Zinc die casting had become an indispensable process in the automotive industry. The process enables create high-precision, durable, intricate geometies and cost-effective components. With its unique properties, zinc alloy die casting contributes to the efficiency, safety, practicial applications and aesthetic appeal of modern vehicles. Let’s explore applications of zinc die casting in the automotive industry and understand why this material is so popular.
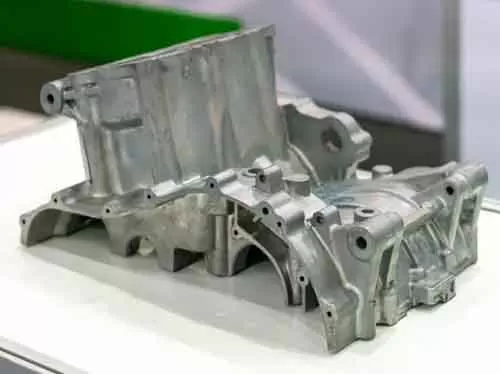
Applications Of Zinc Die Casting In Automotive Industry
1. Structural Components
- Engine Mounts and Covers: Zinc die casting provides excellent dimensional tolerance and strong strength automotive components, which is suitable for engine mounts, gear covers. These zinc die casting components endure high stress, vibration and impact, and own strong corrosion resistance agaist acid lubrication oil.
- Transmission Housings: These parts require excellent heat dissipation and precision. Zinc die casting allows intricate shaped transmission housing and good heat dissipation. Also they can withstand vibrations from gearing running and corrosion from damp enviroments and worse weather, and protect the transmission mechanism well.
- Electric Components: Zinc die castings can shied electronic magnetic inferance, ensure the monitoring system smooth running. They are excellent strength-to-weight ratios and corrosion resistance. And protecting core electric components and endure harsh environment and worse weather.
2. Interior Components
- Dashboards and Instrument Panels: , Some metal die casting display panels and housings for aesthetic and ergonomic design in automotive interior decoration. Depends on Anthropology design of car and vehicle, custom cast panels and housing are created with zinc die casting.
- HVAC Components: These precision zinc die castings ensure heating, ventilation, and air conditioning systems works smoothly. like air conditioner compression electric magnetic circle enclouse, compression machine housing.
- Switchgear and Knobs: Zinc die casting creates flexible appearance design, complex integrated structural and stylish components such as control knobs and switches. with various custom design shapes, which commonly decorate the interior design and functional operation in central console in car. If neccessary, these zin die castings can be plated and enhance their durability.
3. Exterior Components
- Door Handles and Antennas : These parts require a combination of aethetics, resistance to wear at high frequency and durability. They withstand repetitive handling when open the doors. And They accept worse weather environment and strong corrosion resistance.
- Grilles and Emblems: Automotive grilles and brand emblems are commonly small and medium size. Maybe they need intricate designs and superior plating option. Zinc die casting is best option. Either create desired design geometries or having a smooth surface finishing, and easier to be plated and generate shiny attractive.
- Lighting Components: The housings for headlights and taillights due to their precision and unique design. But also these lighting housings can withstand environmental exposure in harsh environment and worse weather.
4. Safety and Security Components
- Seat belt Mechanisms: Zinc alloys’ high tensile strength and precision casting is favor for miniature die casting parts. Like seat belt buckles and locking mechanisms. According to passenger safety consideration, diversity zinc die casting safety buckle and plugers are cast.
- Airbag Housings: Zinc die castings provide the flexible design and dimensional accuracy airbag enclosure and housings. It also fits airbag deployment systems. And Ready for safety airbags for drivers and passengers accidents.
- Locking Systems: Components in door and ignition locks are made from zinc alloy. Depends on the automotive interior design, custom design ignition locks are commonly. They can endure wear resistance and anti-corrosion properties.
5. Electronic and Electrical Components
- Sensor Housings: Zinc alloys housing protects sensitive electronic components in harsh conditions and good heat resistance. This ensures their functionality and longevity. Meawhile It can sheild electric magnetic inference from the sensitive electronic components, and transmit the accurate monitoring data to centrel console in car.
- Connector Components: Electrical connectors benefits come from zinc’s electricity and thermal conductivity. These precision, intricate design miniature parts can connect and close the control electric circuit. And ensure the moudle electronic unit can work smoothly.
- Electric Vehicle Components: With the rise of EVs, the demand for zinc die cast parts in battery casings, motor housings, and thermal management systems are increasing rapidly. More custom zinc die casting projects should be planned in automotive manufacturing field.
Advantages of Zinc Die Casting in Automotive Industry
The widespread applications of zinc die cast parts in the automotive industry reflect several advantages. This needs that more zinc die casting components meet various demands in automotive sectors.
High Precision and High volume Production: Zinc die casting has intricate designs with tight tolerances, ensuring consistent quality. Its casting die can conduct a high volume production and allow a fast cast cycle.
Strength and Durability: Zinc alloys offer excellent mechanical properties, and high toughness,is suitable for high-stress applications. And zinc die casting can produce high quality products with high strength and durability.
Cost-Effectiveness: Zinc die casting minimizes material waste, energy saving in mass production and advanced die casting machines, reduces overall manufacturing costs. Especially It lower melting points saves heating energy by electrictiy power and cooling and solidifying quicky in each cast cycle, and enhance mass production rates.
Design Flexibility: The design in flexiable or surface finish in various styles to enhance the vehicle’s appearance. With cutting-edges 3d design software tools, our engineers can design high precision metal 3d model with intricated appearance and integrated structure.
Corrosion Resistance: Zinc alloys naturally resist rust and corrosion. This makes zinc die casting automotive components all have a strong corrosion resistance although exposing in aid moisture air and marine area with salt humidity.
Casting tight tolerance dimensional small size cast part: Zinc die casting allows for manufacturing high precision tooling steel die for mass production in high efficiency. Our mold technician often process the steel die with cnc equipment and precision instruments, so casting tight tolerance dimensional small cast part ensured.
Conclusion
Zinc die cast parts are playing a vital role in the automotive assemblies. It can offer a balance of strength, precision, and affordability. From structural components, interior and exterior practical components, intricate electronic housings to safety and security components, zinc casting components play a crucial role in different automotive sectors. With automotive technology leap, more custom zinc die casting components are required to assemble with automation control mechanism, create more intelligent pravite car and business passenger vehicles.