In order to prolonging the life span of zinc die casting parts and enhancing its durability, manufacturers take some ideas to improve the quality of zinc die casting parts. Zinc casting parts allow for coating layer and further surface finishes to meet various demands at home and abroad markets. According to these parts’ functionalities and applications, people can choose right surface finish option to treat zinc die castings. How to choose right surface finish options ? This is popular topic, and the answer manufacturer want to get when they try their best to produce high quality metal parts. At below content, we have a detail introduction for the topic.
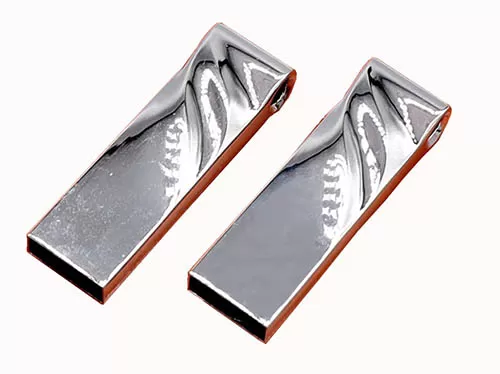
What’s Die Castings Surface Finishes ?
Die casting surface finishes mean that the surface of metal castings need be treated after they are produced. These finishes can applied on based of functional requirements and aesthetic preferences. Common options include the follow methods.
Machined Finish
Some zinc die casting parts may have a secondary process. Using some digital control equipment to optimize their surface finishes. For example, USB hard disk housings , which are small size ones, they should be suitable for some smart devices. So the burrs on these zinc die casting parts should be removed by precision cnc machine centers or digital lathe machines.
Polished Finish
Enhances appearance improve the surface smooth by polishing process. it can improve uneven areas and parting line flashes , making the appearance of these die casting parts smoother. It will be beneficial for high quality electroplating treatment, enhance corrosion resistance of these parts, prolong life span of zinc die casting parts.
Plated Finish
Coatings like nickel or chrome for added protection, aesthetics and corrosion resistance by electrode. After these die casting parts have the right polishing finish, they are delivered to outsourcing factory for a high quality electroplating process. Workers in electroplating factory will wash the dirts on the polished zinc casting parts off. Then put these parts into chemical pool to electroplate nickel or chrome material on the zinc die casting parts. This complete plated finish.
Powder Coated Finish
Powder coated finish is a high efficiency surface finish option, Using thermal spraying powder coating color paint on the zinc die casting parts. Then cooling these parts , and finish powder coated finish process. The option of surface finish is not only have a beutiful appearance, but also enhance corrosion resistance and prolong life span of zinc die casting parts.
Over all, Each finish offers different purposes, depends on its functionality and aesthetics. However , choose which surface finish option, Undergo the excerpt introduction of the above several options of surface finish. This will enhance corrosion resistance of these parts, prolong life span of zinc die casting parts.
Key Factors Of Choosing Right Surface Finish Options For Zinc Die Castings
Choosing the right surface finish for zinc die castings involves several key factors. Here’s a guide to help us make an informed decision. We consider the follow key points, and ensure that we choose right zinc die casting part’s surface finish options when you are need of have a neccesary surface finish for zinc die casting parts.
1. Functional Requirements
When considering of two factors that corrosion resistance and wear resistance, we must do that. If the part will be exposed to harsh environments, finishes like plating (zinc, nickel) or powder coating may be necessary. the part should have an additional protective coating layer.
2. Aesthetic Requirement
In some cases, some zinc die casting parts need a good appearance and beautiful color, we may do this way. Smooth finishes or polished surfaces are ideal for visible parts. Some finishes allow for coloration, which can enhance the product’s overall look.
3. Manufacturing Processes
Planing manufacutring zinc die casting parts, considering of cost and lead time, like this as follow: More complex finishes may increase manufacturing costs. Balance your budget with the desired outcome. Some finishes require longer processing times. Ensure that your timeline allows for this.
4. Finish Types
- Die casting part polishing Process
- Die Casting Parts Cnc Machining
- Die Casting Parts Electroplating
- Metal Casting Parts Coating
5. Environmental Impact
Consider the environmental impact of the chosen finish and whether it achieves sustainability goals. Zinc die casting parts are made of eco-friendly green metal material , and recycle and almost impact our environment.
By Balancing these factors, we select right surface finish that meets both functional and aesthetic needs while staying within budget and timelines. For zinc die casting parts, on which surface is more smoother and even areas, and so easier to be polished so that proceeding next process for its coated, plated. Definitely the above points should be considered.
Conclusion
To reach to the practice requirement for Zinc die casting parts, they can demand various surface finishes. Including as-cast, machined, polished, plated, and powder-coated, each tailored to specific functional and aesthetic needs. Additionally, frozen finishes can enhance detail and hardness in specialized applications. In accordance with the different practical requirement, we should choose the right surface finish option to increasing the functionality and application of zinc die castings.