Die casting is a general industrial manufacturing process in metal process manufacturing industry. Some specific geometries may be cast and maintain integrated structural steady. Depends on the specific requirement of appearances and functionalities of casting die part, die casting manufacturer can have options of various die casting process. Different application, different castable material and process. Today, we have an article to introduce in detail about die casting common overview: Types, materials & Applications.
Common Die Casting Types
- Hot Chamber Die Casting
- Cold Chamber Die Casting
- Vaccum Die Casting
- Gravity Die Casting
Hot Chamber Die Casting
In the die casting, molten furnace is integrated with the machine. Feeding the metal material into pow, and melting metal material and overflow impurities and keep purified and steady temperature molten matail for injection. Though gooseneck mechanism, The hydraulic piston pushes the molten metal into the preheated die. Then under high pressure the molten metal flow fills into the die fully, cooled and solidified, the die is opened, the desired cast part is ejected out of the die. So hot chamber die casting is ideal for low melting point metal, such as zinc, lead and tin alloys.
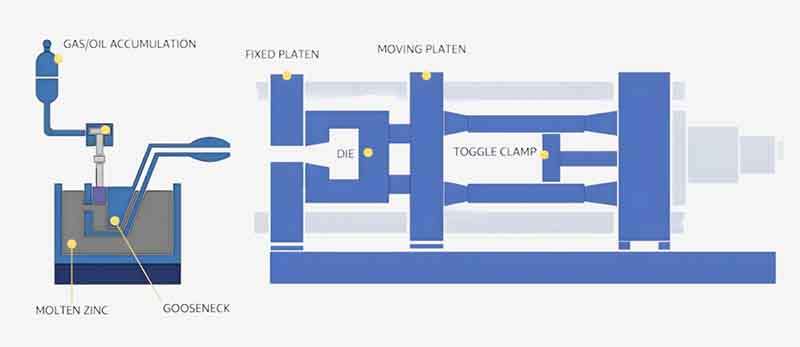
Cold Chamber Die Casting
Cold chamber die casting is a process in which the melton metal furnace is seperated from the machine completely, and require ladling the molten metal and feeding it into the shot and pushing the molten metal into the die with hydraulic piston and fill the die fully under high pressure, cooled and solidified and form as-cast part. These higher melting points metal, such as aluminum, copper, magnesium alloys.
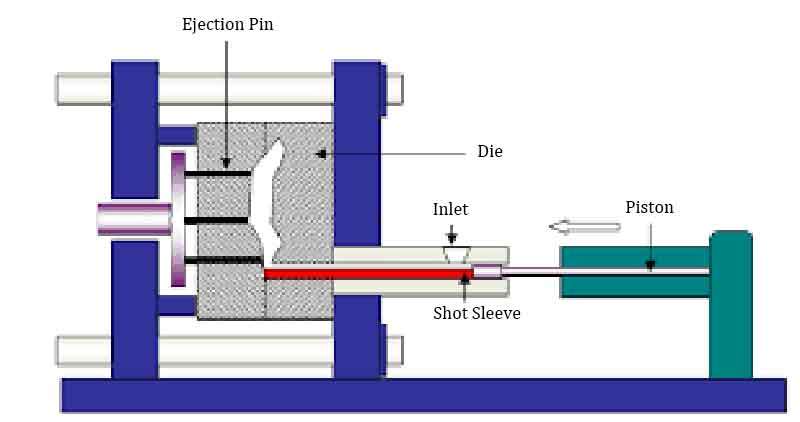
Vaccum Die Casting
To enhance the structure of die casting part, die casting manufacturers should eliminate the porosity on the surface of die casting part. With vaccum die cassting, reducing the porosity stats, and enhancing the internal structure of die casting part. Sometime engineer suggest that adding degas additive into the molten metal, and eliminating the trapped gas within the molten metal and maintain the better molten metal in molten pool. In the term of high pressure of Nitrogen, Form high density die casting part.
Gravity Die Casting
Gravity Die Casting, also known as permanent mold casting, where the molten metal is poured into the die under the force of gravity(with no high pressure). The molten metal flow fill the die naturally, cooled and solidified, the die casting part is formed. Maybe the surface of die casting part is missing, uneven and rough, without an accuracy tolerance and tight dimensions. The kind of die casting is suitable for simple die casting part and better mechanical properties than sand casting.
Suitable Die Casting Metal Choice
Depends on different applications and functionalites, die casting manufacturer should select the right die casting metal alloy and ensure mass production in high effetive and high performance of die casting parts and avoid die casting metal material waste. Commonly we can make high quality die casting part with the right metal alloy due to unique properties of each metal.
Die Casting Materials | Material Examples | Characters | Applications |
---|---|---|---|
Aluminum Alloys | A380, A383 , ADC12 | Very lighweight,strong mechanical properties, good corrosion resistance | Automotive component, aerospace parts, Electronics and consumer goods |
Zinc Alloys | Zamak 3, Zamak5, ZA 8 | Durable and good mechanical properties, flexible design, lower process cost and fine surface finish. | Communication, automotive, electronics, medical device and mechanical components |
Magnesium Alloys | AZ91D,AM60B,AE44 | Extremely lightweight,Good stiffness & damping properties, Excellent machinability | Automotive , aerospace part and electronics |
Copper Alloys | Brass, Bronze | Excellent thermal & electrical conductivity,High corrosion resistance | Electronic connects, marine components and industrial valve and fittings |
Lead & Tin Alloys | Lead and tin | Very low melting point, soft and easy to cast, high density and radiation shielding | Battery terminals, Radiation shielding |
Die Casting Applications
Automotive Industry (Largest Market for Die Casting)
Die casting components have been used largley in automotive industry, involve of interior and exterior components, transmission cases, fuel tube connector, oil filter and sensor enclosures.These components endure strong corrosion and damage from worse weather and marine environment.
Aerospace Industry
Plenty of lightweight components are used on aircraft and plane, such as aluminum and Plenty of lightweight components are used on aircraft and plane, such as aluminum and magnesium alloy die casting parts. Also these strong structural parts have excellent wear resistance.
Electronics Industry
These die casting components are applied for electronic connector and enclosures for shielding electromagnetic interferance, such as consumer device enclsoures, annetants and electronic board heat sink.
Industrial Machinery & Equipment
Large sizes die casting components are suitable for heavy industrial machinery, such as aluminum die casting parts, which are wheels, chassis and engine housings. Small sizes die casting components are also used for heavy industrial equipment due to the excellent corrosion resistance and wear resistance of zinc alloy.
Medical Industry
Medical devices require customized geometries to meet the demand of devices installment. Especially recovery facilities cases and enclosures, these miniature components need tight accurate dimensions and complex design appearance. Zinc die casting is ideal for this industry.
Appliances Industry
Some die casting components are used for kitchen appliances due to their durability and portability. Commonly die casting parts include of aluminum and zinc die casting parts, such as egg shake frame, Dough mixer and some bases for appliances.
Furniture & Decoration Industry
Smart home brings convenience and Intelligence to people life, family wealth security and family member mangagement can be ensured. The above setting dosen’t leave more innovative die casting components, include of door handle of furniture, monitoring camera attractive bases and appeal to eyes ball for decoration.