Everyone all imaginates of cnc machined parts when high precision is raised. CNC machining process is controlled and operated by digital control program with precise tolerance is up to 0.1um. But precise tolerance in metal die casting depends on the casting die’s precision. Especially like many precision components for automotive, electronics, telecommunication and medical industries. With its unique properties, zinc die casting process offers exceptional dimensional accuracy, superior surface finish, and remarkable mechanical strength. So Applications Of High Precision Zinc Die Casting Components have a wide range.
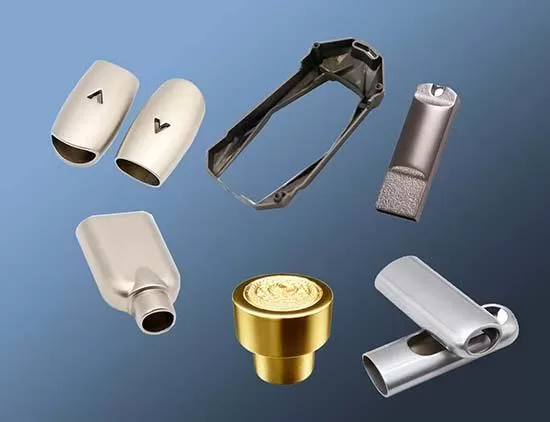
Applications of High Precision Zinc Die Casting Components
High-precision zinc die casting components are widely utilized across various industries. From automotive and electronics to medical devices and telecommunications. Zinc die casting delivers reliable solutions for intricate and demanding applications. Below are some applications of high-precision die casting components in various sectors.
Automotive Industry
Structural Parts: Engine blocks, transmission housings, and chassis components and battery housing.
Aesthetic and Functional Features: Door handles, decorative trims, emblems and car logos.
High-Performance Components: Turbocharger housings, sensor brackets, fuel router fittings and gearbox components.
Electronics and Telecommunications
Heat Management: Heat sinks for processors, LED housings, and power modules.
Casings: Enclosures for routers, set-top boxes, and communication devices.
Connectors and Hardware: Precision connectors,terminals, mounts, and brackets.
Medical Equipment
Device Casings: Enclosures for diagnostic tools, imaging equipment, and portable devices.
Supportive Components: Precision brackets and base for medical machinery.
Implant-Related Devices: Components requiring high biocompatibility and accuracy.
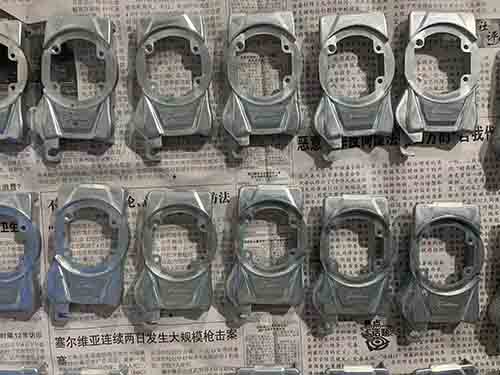
Aerospace and Defense
Lightweight Structural Parts: Aircraft seating components, housings, and control panels.
Critical Components: Radar housings, missile casings, and avionics enclosures.
High-Strength Parts: Landing gear housings and precision fuel delivery systems.
Industrial and Construction Equipment
Machinery Components: Housings for motors, gearboxes, and pumps.
Automation: Precision parts for robotic arms and conveyor systems.
Heavy Equipment: Brackets, clamps, and custom-fit components for heavy-duty machinery.
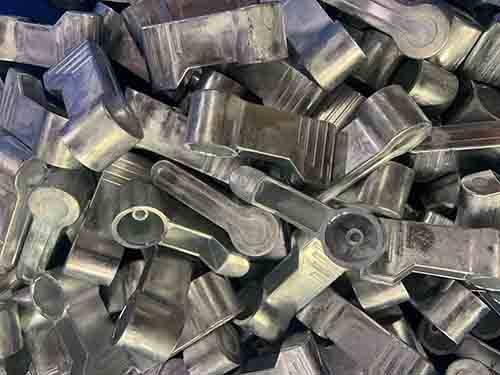
Consumer Goods
Appliances: knobs and buttons for washers, dryers, and kitchen equipment.
Handheld Devices: Casings and intricate supporting parts for cameras, watches, and tools.
Luxury Goods: luxuray parts for jewelry and decorative hardware.
Energy and Renewable Technologies
Wind Turbines: Lightweight structural components and connectors.
Solar Panels: Frames, mounting systems, and heat sinks.
Battery Packs: Enclosures and connectors for energy storage solutions.
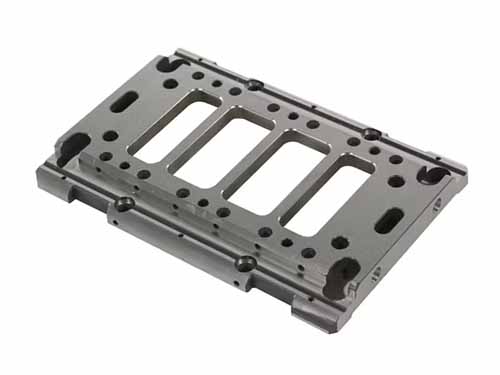
From the above information, we learned that high precision zinc die casting components have been utilized widely in many industries and fields. Zinc die casting components become more and more popular in people work and life. Their manufacturing cost is lower , compare to other casting metal, such as aluminum and copper, even stainless steel. With its special metal properties, zinc die casting components have been used largely in automotive, communication, medical device, aerospace and defense, Industrial equipment and furniture. This is an big business opportunity for zinc alloy die casting parts manufacturers. They need producing high quality and high precision zinc die casting products to meet the demands of market and clients.
Tscasting Technology Provide Custom High Precision Zinc Die Casting Services
Tscasting technology is one of professional die casting factory, which is specializing for zinc and aluminum alloy die casting services. Equipped with well-experienced engineering team, advanced die casting machines and automatic production line, complies with quality management of IATF 16949 strictly, and produces diversity custom high precision die casting components.
Tailored Design
Customization design for client requirements , involves unique dimensions, geometries, and functions. It can need complex shapes, thin walls, or intricate details. Designer and engineers have a continuous improvement and modification for product and mold until fitting the spefications of customer completely.
Special Material Requirements
Casting specific metals or alloys (e.g., zinc, aluminum, magnesium), The casting die withstands repeative wear and high temperature during mass production. The special Material of the die casting part should conform with custom part’s functionality, practise applications and being assembled reasonably.
Tight Tolerances CNC Machining
High precision to ensure the part fits seamlessly with other components in an assembly smoothly. If neccessary , cnc machining turns, mills and tapers some custom parts to meet the specific requirements of tight tolerance.
Fine Surface Finishing
Some advanced finishing processes like powder coating, polishing, or plating for enhanced appearance and durability. Some reasonable process methods to achieve client demand. To minimize further post-process, we can polish the surface of the cores and cavities of the mold, and enhance smoothness on surface of die casting part and ensure as-cast surface finish fine.
Conclusion
When industries demands high-precision die casting components, zinc die casting is undoubtedly the best choice. Its combination characteristics of dimensional stability, surface finish, and mechanical properties make it popular manufacturing processes. Such in automotive, electronics, or medical applications fields, zinc die casting consistently delivers high-quality components to the market. Zinc Die Casting Process Offers High Precision Die Casting Components. In order to ensure that manufacturer can produce high quality zinc die casting components , we also guide them to have a matured technique. Please refer to What is Zinc Die Casting Components Design Guide, Step By Step.