Every one knows that hot chamber die casting has emerged as a premier method for producing high-quality zinc components across various industries. Certainly this technique offers numerous advantages, including rapid production cycles, exceptional dimensional accuracy, and the ability to create intricate designs. In this article, we will let you know that the hot chamber die casting process, its benefits, and highlight some leading manufacturers specializing in zinc die casting. That is Hot Chamber Die Casting Machine Produces High Quality Zinc Casting Parts is the best choice.
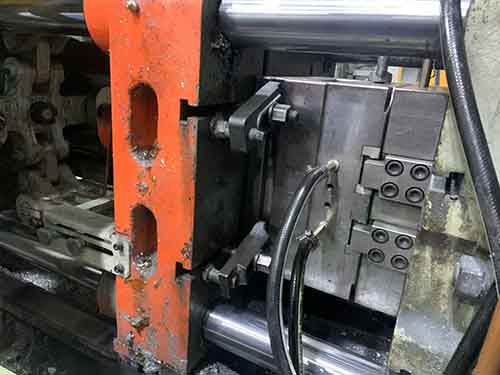
What is hot chamber die casting ?
Hot chamber die casting is a manufacturing process that producing precision metal components by injecting molten metal into a steel mold under high pressure. Particularly suitable for metals with low melting points, such as zinc, magnesium, and certain lead alloys. The manufacturing process is highly effective and cost efficiency, It handles high-volume production for small to medium-sized parts with intricate geometries. The process have the below obvious features as the follow.
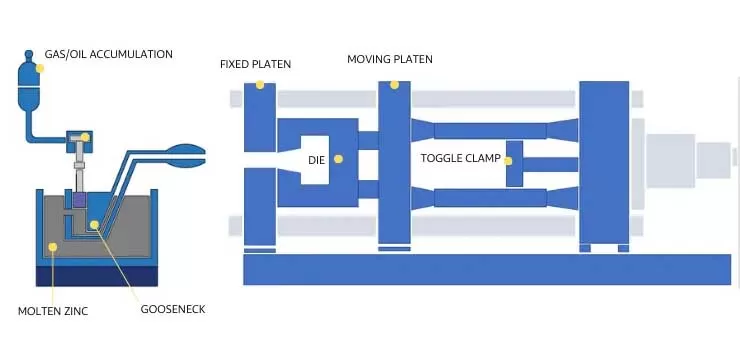
Steps in the Hot Chamber Die Casting Process
Integrated Melting System: The furnace is intergrated with the die casting machine. Then the molten metal in the internal heating pool, ready for casting parts, maintain steady temperatures
Gooseneck Mechanism: A metal delivery system (gooseneck) is submerged in the molten metal. So the gooseneck channels the molten metal into the mold during the injection phase.
High-Pressure Injection: A hydraulic-powered piston forces the molten metal through the gooseneck into the mold. Moveover the pressure ensures the metal fills every detail of the mold, and forms high precision cast part with fine surface finish .
Rapid Cooling and Ejection: Once the molten material fill the detial of the mold, through proper cooling mechanisms, the metal is cooled and solidied into intented shaped cast parts. The mold opens, and ejects the finial casting part out from the mold.
Applications of Hot Chamber Die Casting
Automotive: Sefety settings, Decorative trims, engine components and brackets
Consumer Electronics : housing, connector, sensor enclosure, smart devices components.
Medical Equipment: Precison measurement instruments and diagnostic device components
Furniture: Locks, handles, decorative components
Hot chamber die casting is widely used across various industries for products with precision and durability. The process is a vital manufacturing process for creating high-quality, complex zinc and magnesium alloy parts in high efficiency and mass production. So this streamlined process allows for quick cycle times and high-volume production. Especially it is ideal for manufacturing small to medium-sized zinc components with complex geometries.
Advantages of Hot Chamber Die Casting for Zinc Parts
Using hot chamber die casting to produce high quality zinc casting parts brings several significant benefits. The typical process can create various kinds of custom die casting components, which meet the specific demands and functionality in automotive, electric telecommunication, mechanical equipment and medical instrument fields. Its unique features are shown as the below.
High Production Efficiency: The integrated design of the hot chamber machine enables rapid cycling, which is suitable for the process of low melt points alloy material. It leading to increased production rates.
Excellent Dimensional Accuracy: The high-pressure injection ensures precise replication of intricate designs, resulting in parts with tight tolerances and smooth surface finish.
Smooth Surface Finish: The process produces parts with smooth surfaces, reducing the need for additional finishing operations.
Material Recyled and Reuse: The ability to reuse excess molten metal minimizes waste, making the process cost-effective and environmentally friendly.
Versatility in Design: Hot chamber die casting allows that the die casting parts have complex shapes and thin-walled sections, providing designers with greater flexibility.
Fast cast cycle: The speical manufacturing process can provide fast cast cycle, and either saving energy consumption or lower the overall cost of zinc die casting components in sales.
Leading Zinc Die Casting Classic Cases
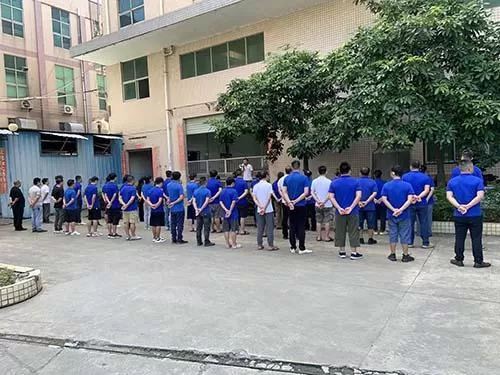
Hot Chamber Die Casting Machine Produces High Quality Zinc Casting Parts. Our High quality zinc casting components and goods are focus on miniature parts, include of communication electronic components and decoration parts and consuption goods. Then the follow classic cases reflect our exquisit technique and consideration service.
- Car Key Cover Case
- Car USB Charger Display Panel Case
- USB Flash Drive Disk Case
- Camera Housing Project Case
- Switch box Project Case
- Wireless Fast Charger Supporting Base
- Exquisite Metal Aromatherapy Cover
- Wrapping Rubber Zinc Die Casting Ball
Conclusion
Hot chamber die casting is the best option for producing high-quality zinc components. It offers unparalleled efficiency, precision, and versatility. So its ability to produce complex shapes with excellent surface finishes makes it indispensable across various industries . Such as automotive, communication, goods consumer industries. Advantages of Hot Chamber Die Casting for Zinc Parts makes zinc die casting components applications and functionalites completion. With the typical manufacturing process technique, manufacturers will produce diversity zinc die casting comonents to meet and fill the requirements of the modern market.