In the world of metal parts manufacturing, zinc alloy die casting is playing a significant role in industrial manufacturing. It offers high precision, durability, and cost-efficiency metal casting parts. As industries evolve, the die casting manufacturing must follow the development of new technologies. We should meet market rapid growth demands, and keep sustainability goals in evironmental management and consistent high quality zinc die casting components to deliver for newly industrial rising. In 2024, 5 trends on Zinc Alloy Die Casting’s Innovation And Growth is seeked for by die casting manufacturers. This article predicts these trends in detail.
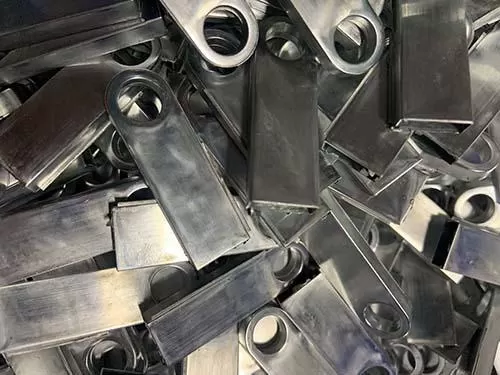
5 Trends On Zinc Alloy Die Casting’s Innovation And Growth
1. Zinc Alloy Die Casting Will Become Automation and Smart Manufacturing
With the rise of Industry 4.0 development, Increased automation and smart manufacturing technologies are replacing the technique of old type industrial manufacturing process. The manufacturing technique is upgraded continueously, especially zinc alloy die casting process is experiencing a severe challenge. What’s more, zinc alloy die casting component accuracy become tighter tolerance and smart manufacturing . It main reflect the below points.
Robotics and Smart manufacturing System Required: Automated robotic systems are increasingly being used in die casting processes. Either enhances accuracy or reduces human error and body accidents or ensures consistent quality cast parts in high volume production. By Artificial intelligence (AI) algorithms, optimizing some vital parameters, such as mold temperature, injection speed, and cooling time, resulting in high casting quality and cost-efficiency.
Predictive Data Monitor: Sensors and IoT devices collect casting machines real-time performance data. Depends on the data display changes during die casting process, we can have a predictive improvements and adjustments in time.
Ahead simulation Test : The adoption of digital casting process simulation and test casting processes in a virtual environment before production. By computer software system, setting required action parameters and test a virtual die casting process operation, and look in any changes,Trouble-shooting some potential problems ahead, reduces trial-and-error costs.
2. Focus on Sustainability and Cycle Economy
People insist on industries worldwide sustainability goals in order to balance between technology development and humen life. Zinc alloy die casting follows eco-friendly purpose, aim to reduce carbon emissions and promote resource conservation. As special metal material, which can be processed into various geometries. Even more its waste can be recycled when they become useless. So the zinc is sustainable and economic. There are a few obvious characteristics.
Recycled Zinc Usage: Zinc is 100% recyclable material. Manufacturers can use recycled zinc parts in die casting. This reduces carbon emission and resource conservation. When the zinc casting part lost its mechanical functions and applications , they can be recycled and reused to melt. And cast and form other parts for other applications with less impact to the environment. Zinc alloy die casting just realizes the positive energy cycle economy.
Energy-Efficient Processes: Using Lower temperature melting furnaces and energy-efficient casting machines, by the unique die casting approche, high efficiency produces plenty of the part with intricate design geometries and steady dimensions.
Waste Reduction: Advanced mold designs, precise injection systems and automatic streamline process reduces material wastage during production. This process is sustainable in environmental protection. These precision casting die and hot chamber die casting machine also enhances production rate.
3. Meet The Growth in Electric Vehicle (EV) and Automotive Applications
In current automotive industry, the rapid growth of electric vehicles (EVs) is creating a new business opportunities for the demand of zinc die casting parts. Rely on zinc good mechanical strength, durability and cost-effective properties, Zinc die casting components are used in large scale in Electric vehicle automotive applications. The follow sectors in automotive industry have a clear description respectively.
Lightweight Components: Automakers are optimizing lightweight materials to enhance vehicle efficiency. Zinc alloys have their excellent mechanical strength and durability. They are made as critical EV components such as connectors, housings, and heat sinks. This is a rare good chance or great challenge for much more zinc alloy die casting manufacturers.
Thermal Management Solutions: The demand for EV battery cooling systems need the enclosures and housings with corrosion resistance and thermal management. Zinc alloys have excellent thermal conductivity, and has a good heat dissipation.
Complex Geometries: Zinc die casting provides the production of intricate, high-precision parts required for modern vehicles. These required zinc die casting components also easier to be shaped at lower cost, compare to other metal parts. This can meet some induvidual requirements for autmotive EV.
4. Advancements in Zinc Alloy Development
With the development of zinc alloys tailored for specific applications, The trend shapes the future of zinc die casting. As a kind of newly metal material, zinc properties and applications had proven in sufficient that it is advanced and challengable. The follow features of zinc will create a best business opportunity for the demand of the future market.
High-Performance Alloys: Zinc alloys manufacturers are investing in research to create zinc alloys with enhanced mechanical properties.They will have higher tensile strength, improved wear resistance, and better thermal performance. This kind of alloy is suitable for mechanical structructural components.
Corrosion-Resistant Alloys: New formulations are introdued to improve corrosion resistance, especially for components exposed to harsh environments. Like transimission housing and oil filter, which endure acid oil corrosion inside luberation oil pool. Sometimes, zinc alloy casting parts coated so that prolonging its life and durability.
Alloys for Miniaturization: With the rise of compact devices, in electronics and medical device,where needs more micro-sized, high-precision parts to assemble these smart devices. Zinc die casting can create precision assemblies for electronics and medical instruments.
5. Increasing Demand for Precision and Customization
Customization is becoming popular trend of modern process, and comes from diverse client requirements and the need for unique components. Zinc alloy die casting just meets the demand of precision and customization aross various industries. By The Technique Of Supporting Casting Zinc Alloy With Hot chamber Die Casting Machines, providing unique and precision zinc die casting components for many industries. Its advantages listed as the below content.
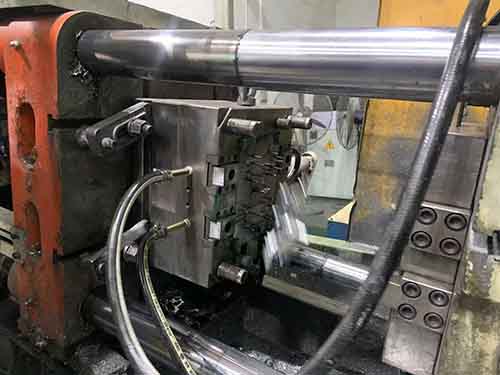
Complex Mold Designs: With advanced Design Software, our engineers can have the creation of highly intricate designs. Collaborate closely with client, and fully understand the needs specifications from the client, considering of functions and applications of the casting part, select high quality mold tooling material, design high quality precision casting die.
Customer-Specific Solutions: Professional manufacturers are collaborating closely with clients to follow customized solutions. Our engineering team will provide OEM or ODM services. Conduct the improved technique drawing to produce final products or create unique design drawing accordance to client conception and data informations until finishing the prodcution of final prodructs.
Conclusion
Zinc Alloy Die Casting’s Innovation And Growth, which is driven by advancements in technology, sustainability initiatives, and evolving market demands. For us, following these trends, and keep competitive and facing the challenges of a dynamic global market. By balancing cutting-edge technologies and insist on sustainability goal, consistently creating and improving zinc die casting process, delivering more functional casting parts across diverse industries. As a professional zinc die casting manufacturer with a strong engineering design team, should follow these trends. We will position us as a leader in the industry, and ready to seize new opportunities and use innovative solutions for the future of zinc alloy die casting. Provide our consideration services and high quality prodcuts to our clients and business partners.