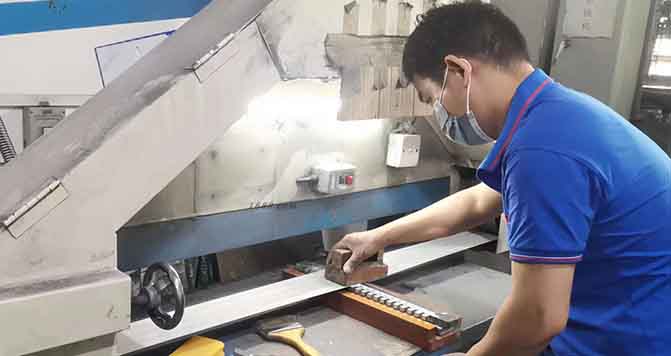
Deburring In Die Casting
Die casting parts deburring process is common post process surface finish in die casting factory. Because the metal parts cast by die, some flashes and sharp edges on parting line of cast parts ang gating to be trimmed. These rough die casting parts should be deburred. Removing flashes and sharp edges with knife and other equipment. More convenient to be polished the surface of them at next step. So in die casting factory, die casting parts deburring process is a vital department. Which is responsible for treating and trimming die casting parts.
- Mechanical Deburring
- Vibratory Deburring
- Manual Deburring
- Cryogenic Deburring
- Laser Deburring
- CNC Machining Deburring
What Is Deburring In Die Casting?
The deburring process in casting is a finishing operation that removes execess material. Such as deburring sharp edges, excess material, or rough spots (called burrs) from a casting part before these die casting parts surface finishes. These burrs are typically formed on the parting lines or at the mold gates during the casting process. These burrs should be removed though some reasonable approches. The blew listed common deburring approches in die casting factory.
Mechanical Deburring
Uses rotating abrasive wheels or belts to grind off burrs. It is suitable for larger, more visible burrs. Using power tools, files to remove burrs and smooth out edges by hand . With abrasive paper or machines, which sand down excess material on the part. Sticking the sandpaper on the rotate wheel, grindering some visible burrs on the part when the wheel rotate.
Vibratory Deburring
The parts are put into a vibratory bowl with abrasive media, the vibrations make the media to rub off the burrs on the part, effectively smoothing them. This process fits small or delicate parts. The action repeat consistently, parts in a rotating chamber that generates centrifugal force, which pushes the vibratory bowl grinder off the burrs.
Manual Deburring
Workers use chisels, scrapers, knives, or brushes to remove burrs and flash on cast parts. This process is best for custom or small batch parts that reach precision and custom requirements. Using hand tools or micro-grinders to remove the burrs on the parts with more intricate and delicate parts. It is flexible and suitable for small volume of parts process.
Cryogenic Deburring
In this process, parts are cooled to very low temperatures with liquid nitrogen, making burrs and flash brittle. The brittle burrs are blasted with small, abrasive media. It is suitable for small parts with many hidden burrs.
Laser Deburring
Using focused laser beams to remove burrs without mechanical contact. It can process parts that require a high level of precision and cleanliness. Like in aerospace or medical applications. Ensure that precision tolerance is high.
CNC Machining Deburring
In order to ensure high precision and tight tolerance dimensions of metal part, cnc machining deburring is used to trim and cut the excess material on the die castings. With high precise cnc machining equipment, ensure the metal part excellent performance and mass production in high efficiency in large volume.
From the above deburring approches, Different parts should be treated by different process. Especially metal die casting parts, the tough pars , on which various burrs are existed, we should adopt the right deburring method to treat them.
Professional Die Casting Factory Provide Deburring Services
While it is labor-intensive and may not be as fast as automated methods, manual deburring remains a vital method in industries requiring precision. Like aerospace, medical devices, and high-performance automotive parts. Especially as the professional die casting factory. TangSheng Hardware Technology is a industrial factory, have to have the following deburring process for zinc alloy die casting parts.
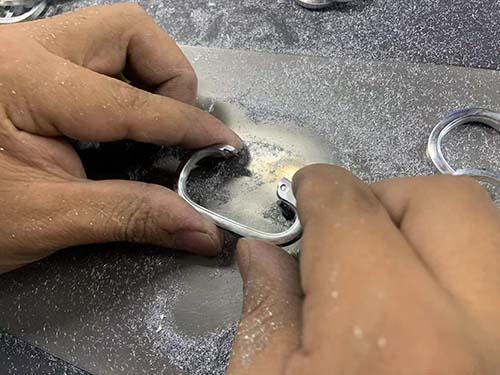
Removing The Burrs By Machining
To removing the flashes and sharp edges on the casting parts, we adopt some small size milling machines to get rid of burrs on the parts easily. It makes the edges of casting parts become so smooth. This operation can complete removing the burrs on edges of die casting parts. But it should be executed comply with secure guideline orders avoid some accidents of injured hand occurred .
Removing The Redundant By hand
To removing the redundant on the casting parts with file , worker use the file to get rid of burrs on the parts easily, make the edges of casting parts become so smooth. This kind manual deburring method is simple and efficiency, but it will spend more labor cost. This operation can complete removing the redundant part from die casting parts. but it request worker to spend more time to improve and remove the redundant part from the die casting part.
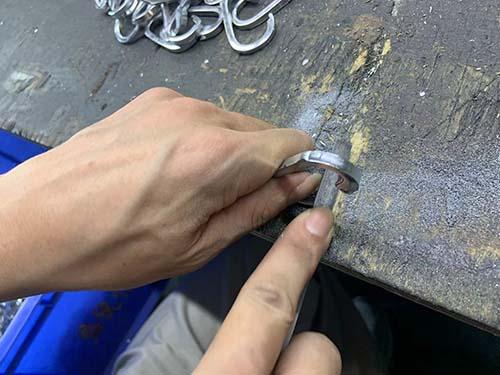
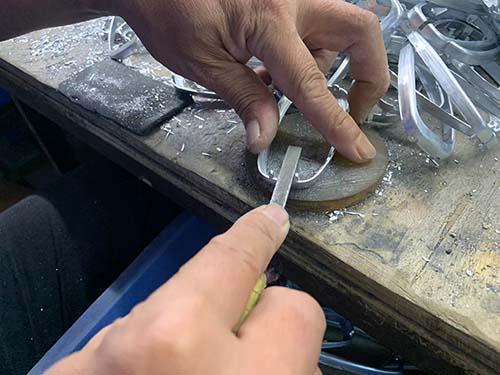
Removing the burr and sharp edges With Files
To removing the burr and sharp edges on the casting part edge with file , worker use the file to get rid of burrs on the parts easily, make the edges of casting parts become so smooth. This kind manual deburring method is simple and efficiency, but it will spend more labor cost. This operation can completely remove the redundant part from die casting parts. but it request worker to spend more time to improve and remove the burr and sharp edges on the die casting parts.
Removing Sharp Edges On The Mouth
To remove sharp edges on the casting part mouth, worker use sanding wheel to get rid of burrs on the parts easily. And ensuring the mouth of casting parts so smooth. This kind manual deburring method can remove the burrs on the mouth. But complying with secure guideline orders avoid some accidents of injured hand occurred .
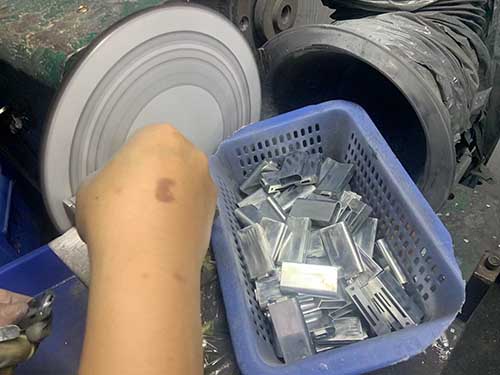
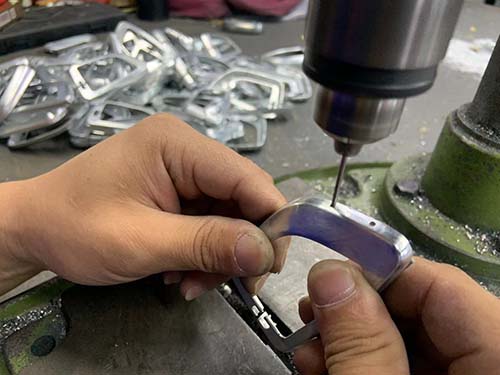
Removing The Redundant In Holes
To removing the redundant part inside the casting part holes with drilling machine , worker operate the drilling machine to get rid of the redundant part inside the holes easily, make the holes of parts is suitable of tapping in the next step. This kind manual deburring method is customized in accordance with die casting status. but it should be executed comply with secure guideline orders avoid some accidents of injured hand occurred .