Frequently Asked Question
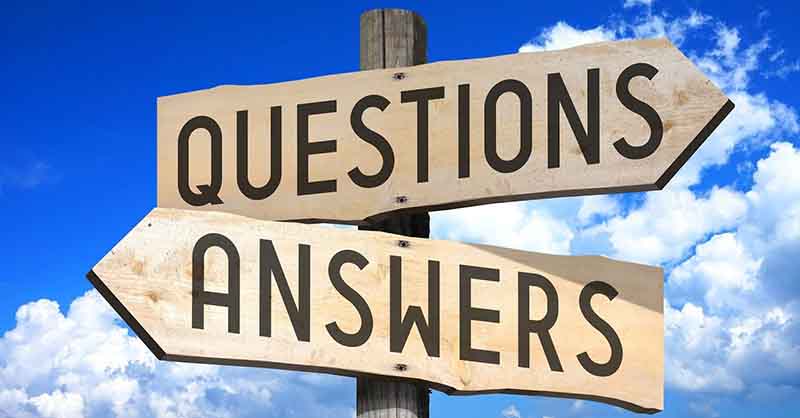
Q: What is Zinc Die Casting?
A: Zinc die casting is zinc casting part procedure, means the worker will melt solid zinc alloy block into liquid, and under the strong pressure of hot chamber die casting machine, press this liquid zinc into metal die, then cooling the die , make liquid zinc to return various shaped solid. Then eject the solid zinc shaped parts from the die. In general, zinc block solid become into liquid zinc at 450 degree in the temperature. But also, the rough shaped zinc parts need more post process to process it.——FAQ NO.1
Q: Which products are made from zinc casting and popular ?
A: In our daily life, zinc casting products are also popular, from Home Appliances to Industrial Usage. Zinc casting is used to make a variety of household items, including belts buckles, furniture inserts, door handles, and locks. In another one, our car key case cover, which made from zinc casting parts and plastic injection parts together. With the development and progress of society, Zinc casting products will become more and more common. ——FAQ No. 2
Q: What are the materials used in zinc casting?
A: Zinc alloys are commonly used in die casting due to their excellent fluidity, cost-efficiency production and resistance to corrosion. These zinc alloys Include the below types.
Zamak Alloys (most widely used in die casting):
- Zamak 2 (Zn + 4% Al, 3% Cu, 0.06% Mg) – Highest strength, good hardness, with excellent wear resistance and anti-collision.
- Zamak 3 (Zn + 4% Al, 0.03% Mg) – Excellent balance of strength and ductility (most common), create thin wall and complex structure small size parts.
- Zamak 5 (Zn + 4% Al, 1% Cu, 0.06% Mg) – Improved hardness and creep resistance, suitable for precision dimensions die castings.
- Zamak 7 (Low-Aluminum variant) – Better corrosion resistance, maintain good performance when exposed to harsh environments
ZA Alloys (Higher aluminum content for stronger parts):
- ZA-8 (Zn + 8% Al, 1% Cu, 0.03% Mg) – Used for gravity casting, reduce viberations of heavy mechanical components.
- ZA-12 & ZA-27 (Higher Al, Cu, Mg) – Stronger but less castable than Zamak, And keep good fluidity of melting material.
———-FAQ No.3
Q: What is the use of zinc casting in automotive industry?
A: With more and more trucks and cars are born, more zinc casting products need meeting demand of automotive parts and car decoration, because the drivers and the boss want to some car gifts and crafts. So zinc casting products play a indispensable role in automotive industry. Such as our recent newly development product, which is car key case cover, either protects the car key well, or decorate the car key. In exception of these, we have more blank market to develop in car and automotive industry.——-FAQ No. 4
Q: How Many Surface Finishes Are For Zinc Casting ?
A: Zinc castings typically have a variety of surface finishes, each suited for different applications depending on aesthetic, functional, and protective requirements. Common surface finishes for zinc castings include the below options.
1. As-Cast Finish The natural finish straight out of the mold without any post-processing. It retains the texture of the mold.
2. Machined Finish The casting is machined to create a smoother surface, often used to meet tight tolerances or specific surface texture requirements. Components requiring precise dimensions or smoother finishes.
3. Electroplating (e.g., Nickel, Chrome, Zinc) A metal coating applied through electrolysis for corrosion protection, enhanced appearance and aesthetic, increased wear resistance and prolong its application life. They are commonly used for Automotive components, decorative parts, and functional items needing corrosion resistance.
4. Powder Coating A durable, protective, and decorative coating applied as a powder and then cured under heat. Used in environments where corrosion resistance is important, such as in outdoor applications. meanwhile build a good appearance and decoration.
5. Painting Zinc castings can be painted using conventional techniques, such as spraying, for aesthetic or protective purposes. Such as consumer goods, automotive parts, or any application requiring a customized appearance.
6. Anodizing Although more common with aluminum, certain zinc alloys can be anodized to create a protective oxide layer, improving corrosion resistance and surface hardness. Used in select industrial applications requiring enhanced surface protection.
7. Buffing and Polishing Mechanical processes to achieve a high-gloss or mirror-like finish on zinc castings. Applications: Decorative items like hardware, jewelry, or automotive parts.
—— FAQ No. 5
Q: What Are The Advantages Of Zinc Alloys?
A: Zinc alloys offer several advantages, especially in equipment manufacturing, automotive, and electronics. Some of the key advantages include:
- High Strength And Durability
- Good fluidity And Ductility
- Excellent Castability
- Strong Corrosion Resistance
- Create Superior Surface Finishing
- High Wear Resistance
- Lower Melting Points
- 100% Recycled And Green ECO-Friendly
- Good thermal and Electrical Conductivity
—— FAQ No. 6
Q: How Much Is Zinc Die Casting Part Cheaper Than Aluminum One ?
A: The cost difference between zinc alloy casting parts and aluminum alloy casting parts can vary based on several factors such as production volume, production cycle time, the raw material cost, consumption energy cost and specific alloys material used. Generally speaking, zinc alloy casting parts tend to be 20% to 40% cheaper than aluminum alloy casting parts. Let’s break down the reasons behind this cost difference.
1. Material Cost
Zinc alloys are typically higher as raw materials compared to aluminum alloys, though the price difference can fluctuate depending on market conditions. But the zinc alloys raw material cost is 2-3 times of that of aluminum alloys.
2. Lower Process Cost
- Lower Melting Point: Zinc alloys melt at around 380°C (compared to 650°C for aluminum), meaning less energy is needed during the casting process. This significantly reduces the energy cost in producing each part.
- Faster Cycle Time: Zinc solidifies and cools faster than aluminum, allowing for faster casting cycles. This leads to higher productivity and lower labor costs per part.
- Tool Life: Zinc casting requires lower temperatures, which results in less wear and tear on the molds. The molds for zinc casting typically last longer, resulting in lower tooling maintenance and replacement costs over time.
- Thinner Walls & Intricate Parts: Zinc alloys allow for thinner walls and greater detail in casting than aluminum. This means that zinc parts can sometimes be made lighter or more efficiently, further reducing costs.
3. Part Complexity and Tolerances
- Dimensional Precision: Zinc die casting offers excellent dimensional precision, often reducing or eliminating the need for secondary machining operations. Aluminum parts sometimes require more post-processing, which can drive up the cost.
- If the parts require tight tolerances, zinc casting can often produce these more consistently and with less post-processing, which makes zinc parts less expensive to finish.
4. Mold (Tooling) Cost
- The molds for zinc alloy casting typically last longer than those for aluminum casting because the lower melting temperature of zinc causes less wear and tear on the molds. and make the mold of zinc casting produces more qualified cast parts and save more production cost.
5. Volume and Production Efficiency
- Mass Production: Zinc is particularly advantageous for high-volume production due to its fast cycle times and mold longevity. So the production cost difference between zinc and aluminum die casting can be significant. Zinc die casting production cost is up to 30–40% cheaper per part than that of aluminum in some cases.
6. Post-Processing
- Zinc castings generally require less machining or finishing compared to aluminum. Aluminum, being harder and more abrasive, can incur higher post-processing costs. Zinc parts are also easier to plate or finish.
- Zinc parts can be polished, painted, or powder-coated easily, offering a cost advantage in finishing compared to aluminum parts, which often need more extensive surface preparation.
In Summary, From the overcost between zinc and aluminum die casting part, the overcost of zinc die casting is far lower than that of aluminum. Although the raw material cost of zinc alloy is 2-3 times of aluminum one, when these raw material is processed into useful die casting part, the overcost of zinc die casting is 30-40% of aluminum die casting. So zinc die casting part is ideal, better than aluminum one.
—— FAQ No. 7
Q: About Zinc Die Casting Component Electricity Conductivity ?
A: Zinc die casting components are used in various industries, including electric communication, due to their strength, durability, miniature and ability to form intricate shapes. However, when it comes to electrical conductivity, zinc has moderate conductivity compared to other metals.
Zinc’s Electrical Conductivity
Zinc has an electrical conductivity of approximately 16.6% IACS (International Annealed Copper Standard). This means zinc conducts electricity at about 16.6% of the efficiency of copper, which is the standard at 100% IACS.
Zinc Alloy Compostion
Comparison with Other Metals: Copper: 100% IACS (very high conductivity) Aluminum: Around 61% IACS (widely used for electrical purposes) Zinc: Around 16.6% IACS (moderate conductivity)
While zinc’s conductivity is significantly lower than copper and aluminum, it is still usable in applications where moderate electrical conduction is sufficient or where the primary function of the component is mechanical support, shielding, or corrosion resistance rather than optimal conductivity.
—— FAQ No. 8
Still Have Questions?
If you have other questions about zinc casting, or any inquiry about your project for die casting zinc alloy part. You can contact us by phone or take your message to us , welcome to your inquiry any time.