Finished products install and package is a comprehensive department in the industrial factory, All parts are reached at this place at last after passing a few processes. whenever metal parts or plastic plastic, operators begin to have a right installment and testing under a right guideline. Some Metal parts may be installed together with screws. inside put some of plastic parts if necessary. something like this , a finished products is gone. But also in accordance with client’s requirements, worker put some finished products into accordingly packaging box and cartons. This is the main occupation of the department. They either control the quality of finished products or package these products in right way.
- Check outsourcing coated parts surface appearance
- Install zinc alloy parts into a finished product or functional part
- Fit embed part out of zinc alloy parts and complete a process
- Record the quantity of finished products and unfinished products process
- Sort out different category of products ,especially Good products and No good products
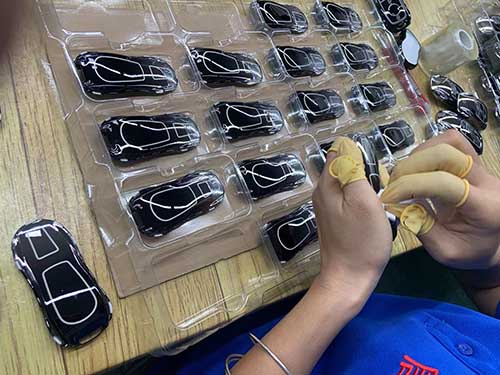
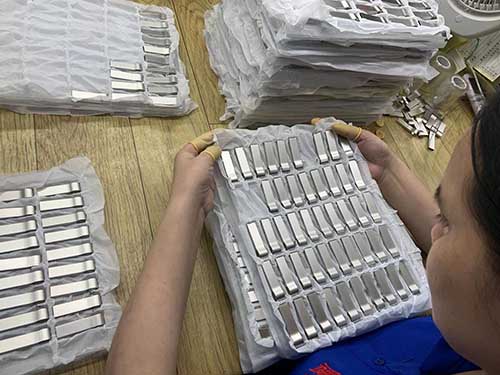
Check Outsourcing Coated Parts Appearance
TangSheng Hardware Technology produce mainly two kinds of parts , include of zinc alloy die casting parts and plastic parts , These parts should be outsourced to do a good surface treatment. They may be coated by outsourcing factory, spraying oiled or electroplated. afterwards, These outsourced parts is be back to our factory, firstly, they arrived at our finished products installing and package department, our worker begin to check the appearance of these parts, and pick up some of imperfection and defective parts, sort them out in order.
Check The Appearance Of Outsourced Plastic Parts
To check the appearance of outsourced plastic parts, a thorough visual and dimensional inspection is essential to ensure they meet both functional and aesthetic requirements. Here’s a step-by-step guide on how to conduct an effective appearance check.
1. Surface Finish
Verify if the surface finish (e.g., matte, glossy, or textured) matches the design specifications. The finish should be even across the part. Look for uneven spots, streaks, or areas that looks impacting the appearance of the part. Check for scratches, scuff marks, or any damage on the surface. Check for any dark spots or burn marks caused by overheating during the molding process. Look for flow marks or ripples, which are visible patterns created by the flow of molten plastic in the mold. Inspect the surface for any bubbles, peel, or air- trapped inside the part, especially in transparent or translucent plastic parts.
2. Color Consistency
Ensure the color of the plastic part is uniform across the entire surface, with no discoloration or color streaking. If the parts are produced in batches, compare parts across different batches to ensure there is no significant variation in color between them.
3. Dimensional Inspection
Observing warping or distortion, Putting it on a flat surface or measurement tools like calipers to ensure the part holds its intended shape. Measure key dimensions of the part using calipers, micrometers, or other appropriate measuring tools, and ensure the part is within the tolerances range of dimensions.
4. Packaging Inspection
Inspect the packaging to ensure that parts are properly protected during shipping and handling. Poor packaging can lead to surface damage or contamination, affecting the appearance, or damage the apperance of the part.
5. Reference Samples
Here have a pre-approved sample or quality standard access documents on hand to compare the appearance of new parts.
Check The Appearance Of Outsourced Zinc Die Casting Parts
To check the appearance of outsourced zinc die casting parts, we follow these steps to ensure that they meet client’s quality standards.
1. Surface Finish Of Outsourced Parts
Inspect the surface of outsourced metal parts if any blowholes, porosity, or shrinkage is discovered. These common issues in casting can affect both appearance and structural integrity. Check the surface finishes (matte, polished, or plated) are consistent across the parts. Once any unexpected roughness or irregularities unless specified occurred, Our inspector will refuse this lots of outsourced parts. We inspect electroplated, coated, or painted zinc die casting parts for uniform coverage, and ensure that no areas are thin, blistered, or peeling. For plated finishes like chrome, nickel, or zinc, the color should be consistent across the part.
2. Dimensional Tolerances
Cast parts can sometimes warp during cooling. Use measurement tools like calipers, micrometer and graph measuring instrument to ensure the part’s shape is within the specified tolerances. Ensure the part’s dimensions match the drawing specifications. For critical dimensions, this may require precise measurement tools like coordinate measuring machines (CMM).
3. Coated Material Bond And Thickness Testing
If the part has a specific surface treatment (e.g., powder coating, anodizing, or electroplating), you may need to perform tests like a thickness gauge test or adhesion test to verify that the finish meets technical specifications.
4. Packaging Inspection
Finally, check that the parts are packaged properly to avoid damage or scratching during shipping and handling. These factors cause the damage and contamination of these die casting parts.
Install Zinc Parts Into A finished Product or Functional Part
Workers in finished products install and package dept are responsible for installing outsourced zinc alloy parts into a qualified finished product and functional part and packaging them and ready shipping them to our regular customers. Electroplated or oil-spraying die casting parts are all finished assembly and package here.
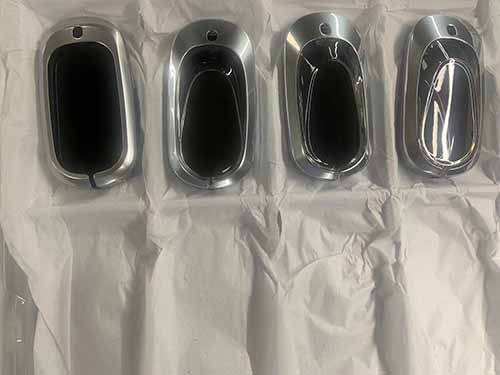
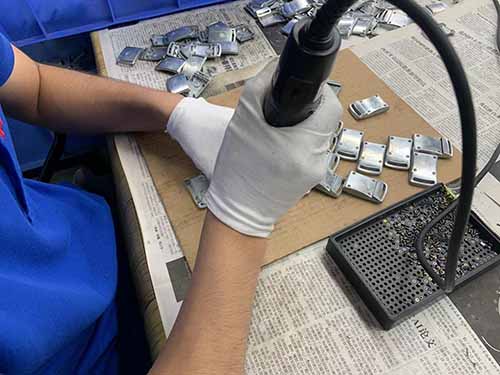
Assemble Zinc Alloy Parts With Screws For Further Surface Finish
For zinc alloy die casting parts deburred, they come this dept for a testing install or install together with screws and proceed the next procedure. Workers install these parts as one with screws respectively, then sent them to our polishing production line. Its aim is to be more convenient to polishing the surface of these die casting parts so that electroplating these die casting parts better.
Install Zinc Alloy Casting Parts Into A Finished Product
A finished product composes of a few metal parts and install them together and become a commodity, Then worker will pick up appropriate part and come with suitable another part and install these parts into a finished product. Sometimes, some parts is locked, they will repair and modify these parts until install them into a qualified finished product. At last put these finished products into the reasonable box and package vessel.
Install Some Functional Parts or Unfinished Goods
Some Functional Parts also require to be installed together with several different component. Our worker refers to the first sample or assembly chart from the client, and install the specific requirement components and finish the installment of fuctional parts, such as Flash disk storage mould, multi-functional Metal hook and Electic ciucuit board installment.