Different composition zinc alloys, different applications. In many fields, zinc alloy die casting parts are used widely due to zinc metal properties and resistance corrosion, easy castablity and low cost. These zinc materials are all have a common characteristic, which is low melt point and easier to be formed. So they can accept custom design and die casting, mold wear is low efficiency. and it allow have a high volume production. Different composition zinc alloys, can be cast into the appropriate component, depends on its functionalities and specific applications in fact.
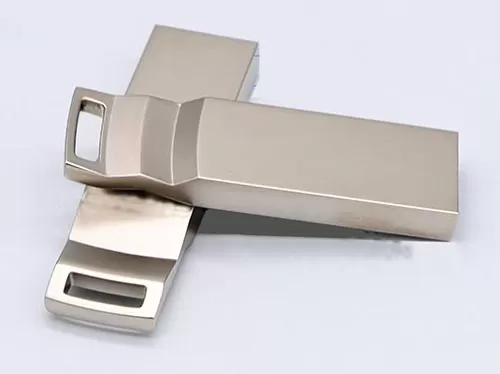
Which Types Are For Zinc Alloy Composition ?
Zinc alloys are diversities of synthetic materials, which are most of zin element, combined with various alloying elements. Dedends on the different demands in fact, they need compose of various metal elements to enhance their own mechanical properties, corrosion resistance, and casting performance. This makes custom zinc die casting parts become very popular, and mainly includes of the below several issues.
Zinc (Zn)
Zin element content , is amount for >90% of the alloy. with excellent corrosion resistance, castability, and a low melting point (~419.5°C).
- ZAMAK 2: Zinc (~96%), Aluminum (~4%), Copper (~3%), Magnesium (~0.05%), Which is highest strength and hardness among ZAMAK alloys.
- ZAMAK 3 : Zinc (~96%), Aluminum (~4%), Magnesium (~0.05%), Copper (minimal),with excellent dimensional stability and castability. Most commonly used alloy, used for Consumer goods, automotive components, and electronics.
- ZAMAK 5: Zinc (~95.5%), Aluminum (~4%), Copper (~1%), Magnesium (~0.05%). With higher strength and wear resistance than ZAMAK 3. It is suitable for parts with mechanical stress, such as gears and brackets.
- ZAMAK 7: Zinc (~99.99%), Aluminum (~3.9%), Magnesium (~0.02%), having Improved ductility and impact resistance. Thin-walled components with intricate designs fit it.
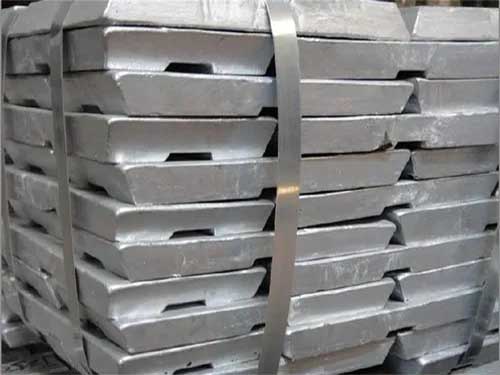
Zinc-Aluminum Alloy
Commonly content ranges from 4% to 27%. Enhances strength and hardness,with corrosion resistance. A good fluidity during casting, allowing for thin-walled and complex shapes.
Items | Chracters |
---|---|
ZA-8 | Zinc (~91%), Aluminum (~8%), Copper (~1%). Suitable for both hot and cold chamber die casting. Can process thin-walled and precision components. |
ZA-12 | Zinc (~88%), Aluminum (~12%), Copper (~0.5%). Offers higher strength than ZAMAK alloys. For Bearings, bushings, and heavy-duty industrial parts. |
ZA-27 | Zinc (~73%), Aluminum (~27%), Copper (~2%). It is highest strength among zinc alloys but limited to gravity casting due to high aluminum content. Structural components, wear-resistant parts use it. |
Zinc-Iron Alloy
Typically control below 0.02%. Considered an impurity; excessive iron can cause brittleness and poor corrosion resistance. Controlled to prevent defects during casting.
Zinc-Lead (Pb), Cadmium (Cd), and Tin (Sn) Alloy
Impurities content is below 0.005% strictly controlled in modern zinc alloys for health, safety, and environmental reasons. It may cause toxic and pollute the environment if excess.
Additional Elements in Specialized Zinc Alloys
Some zinc alloys may include other typical elements to tailor their properties for specific applications. For example, Nickel (Ni) : Improves corrosion resistance and surface finish. Widely used in high-quality decorative or functional coatings. Titanium (Ti): Occasionally added for grain refinement and increased toughness.
Different Zinc Composition, Different Applications
Different composition zinc alloys ,different applications. Depends on different applications for deversity industries, choosing the right zinc alloy material to cast proper functionality zinc casting parts. Here’s a detailed breakdown of commonly used zinc alloys and the industries they serve.
Zamak Applications
ZAMAK 2: Its properties are high strength and hardness, wear resisitance and having a good dimensional stability. It is commonly used for gears , bushings and structural components in Automotive and mechanical industries.
ZAMAK 3: These parts all have excellent castability, dimensional stability and surface finishes. They are often applied for handles ,knobs and zippers in holdhome and electronic consumer goods industry, some emblems , interior trims and decorative components in automotive industry.
ZAMAK 5: It is higher strength and hardness than ZAMAK 3, and has a good impact resistance. And used for door handles brackets and mounting plates in automotive industry and hinges, slides and decorative fittings in furniture industry.
ZAMAK 7: Having an Imroved ductility and impact resistance compare to ZAMAK 3 , Applied for some intricate designs components for electronic and telecommunications, Also can be cast into model figures and small sized components in toys and gaming field.
Zinc-Aluminum Alloy Applications
ZAMAK 8: The alloy material is high strength, good wear resistance and excellent surface finishing. Thin-walled components , housings and gearboxes in automobiles and cars and antenna mounts, structural frames in telecommunications and bearings and bushings in industrial equipment.
ZAMAK 12: It has a balanced strength, wear resistance and good machinability. and used for Reinforcement brackets and supports in construction and some structural components in aerospace industries.
Zamak 27: Its properties are extremely high strength and wear resistance, bushings , bearing and load-bearing components in industrial equipment are cast with zamak 27 material.
Special Zinc Alloy Applications
Zin-Fe Alloy: The material has a good corrosion resistance and electrochemical performance, and common used for coatings and other industrial applications. such as galvanized steel, electroplating material and batteries.
Zinc-Lead (Pb), Cadmium (Cd), and Tin (Sn) Alloy: The material has a wide range of usage, most of them are used for produce batteries and militery defence. Such as battery electrodes and nuclear shielding for radiaction.
Nickel and Titanium Zinc Alloy: Nickel zinc alloy has high electric conductivity, and can be used for batteries and energy storage. Sometime for electroplating coating is a favorable option and processes some a fine surface die casting parts for aerospace industry. Titanium zinc alloy is very light metal material, and with high hardness, and used for aerospace and dental implant in medical industry.
Conclusion
From the above information,Different composition zinc alloys ,different applications. By choosing the right zinc alloy, manufacturers can optimize performance, reduce costs, and meet the specific demands of various industries. With the development of technology and the progress of society, zinc alloy die casting parts will become more popular, but also their applications more wider. Our manufacturer should catch the precious opportunity to grow ourselves continuously.