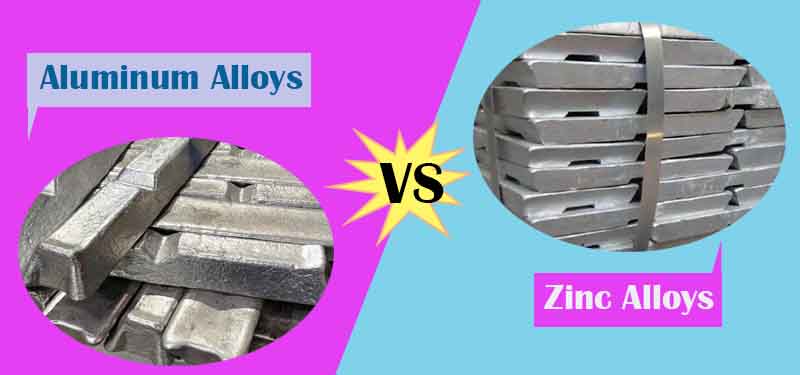
Aluminum Alloys Vs. Zinc Alloys
There are two types of common metal alloy cast material in modern industrial manufacturing, they are aluminum alloys and zinc alloys. Since different metal properties, these material cost and production cost are different. Aluminum alloys cost is cheaper, but production cost is higher, require higher temperature to process, consumpt more heat energy. However, zinc alloys cost are higher, but production cost is very lower, require low temperature to form, and have a fast cast cycle. So these two types alloys are made into some specific functional and structural casting part in different sectors. Aluminum Alloys Vs. Zinc Alloys, Choose the right alloy material to produce proper components in actual applications.
Aluminum Alloys Pros And Cons And Applications
Advantages Of Aluminum Alloys
- Lightweight: They all have far low density(~2.7g/cm³), and ideal for aerospace, automotive and portable smart device and smart wearable device.
- Excellent Corrosion Resistance: Naturally forms a protective oxidation layer, which cover the surface of aluminum part and prevent aluminum oxidation. And have an excellent corrosion Resistance.
- High Machinability: These Aluminum alloys are soft, and easy to be machined, with a good integrated structure.
- High Thermal & Electrical Conductivity: Aluminum naturally has excellent thermal conductivity, many electronic components need aluminum housing and enclosures to transfer overheat into the air quickly and maintain lower temperature. Such as high power LED lighting, electronic product mainboard frame.
- Castability And Fluidity: Aluminum alloys blong to metal that easy to cast. When the metal is molten, and have a good fluidity and ductility, and can fill the die fully under high pressure, and form high quality casting part.
- Sustainability And Recyclability: Aluminum is 100% recyclable, like zinc, and as sustainable material, which is applied repeatively with no quality loss. And it is ideal material to eco-friendly.
Disadvantages Of Aluminum Alloys
- Lower Hardness & Poor Wear Resistance: Aluminum is softer than steel or zinc, leading to wear in high-friction applications.
- Higher Production Cost Than Zinc Alloys: Aluminum alloy require higher temperature to melt, and longer time for cooling, and higher defective rates, result in higher production cost.
- Lower Production Rates: Higher thermal expansion can cause high shrankage and cold shut. result in lower production rates.
- Porosity in Castings, facing surface finishing challenges: Hydrogen absorption can cause voids, requiring vacuum casting or degassing. Or another Aluminum Casting Impregnation Reduce Shrink Porosity And Gas Porosity.
Applications Of Aluminum Alloys
Aluminum alloy is very light metal, and castable, and also easy to be machined. So it can be cast into some precision components across many industries. Depends on the specific functional and application environments, die casting manufacturer can choose the right aluminum alloy composition to produce more high precision parts. and use them in many industries.
Industries | Aluminum Alloys Applications |
---|---|
Aerospace & Aviation | Aircraft structures : fuselage, wings, panels, they are very light, reduce overweight of aircraft or plane. Spacecraft & Satellites: fuel tanks, structural components are made of aluminum alloys. Either light or high toughness. Helicopter rotors & engine parts: High hardness, and good resistant to sress. Common alloys: 2024, 6061, 7075. |
Automotive Industry | Engine components: such as pistons, cylinder heads, strong corrosion resistance and high hardness. Body panels & chassis : weight reduction for fuel efficiency. Wheels & Suspension Parts: Light weight, and solid and fine integrated structure. Common alloys: 5052, 6061, 6082. |
Marine Applications | Ship hulls & Superstructures: good corrosion-resistant in seawater Offshore Platforms & Boat Fittings: Easy machined, and remain a high precision dimensions. Common alloys: 5083, 5086, 6061. |
Construction & Architecture | Window frames, Roofing, and Cladding: Lightweight, wear-resistance and strong corrosion resistance in air. Wall Curtain Decoration: Good metal gloss, corrosion resistance. Proof moisture. Common alloys: 6063, 6061 |
Electrical & Electronics | High voltage Electricity Transferation: Belong to electical conductive substance, replace copper. Heat Sinks: excellent thermal conductivity, quickly conduct heat energy into the air and other metal substance. and keep a lower temperature. Electronic housings & Smartphone Frames: docorative and protecting the core components. Common alloys: 1350, 6061, 1100, |
Packaging Industry | Beverage cans (Al 3004 & 5182): high ductility, and easy to form. Food containers & foil: (Al 8011, 1235). Luxury and storage the food well. Pharmaceutical packaging: Decoration and promption. |
Defense & Military | Armored vehicles & military aircraft: Reduce overweight of equipment, and remain high performance of equipment . Missile casings & naval ships: light weight, and offer a high speed for very light weight. Common alloys: 7075, 5083, which are high strength & ballistic resistance. |
Zinc Alloys Pros And Cons And Applications
Advantages Of Zinc Alloys
- Superior Castability & Fluidity: Zamak alloys have a good fluidity and flow well in mold, filling thin walls(as thin as 0.5mm).
- Precise Dimensions And Tight Tolerance Accuracy: Low shrinkage (~0.7%) compared to aluminum (~1.3%), making zinc ideal for tight-tolerance parts (e.g., gears, connectors).
- High Strength And Stong Wear Risistance: High hardness metal, and higher tensile strength and strong wear resistance, and endure impact times and high frication applications.
- Fine As Cast Surface Finish: With high precision steel tooling die, cast zinc die casting part with fine surface, with less post-prrocess.
- Fast Cast Cycle Production: lower temps (~385°C/725°F vs. ~660°C/1220°F for Al), allowing quicker die-casting cycles and energy savings.
- Cost-Effective for Small, Complex Parts: The lower melting decide zinc alloys to cast small sizes casting parts, but the zinc die castings are high precision.
Disadvantages Of Zinc Alloys
Heavy: 2.5x denser than aluminum, making it unsuitable for weight-sensitive applications.
Limited High-Temperature Performance: Loses strength above ~120°C (250°F), not suitable for engine components or hot environments.
Corrosion Resistance Requires Plating: Bare zinc in humid or salty environments requires equires chromate plating, powder coating, or nickel finishes for protection.
Brittleness in Certain Alloys: Zamak 7 and ZA-12 are more brittle than aluminum, risking fracture under impact.
Not Ideal for Large Parts: Higher density makes large zinc castings unwieldy and expensive (aluminum or magnesium are better for big components).
Applications Of Zinc Alloys
As one of lower melting points Metal, Zinc alloys can be cast into ideal metal components used largly in many industries, At lower production cost, technician can ensure producing high quality die casting components with hot chamber die casting machines in high efficiency. Of course more complex geometries and integrated structure components for zinc die casting meet the specific requirements of many industries.
Industry | Zinc Alloy Applications |
---|---|
Automotive Industry | Transmision And Fuel Line Component: brackets, Fuel filters and gearbox components Interior and Exterior Components: door handles, Antanna, car label and knob. Safety Systems: Airbag housings and seatbelt mechanisms due to high strength and impact resistance. Common Alloys: Zamak 3, Zamak 5, Zamak 7, Zamak 8 |
Electronics & Electrical Appliances | Connectors & Housings: Used for smartphones, laptops, and power adapters due to its good electricity conductivity and shielding electric magnet signal. Battery Casings: Strong corrosion resistance and solid. Common Alloys: Zamak 3, Zamak 5, Zamak 7 |
Construction & Hardware | Door & Window Fittings: Hinges, locks, and handles, strong corrosion resistance and high precision dimensions. Plumbing Fixtures: Faucets, valves, and fittings due to zinc alloys castable and durability. Common Alloys: Zamak 3, Zamak 5 |
Cloth Accessoiries | Zippers & Fasteners: small size and high precision dimensions and a smooth surface finsh. Hang tags: Easy to cast and fine surfce finish. Common Alloys: Zamak 3 , Zamak 5 |
Industrial Applications | Bearings & Bushings: good wear resistance and castable. Corrosion-Resistant Coatings: Common coating metal, provide a good bond for electrolating process. |
Medical & Dental | Dental Amalgams(Zamak 3,Zamak 5 ): as dental filling material Surgical Instruments: biocompatibility and sterilization resistance. |
Aerospace & Defense | Safety System lock fitting: used in certain aircraft parts. Military Hardware: Solid and castable, durable. Common Alloys: ZA-12, ZA-27 |
Aluminum Alloys Material Vs. Zinc Alloy Material
Aluminum Alloys Material | Zinc Alloys Material |
---|---|
2024: Aluminum (~90%), Copper (Cu): 3.8–4.9%, Magnesium (Mg): 2.1-2.9%, Manganese (Mn): 0.3–0.9%,Iron (Fe): ≤ 0.5%,Silicon (Si): ≤ 0.5%,Zinc (Zn): ≤ 0.25%,Titanium (Ti): ≤ 0.15% | Zamak 2: Zn (~95.5%), Al (3.8–4.2%), Cu (2.7–3.3%), Mg (0.03–0.06%) |
7075: Aluminum (~88%), Copper (Cu): 1.2-2.0%, Magnesium (Mg): 0.8-1.2%, Manganese (Mn): ≤ 0.3%,Iron (Fe): ≤ 0.5%,Silicon (Si): ≤ 0.4%,Zinc (Zn): 5.1-6.1%,Chromium (Cr): 0.18–0.28% | Zamak 3: Zn (~95.5%), Al (3.8–4.2%), Cu (<0.1%), Mg (0.02–0.05%) |
6061: Aluminum (~97%), Copper (Cu): 0.15-0.4%, Magnesium (Mg): 1.2–1.8%, Iron (Fe): ≤ 0.7%,Silicon (Si): 0.4-0.8%, Zinc (Zn): 0.25%, Chromium (Cr): 0.04-0.35% | Zamak 5: Zn (~95.5%), Al (3.8–4.2%), Cu (0.7–1.1%), Mg (0.03–0.06%) |
5052: Aluminum (~96%), Copper (Cu): ≤0.1%, Magnesium (Mg): 2.2-2.8%, Iron (Fe): ≤ 0.45%,Silicon (Si): ≤0.25%, Zinc (Zn): 0.1%, Chromium (Cr): 0.15-0.35% | Zamak 7: Zn (~95.5%), Al (3.8–4.2%), Cu (<0.1%), Mg (0.005–0.02%) |
6082: Aluminum (~97%), Copper (Cu): ≤0.1%, Magnesium (Mg): 0.6-1.2%, Iron (Fe): ≤ 0.5%,Silicon (Si): 0.7-1.3%, Zinc (Zn): ≤0.2%, Manganese (Mn): 0.4–1.0% | ZA-8: Zn (~91%), Al (8.2–8.8%), Cu (0.8–1.3%), Mg (0.015–0.03%) |
5086: Aluminum (~94%), Copper (Cu): ≤0.1%, Magnesium (Mg): 3.5-4.5%,Chromium (Cr): 0.05–0.25%, Iron (Fe): ≤ 0.5%,Silicon (Si): ≤0.4%, Manganese (Mn): 0.2-0.7% | ZA-12: Zn (~87%), Al (10.5–11.5%), Cu (0.5–1.2%), Mg (0.015–0.03%) |
1350: Aluminum (~99.5%), Copper (Cu): ≤0.05%, Iron (Fe): ≤ 0.4%,Silicon (Si): ≤0.1%, | ZA-27: Zn (~70%), Al (25–28%), Cu (2.0–2.5%), Mg (0.01–0.02%) |
1100: Aluminum (~99%), Copper (Cu): 0.05-0.2%, Iron (Fe): ≤ 0.95%,Silicon (Si): ≤0.95%, | ACuZinc (Zn-Al-Cu): Zn (~99.5%), Ti (0.1–0.3%) |