Zinc alloy die casting and stainless steel casting have distinct characteristics, making each suited for specific applications. For their different material properties, these die casting parts are used in different place on same machine and equipment. This makes them to work at best status. Zinc alloy die casting vs. stainless steel casting, Where does their advantages reflect respectively ? Let us explaining to everyone about it by using the following information.
Zinc Alloy Die Casting VS. Stainless Steel Die Casting
As the follow information, which introduce zinc alloy and stainless steel die casting unique advantage and benefits respectively. According to their different characters and application value, zinc alloy and stainless steel die casting processes all need complete technique to produce die casting products.
Advantages of Zinc Alloy Die Casting
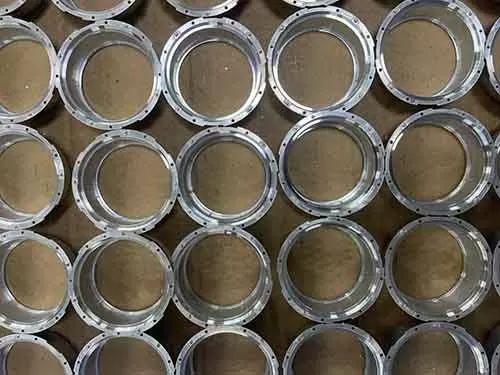
Cost-Effectiveness
Zinc alloys are generally less expensive than stainless steel. Zinc Die casting offers rapid production cycles, and employing mass production with high repeatability and minimal waste due to zinc material special properties. A professional zinc casting manufacturer uses zinc die casting in high efficiency to raise company profits. Zinc die casting tools have a longer lifespan due to lower operating temperatures, reducing overall production costs.
Design Flexibility
Zinc alloy die casting can achieve intricate and thin-walled designs with high precision. A proficient product design team will can design and make complex geometies according to client’s requirements. It allows for smoother surface finishes, reducing or eliminating post-processing like polishing or machining. Excellent for creating miniature components with tight tolerance and accuracy dimensions.
Mechanical Properties
Zinc alloys are more impact-resistant than stainless steel. Zinc alloys are lighter than stainless steel, reducing the overall weight of the product. Also zinc alloy has a strong strength and corrosion resistance. Many automotive components are made of zinc alloys, and improve fuel-effective and electronic vihecles overall weight and increasement of running performance.
Corrosion Resistance
Zinc alloys offer natural corrosion resistance,and less rust produced, So zinc die casting components can be exposed on moisture air and corrosion environments for a long time. especially when plated or coated, though less than stainless steel in extreme environments.
Recyclability
Zinc alloys are highly recyclable, and sustainable and support environment protection and confirm international green eco-friendly standards. The special metal alloy can be reused with less waste, eliminate carbon emmition to enviroment, and the zinc die castings lost its functionality, and they will be remolten and cast other die castings to use.
Advantages of Stainless Steel Casting
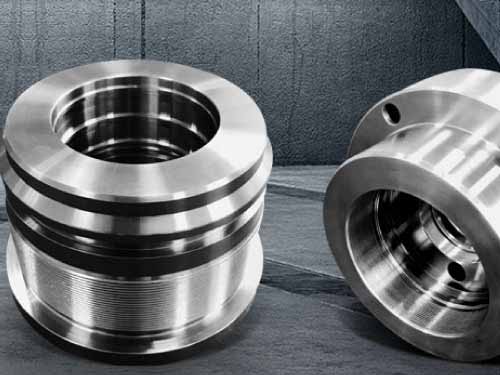
Durability
Stainless steel is extremely strong and resistant to wear and tear, and often used for heavy-duty applications. It has strong hardness, and remain shiny and appeal appearance with a bit rust on the surface for a long time. The stainless steel die casting components are mainly used for transmission system that handle high pressure and great torque transmission.
Corrosion Resistance
Superior resistance to rust and corrosion, even in harsh environments (e.g., marine or chemical exposure), without the need for additional coatings. These stainless steel components always maintain bright shining appearance, and with strong corrosion resistance. They are exposed to corossion environment and moisture air for a long time.
Heat Resistance
Stainless steel can withstand higher temperatures than zinc alloys, making it suitable for high-heat applications. These gearings can over high temperature during mechenical movements, the stainless steel have a good thermal conductivity, and cool the gearing setting and ensure the transmition setting running smoothly.
Aesthetic Appeal
Stainless steel’s natural finish is visually appealing, often used in applications requiring premium looks without additional treatments.
Biocompatibility
Stainless steel is non-toxic and hypoallergenic, it is favor for medical and food-related applications. Such as stainless steel tableware, kitchen utensils and gifts in our daily life.
Automotive Application for Zinc Alloy and Stainless Steel Die Casting Respectively
Zinc Alloy Die Casting in Automotive Applications
- Offering Lightweight Components: Zinc alloys are much lighter than stainless steel, reducing the overall weight of the vehicle, which improves fuel efficiency and reduces emissions. These zinc die casting components are suitable for fuel-efficiency cars and EV in automotive industry.
- Complex Design Capabilities: Zinc die casting allows for the production of intricate, thin-walled, and detailed components with high precision, suitable for modern vehicle designs.
- Cost-Effective Production: High-speed production with minimal machining or finishing required. Excellent for mass production of parts like door handles, brackets, console components, and decorative trims.
- Corrosion Resistance: Zinc alloy natural corrosion resistance, often enhanced with coatings like electroplating, and being suitable for interior and exterior applications.
- Impact Resistance: Zinc alloys afford shocks effectively, which is beneficial for structural automotive components under moderate stress.
- Sustainability: Zinc alloys are high recyclable, supporting the automotive industry’s push toward sustainability environmental protection standard.
Stainless Steel Casting in Automotive Applications
- Exceptional Strength and Durability: Stainless steel components are highly resistant to wear,tear, and is ideal for parts exposed to heavy loads or friction.
- Superior Corrosion Resistance: Stainless steel can withstand extreme environments, such as exposure to road salt, humidity, and heat, without additional coatings.
- High-Temperature Resistance: Excellent for components endure high operating temperatures, such as exhaust systems or engine parts.
- Aesthetic Appeal: Stainless steel’s natural finish and resistance to decolor. They are regarded as ideal part for high-end trims or decorative elements.
- Minimal Maintenance: Parts made of stainless steel require little maintenance, lasting longer in extreme conditions.
Comparison Summary for Automotive Parts
Feature | Zinc Alloy Die Casting | Stainless Steel Casting |
Weight | Lightweight, reduces vehicle weight | Heavy, adding durability but increasing weight |
Production Cost | Lower due to high-speed die casting | Higher due to slower production and material cost |
Corrosion Resistance | Moderate, enhanced with coatings | Excellent, natural resistance without coatings |
Design Complexity | High, supports intricate and thin-walled parts | Limited complexity, suitable for robust designs |
Durability | Good, sufficient for moderate-stress parts | Exceptional, ideal for high-stress applications |
Applications | Interior, decorative, and lightweight parts | Structural, high-temperature, and load-bearing parts |
Conclusion
By Zinc Alloy Die Casting VS. Stainless Steel Casting, there are different advantages and benefits in application and functionality respectively. For different metal properties between zinc alloy and stainless steel material, they have each unique die casting process methods respectively. Zinc die casting is focus on the advantages that high precision, high production efficiency, low cost and strong corrosion resistance. But Stainless steel die casting is adhere on supper hard, Superior corrosion resistance, heat-resistant and beautiful Aesthetic Appeal. Whenever zin die casting and stainless steel die casting components, they can be all used in automotive field, Only difference, these parts are used in different place at same vehicle and equipment.