Zinc alloy die casting is a crucial process in the automotive industry. It provides durable, intricate, and cost-effective metal components. These meteal components meet more cars and vehicles’ greater fuel efficiency and high performance. This leads to zinc alloy die casting parts become indispensable assemblies in automotive industry market. Rely on their unique blend of strength, formability, and precision in manufacturing complex parts, they can be responsable for some specific mechanical parts and electric components in automotive sectors. For automotive manufacturers, zinc die casting is ideal solution for producing intricate, high-quality components. In this article, we’ll explore applications of zinc alloy die casting in the automotive industry from the following aspects.
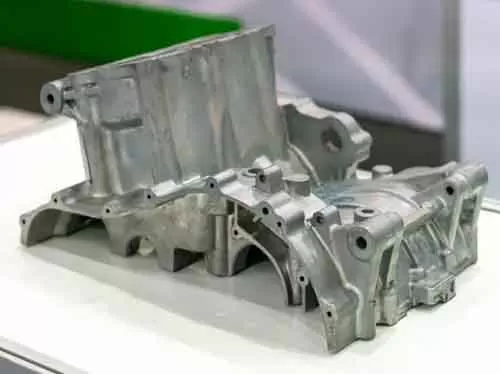
Why Are Zinc Alloys Used in Automotive Manufacturing ?
Statistic shows that zinc alloys have some specific metal properties. So Zinc die casting can be suitable for automotive applications due to zinc metal properties completely. Automotive manufacturer found that zinc alloy automotive components were more costly and durable, compare to some of aluminum one. But also These zinc die castings have a steady structure. The below key points have an enough proof.
High Strength-to-Weight Ratio And Flexiblity
Zinc alloys provide high strength and durability while keeping the weight of the components low. These parts are critical to decrease the weight of overall weight of vehicle, enhancing vehicle fuel efficiency and performance. Meanwhile,zinc alloy die casting component’s structure can also be changed at any time, only spending lower cost. It is flexible and convenient for personalized car and custom smart electric vehicle.
Strong Corrosion Resistance
Some automotive parts are exposed to harsh conditions, including moisture and marine bench. Zinc alloys have excellent corrosion resistance. Especially some zinc alloy die casting components can withstand the salt moisture air on the bench of sea, avoid some fault the vehicle occurred.
Dimensional Precision
Zinc die casting produces precision components with tight tolerances. They have high accuracy dimensions and smooth surface finish. This reduces the need for secondary machining and ensures consistency across mass production. Sometimes, some precise automotive parts should be processed by cnc machine center so that ensuring that these parts can be suitable for vehicle assembly.
Cost-Effectiveness
Zinc die casting is highly economical, especially for high-volume production runs. It can process complex shapes in mass production, reduces assembly costs and improves overall manufacturing efficiency. But also the low melting points zinc metal can have a fast cycle time to achieve a high volume production in shorter time.
Common Automotive Components Zinc Alloy Die Casting
Some of the most common automotive components made using zinc die casting due to zinc die casting parts are durable and cost-efficiency. Zinc alloys are easy to be cast and have strong mechanical structure properties, and can be satisfied with the needs of automotive components functions,repeative impacts and viberation. Some of other components also provide attractive appeal appearance and corrosion resistance. The details as the folowing items on automotive sectors.
Transmission
Zinc alloys are used to create strong yet durable housings that protect the transmission system while maintaining fuel efficiency. The transmission housings are strongly corrosion resistance and solid , and have a longer life span. In accordance with transmission system space design, Various shaped zinc die casting transminssion housings are created in flexible.
Engine Covers
Zinc die cast engine covers offer protection for engine components. While being able to handle high temperatures, The zinc cover can have a good heat dissipation, maitain the engine have a lower temperature, work normally. The cover also endure the weight things repeative impacts and effective protect the engine core well once any collision accident occurred.
Brackets and Supports
Structural components such as brackets that secure engine parts or electrical systems. These zinc die casting brakets and supports have their strength and durability. The battery brackets for EV are made of zinc alloys, and either provide a good heat dissipation for battery reactors or prevent any damage of impact from other weight things.
Door Handles and Lock Mechanisms
Zinc alloys allow for precision casting of door handles and lock mechanisms, offers both aesthetic appeal and functionality. Its design is flexible. The ignition starter from turning key to button down, The design modification increase the comfortability and experience of drivers and end-users, zinc die casting design also create more attractive ignition starter setting and lock mechanisms.
Fuel System Components
These Parts like fuel line fittings, fuel injectors, and pump housings. They require corrosion resistance and precise engineering. The common gas and fuel all produces acid and other corrosion during long term usage. The zinc die casting components can resist fuel corrosion due to zinc strong corrosion resistance and rust resistance.
Electrical Components
Zinc has good electrical conductivity, is often used in connectors, terminals, and other parts within the vehicle’s electrical systems. Zinc’s heat-resistant properties allow it to be used for heat dissipation, avoid sensitive electronic components of the vehicle against high temperatures.
Zinc Alloy Die Casting in Electric Vehicles (EVs)
The rise of electric vehicles (EVs) is having a profound impact on the automotive zinc alloy die casting market. The zinc die casting components are same time used for improving EVS perfermance and realize some specific functions in The EV.
Lightweighting for Range Improvement: EVs need to maximize energy efficiency to light the oeverall weight of vehicle, More zinc alloy components, which replace some more heavier iron weighter. This helps reduce the overall mass of the vehicle. It also contribute to zinc unique metal properties, which have a strong mechanical strength and rust resistance.
Electrical Components: Zinc’s conductive properties make it an ideal material for components within EV electrical systems. This includes connectors and terminals that require reliable performance in high-voltage environments. These components have a good electricity conductivity, and connect to the electric circuit closely, and offer a good heat dissipation, and as electric moudle housing , protect the moudle and disperse the heat from electric components.
Thermal Management: Zinc die cast components may be as heat shields and battery housings, managing the heat generated by EV powertrains and batteries, which maintain safety and performance. The heat that gearings system produce can be dispersed quickly with zinc transmission housing when the car ran, and ensure the transmission system performance and safety.
Conclusion
Applications of zinc alloy die casting the automotive industry has become an indispensable. Since it offers numerious advantages such as precision, strength, and cost-effectiveness. With trends like lightweighting, electric vehicle production, and sustainability shaping the future of automotive manufacturing, zinc die casting will play an even larger role. Manufacturers who embrace the latest advancements in die casting technology, automation. Sustainable practices will be well-positioned to meet Automotive Zinc Die Casting Market From 2024 to 2025 and beyond.