precise enough to achieve the desired quality. It need to control the gas mixture or electricity power to generate intense heat burns off burrs and other excess material from a part’s surface. and prevent over-heating cause the deformation of the plastic parts.
Advantages For Plastic Parts Deburring
Deburring plastic parts is an indispensable process, there is several reasons to create rough plastic parts injected from plastic injection machines . Include gated location designed in the plastic injection molding tools. So deurring plastic parts is necessary in post-processing of plastic injection process.
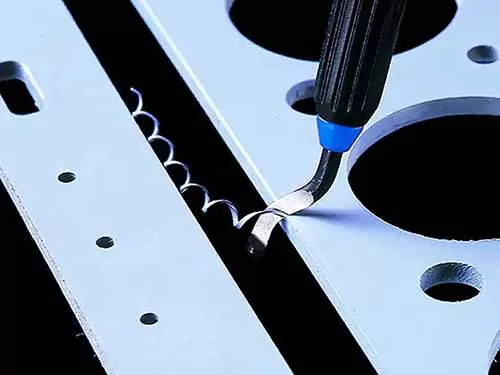
Improved Aesthetics
Burrs and rough edges can negatively affect the appearance of the plastic part, especially when the final product is on market for consumer use. Like automotive components, electronic consumer goods, and toys, As the aspects of safety and aethetics consideraton, removing burrs ensures the part’s aesthetics and a clean, smooth finish.
Enhanced Functionality
When rough plastic part dimension is unproperly, it can’t fit or assembly with other components in mechanical property. The Deburring improve parts functionality, makes it fit together smoothly. Such as gears, locks, or sliders, burrs can create resistance or cause jamming. Removing burrs ensures that these parts perform at their optimal level.
Increased Safety
Burrs can be sharp and cause a risk of injury to users when handling or use of the part. By deburring the edges and the minimize flash on the partline of the plastic part, manufacturers can reduce the risk of cuts, scratches, or other injuries. Like household appliances, toys, or medical devices, which be guaranteed to use safetly.
Compliance with Standards
In mordern industries, such as automotive and medical devices, all have strict quality standards. Burrs can impact the functionality and quality of the product. So deburring is compliance with industry standards, makes the plastic part have a precision dimensions and suitable for assembly with other parts smoothly. The plastic deburring processes should comply with industrial production standards.
Conclusion
Deburring plastic parts is an indispensable process in plastic injection molding that plays a critical role. Want to ensure that the plastic parts are aesthetically appeal, functional and safety for end users, we shoud use deburring process to improve and optimize the quality of the plastic parts. Deburring can remove sharp edges, improve product apperance and functionality, and ensure that parts meet industry standards.