Nowadays, zinc die casting parts have been used widely in various industries and fields, Much more zinc die casting manufacturer need produce more high quality zinc parts to meet the demand of market. But they encounter some technical problems to be resolved. Porosity is one of the most common challenges faced in zinc die casting. It can significantly affect the structural integrity, functionality, and appearance of die-cast parts. For manufacturers aiming to produce high-quality zinc die-cast parts, reduce porosity on the zinc die casting parts. How to reduce porosity on zinc die casting part casting during the process of zinc die casting parts? This guide provides a detailed explanation of porosity, its causes, and practical strategies to reduce it.
What Is Porosity on Zinc Die Casting Part Casting ?
Porosity on zinc die casting part means the presence of small voids, holes, or air pockets on the surface of die castings. These voids can occur during the die casting process and different sizes, their range from microscopic pores to visible cavities. Porosity is a common defect, which can significantly impact the structural integrity, functionality, and appearance of the cast part. When we found porosity on the surface of zinc die casting part, which hint us that the zinc die casting part structure have become so unstable and reduce the cast part anti-pressure and present its rough surface finish.
Types of Porosity on Zinc Die Casting Part
Denpends on visible porosity on the cast part that we look in, Porosity on zinc die cast parts generally falls into three main categories:
Gas Porosity
Trapped air or gases causes these small voids on the surface of the zinc die castings during the injection of molten zinc into the mold cavity. Its characteristics: Small, spherical voids often near the surface of the part. This can impact the cast part mechanical structure and the defect of appearance.
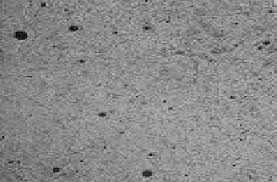
Shrinkage Porosity
When the cast part accepts uneven cooling and solidification of molten zinc, leading to voids where the metal has contracted. These irregularly shaped voids typically found in thicker sections of the cast part, even more lead to the cast part hollow inside it. Rigid impact the integrated structure of the part and warping.
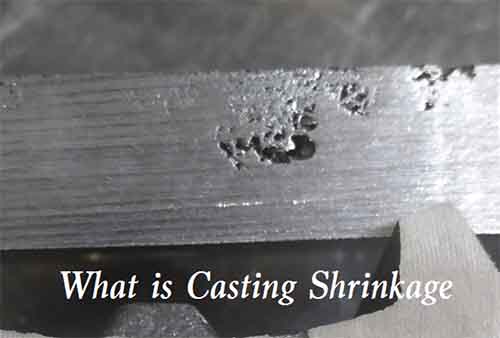
Vacuum Porosity
Inadequate venting in the mold can’t escape the trapped air or gas from molten zinc under high pressure, Some voids may appear deep on the surface of the cast part. It affects part strength and performance, especially in critical applications.
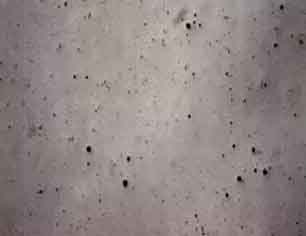
Why Causes of Porosity in Zinc Die Casting Part Casting
Before resolving the problem, we firstly learn How are Zinc Alloy Die Casting Parts Shaped. In accordance with the process of zinc die casting parts, several factors contribute to porosity during the zinc die casting process.
Improper Mold Design
Insufficient venting and overflow channels. and lead to the trapped air or gas inside the molten metal, can’t overflow on the surface of the cast part. Poor gate design causes turbulence in molten metal flow. Or fill the mold detail uncompletely and cause defect cast part.
Inadequate Process Parameters
Incorrect injection pressure or speed leading to air entrapment. Lead to porosity cast part generated during die casting process. Inadequate temperature control of the molten zinc or the die, makes the cast part shrankage and warping.
Impurited Material Issues
Impurities or contaminants in the zinc alloy causes various porosity issues on the die casting part. Presence of dissolved gases in the molten metal, should be escaped by proper venting and overflow method.
Uneven Cooling and Solidification
Uneven cooling rates can cause shrinkage voids, make the cast part warpping. Thicker sections in the part design leading to differential cooling. Uniformly cooling overall the cast part causes cold shut, warping and flow marks .
The above several points is most easiest to cause the porosity on zinc die cast part. You should check these points mainly once there is porosity on zinc die casting part, take some necessary measture to resolve it, and ensuring that the high quality zinc die casting components are finished.
Practical Guidelines to Reduce Porosity On Zinc Die Casting Part
1. Optimize Mold Design
Improve Venting and Overflow: Incorporate proper venting channels to allow trapped air and gases to escape. Place overflow reservoirs strategically to collect excess molten material and impurities. The furnace reserviors hold the molten zinc material, naturally escape excess trapped air in molten zinc and filter the impurities in zinc material, but if the trapped air produce during die casting process, improving venting and overflow channel to escape the trapped air from the formed part and finish a fine final product.
Focus on Gate Design: Position gates to minimize the distance molten metal travels, reducing the risk of air entrapment. Avoid the molten metal material turbulance or uncomplete filling in the cavity of the mold, lead to the defect cast parts causing.
Design for Uniform Cooling: Avoid sharp corners and uneven wall thicknesses that lead to inconsistent cooling and shrinkage porosity. Use cooling channels to maintain an even temperature throughout the mold. This need add some proper cooling channels to offer uniform cooling throughout of the mold when the part solidified in the mold.
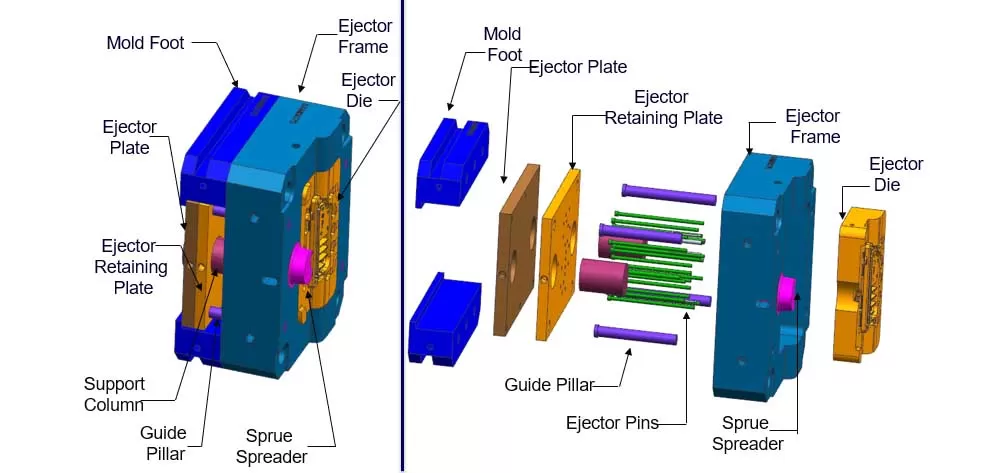
2. Control Process Parameters
Handle Injection Speed and Pressure: Require high injection speeds to fill the mold quickly, ensure the detailed areas of the cast part can be cooled uniformly. Meanwhile, Optimize pressure to ensure the mold cavity is filled completely without air entrapment, and makes create a fine surface finish of the cast part.
Temperature Control: Maintain an optimal temperature for the molten zinc alloy to flow freely. And make the molten zinc alloy fill the mold completely quickly. Preheat the die to avoid premature cooling and shrinkage porosity during the process of die casting. Cooling channels can offer unifom cooling for the even areas of the cast part.
Cycle Time Optimization: Fine-tune cycle times to ensure adequate cooling without causing stress or defects. The uniform heated mold accept even cooling, and create the fine surface finish and high quality integrated structural cast part.
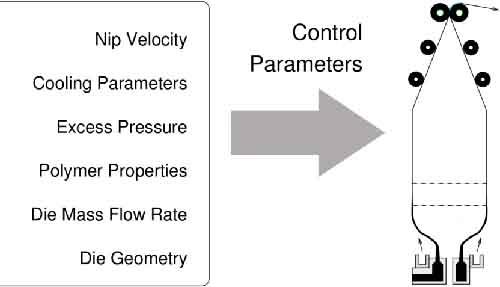
3. Improve Alloy Quality
Impurities in the alloy can release gases during casting, leading to porosity. We should select certified, clean alloys minimizes this risk of porosity on the die castings. Proper grain refiners can improve the structure of the zinc alloy, reducing the chances of shrinkage-related porosity. Sometimes we may use degassing agents or equipment to get rid of dissolved gases in molten metal before casting. Improve alloy quality helps reducing the porosity defects on zinc die castings.
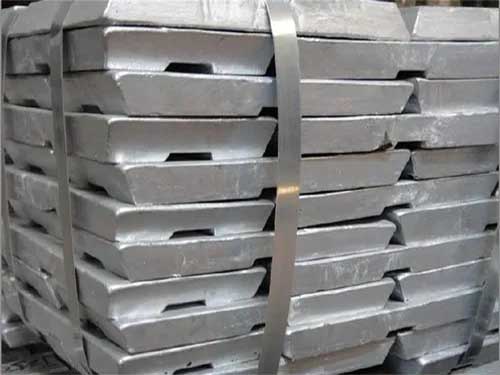
4. Introduced Advanced Technologies
Simulation Software: With the assistant of advanced technology, we can use computer-aided engineering (CAE) software to simulate metal flow, cooling, and solidification. This helps identify potential porosity issues and optimize mold design, Especially venting and gating position, and escape trappered gas in the molten alloy effectively.
Real-Time Monitoring: Install sensors to monitor temperature, pressure, and flow during the casting process. Real-time data allows us to implement some immediate adjustments to prevent porosity. and handle proper operation parameter, and reduce porosity problems on zinc die castings and maintain a smooth mass production.
5. Implement Quality Control Rules
We can use X-ray or CT scanning to detect all porosity and ensure consistent quality. Perform leak testing on pressure-tight parts to ensure no defects are present. We carefully analyze rejected parts to identify trends and root causes of porosity, implement corrective actions to improve the mold and die casting technique and consistently provide high quality die casting components.
Conclusion
To reduce porosity on zinc die casting part, we need a combination of optimized mold design, precise process control, high-quality materials, and advanced technologies. By tracing the root causes of porosity, and implementing the strategies of Practical Guidelines to Reduce Porosity On Zinc Die Casting Part. Consistently enhances our quality ideas, and produce high quality zinc die casting components. Meanwhile manufacturers produce higher-quality zinc parts, and stay competitive in a demanding market, they aiming to improve, continuous learning, innovation, and quality assurance are key to achieving defect-free production and meeting customer expectations.