Zinc and aluminum alloy die casting has unique advantages respectively. In communication industry, the best choice between both depends on the specific requirements of your project, including factors like strength, cost, weight, and finish. These factors are all decided by the application specific for communication device and equipment. Here’s a breakdown of the pros and cons of each material to help determine which might be better for your application. This is Zinc Die Casting vs. Aluminum Die Casting.
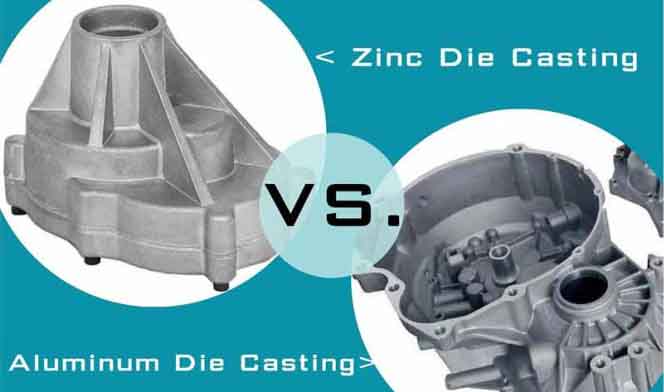
Zinc Alloy vs. Aluminum Alloy Die Casting
Material Cost
Production Process
Application Fields
Durability
Depends on Specific Requirements from Communication Industry, We recommand the best solution to our client. Zinc alloy and Aluminum alloy die casting are Our main processes.
Zinc Alloy Die Casting
Zinc alloy die casting is The Most Common Casting Process for Zinc Alloys. The process occupies most casting industry market share. With zinc alloy unique properties, zinc die casting components have been used for many industries applications. Through hot chamber die casting process, many manufacturers are beneficial from fast cast cycle in mass production.
Strength and Ductility
With excellent strength and ductility, zinc alloy is suitable for smaller, more intricate parts. Molten Zinc alloy have a good ductility, fits thin wall and small size die casting parts. And can withstand high impact,allows high-volume production in fast cycle.
Strong Corrosion Resistance
Excellent corrosion resistance, often withstand in environments exposed to moisture. Suitable for parts that will be exposed to harsh weather or corrosive environments. Monitoring camera housing, signal antenna and smart device enclosure can be made from zinc alloy, and ensure 5G internet connection in some harsh environment and bad weather.
Good Weight-Ratio
Zinc is Heavier than aluminum dut to its high density. But it is durable and weight- ratio, compare to iron casting parts. suitable for protective housings and connectors in signal tower and data center in commnunication industry.
Lower Cost and Longer Tooling Life
Zinc alloy’s lower melting point allows for faster casting cycles and longer die life. During the production process, It reduces die casting process cost, So overall cost of part is lower than aluminum die casting part, Although the cost of aluminum alloy material is very low.
Fine Surface Finish
The molten zinc alloy has a good fluidity, added the precision steel casting die, under high pressure, it can provide a smoother surface finish that often requires minimal post-processing. Especially some miniature metal die casting components with precision dimensions and complex design shapes.
Hot Chamber Die Casting
Integrated with melton metal pool, overflow impurities inside molten zinc, keep steady temperature purified molten zinc alloy and preheated casting die. Through specific gooseneck mechanism, Inject molten zinc into the preheated casting die, cooling and soliditying quickly, having a fast casting cycle and high volume production.
Aluminum Alloy Die Casting
Aluminum allopy die casting belongs to cold chamber die casting process, which can create high precision metal cast parts with lightweight. But the process is conducted under high temperature and pressure, Aluminum melton pool is seperated from the cold chamber die casting machine and prevent damage the machine from high temperature. To ladle the molten aluminum from the melton pool, and inject into the steel casting die and pass a longer cooling time and solidify, eject the part out from the die.
Strength and Durability
Aluminum alloy offers a good strength-to-weight ratio, it is lightweight due to lower density of aluminum. The aluminum alloy die casting also a strong integrated mechnical properties. They are preferable for miniature smart wearable device enclosure in communication industry.
Corrosion Resistance
Aluminum also has good corrosion resistance, however it may not perform as well as zinc in salt water or marine environments. For a long time anodized layer on the surface of parts. The anodized layer can withstand corrosion substance and exposed in acid air.
High Light Weight
Much lighter, solid and good toughness. Used for some vital components in communication equipment applications.
High Material Cost and Tool Maintenance Cost
Though aluminum raw material cost is lower , but the higher melting point can lead to high heat energy consumption and faster tool wear. This means more frequent maintenance or die replacement is needed. makes the production process cost higher, Overall part cost is higher. The lower cooling system cause a slower casting cycle and the risk of shrankage.
Cold Chamber Die Casting
Apart from melton metal pool, avoid the higher temperature damage the cold chamber die casting machine. Slower part shape, cooling and soliditying, due to higher melt pointings aluminum alloy. More heat energy consumption to melt aluminum alloy, and storage the preheated melton metal reservior, and ladle the molten aluminum alloy and inject into the casting die , shape die casting part and eject it out from the die.
Zinc Die Casting and Aluminum Die Casting’s Applications On Communication Field
On the communication filed, metal die casting plays a crucial role in manufacturing components for devices and equipment. Especially with growing demands for precision and durability, high-performance telecommunications equipment. About how zinc and aluminum die casting can be leveraged for different applications in this field.
Zinc Die Casting | Aluminum Die Casting | |
---|---|---|
Housing and Enclosures | Smaller, intricate components like connectors, plugs, and jacks, with fine detailing and complex shapes. Used in housing for sensitive electronics due to its EMI/RFI shielding properties. | Like larger housings, such as enclosures for antennas, base stations, and even outdoor routers or network switches. They are lightweight and corrosion-resistant properties. |
Heat Management | good thermal conductivity, it’s generally not preferred in applications where significant heat dissipation is needed, mainly due to its heavier weight and higher density. Compare to light weight aluminum. | With excellent thermal conductivity, and used in parts requiring heat dissipation. For example, aluminum heat sinks in signal processors, transmission amplifiers, and other communication devices. |
Structural Components for Communication Towers | Smaller zinc die-cast parts are used in connectors, clamps, and brackets in communication towers. They have strength and durability. | Their lightweight and weather-resistant nature makes them fit outdoor environments. Aluminum components reduce the overall weight of the tower structure, make in regions prone to seismic activity. |
Antennas and Satellite Communication Equipment | like brackets and connection points, zinc is durability, In complex designs needed to ensure signal accuracy and avoid interference. | Antenna reflectors and supporting components are made from aluminum due to its lightweight, corrosion-resistant, and reflective properties. |
Connectors | Connectors and other internal components with intricate detailing and provide shielding against electromagnetic interference. In devices like smartphones, tablets, and modems. | Enclosures for routers, modems, and other consumer network devices choose aluminum die-cast parts due to their strength, lightweight, and heat-dissipation properties. |
Conclusion
In summary, Zinc and aluminum alloy die casting have been used for many fields, They have its own advantages respectively, When there is some special demands for metal die casting parts on your project, you can select what you want to in accordance with your real requirements. Of course , Aluminum is very light, and outstanding cooling properties, so it is often used for lightweight purpose. But zinc is heavier, but it is durable and solid, Some zinc die casting parts are used for housings and enclosures for smart devices.
Zinc Die Casting vs. Aluminum Die Casting in the communication industry, zinc die casting is favor of small, complex parts where interference shielding and durability is crucial, Aluminum die casting allows larger structures and components that require heat dissipation, They are light weight. Depending on the component requirements, whenever zinc or aluminum die castings, and contributed to communication industry with their own properties.