From casting industry is born, people alway explore casting part to meet the demand of their daily life. The oldest casting method is sand casting, which forming the metal casting part with simple sand molding tool, without tight tolerance and accurate dimension and uneven and tough surface. The casting technology is suitable for heavy weight bases with tough surface at low volume,such as iron casting parts, copper casting parts and some of tough aluminum casting parts. With the continuous improvement of die casting technology, Metal dies are created by innovative man, with them, people can produce tight tolerance and accurate dimensional die casting parts. But also some intended die casting parts with complex geometries and aesthetic appearance are used for many fields. Like Aluminum casting dies and steel casting dies. Die casting vs. sand casting: difference and comparison, The following let everyone know the detailed about it.
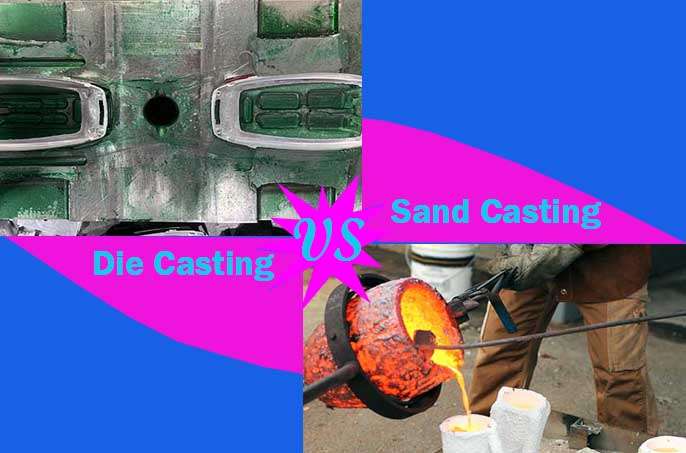
Die Casting VS Sand Casting
- Fast Casting vs Slower Casting
- Tight Tolerance vs Loose Tolerance
- Complex Mold Design vs Simple Sanding mold
- Smooth Surface Finish vs Tough Surface Finish
- Minimizing machining vs high volume cutting and turning
Die Casting Overview and Comparison To Sand Casting
What is Die Casting ?
Die casting is a metal casting process, which means forcing molten metal into a mold cavity under high pressure, passing cooling the die and solidifying the molten metal, forming the intended shape casting part. The mold cavity is created using two halves of hardened tooling steel dies which have been machined into shape. Then assemble the die on the right die casting machine, and align with the die. With the large hydraulic piston, push the melton metal into the high speed steel die and form the casting part. Most die castings are made from non-ferrous metals, such as  zinc, copper, aluminium, magnesium, lead, pewter, and tin-based alloys. Depends on the different metal casting, the hot and cold chamber die casting machine is used. When die casting is applied, manufacturer will produce the die casting part with high precision and fine surface finish, comparing with sand casting, which is a traditional and old type of casting process, offers tough surface and low precise casting parts.
Die Casting vs. Sand Casting : Differences Between Two Types
Aspects | Die Casting | Sand Casting |
---|---|---|
Mold Material | Aluminum &Steel dies (permanent) | Sand molds (expendable) |
Production Speed | Very fast (high-pressure injection) | Slower (natural flow injection, without any pressure) |
Surface Finish | Smooth, precise (minimal post-machining) | Rough, may need post-processes. |
Tolerances | Tight (±0.1 mm or better) | Looser (±1 mm or more) |
Part Size | Small to medium (up to ~50 kg) | Very large (, heavy industrial machinery chassis and main frames, several tons possible) |
Cost | High initial tooling, low per-unit cost and high automation production line. | Low tooling, higher per-unit labor cost, porosity on surface of casting part. |
Metal Options | Limited (non-ferrous alloys preferred) | Almost any metal (including ferrous) |
Mold Design | Complex and longer life tooling | Simple and lower life tooling |
The Different Applications For Die Casting And Sand Casting
Die Casting Applications
These different size die casting parts have been used across many industries. Miniature die casting parts require high precision and complex structural design, engineer suggest that precise casting dies are made and ensure providing high quality die casting components in high effective.