When zinc alloy part warping or shrinkage occurred during the casting process, these causes produced due to these issues, like improper cooling rates, mold design, or alloy composition. To resolve these problems, we take some reasonable meatures to tailor resolving problems in accordance with real conditions. By the blew approaches, at last completely solve own detail problem. Good Solutions For Improving Zinc Alloy Casting Part Warping Or Shrinkage.
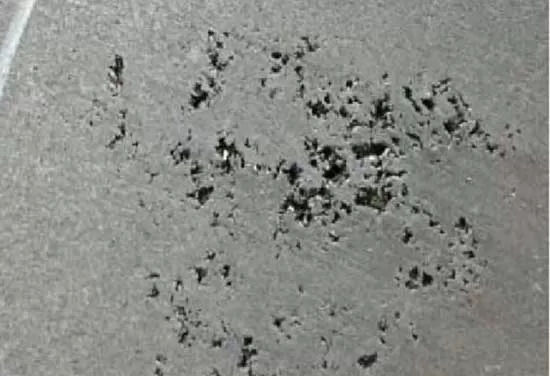
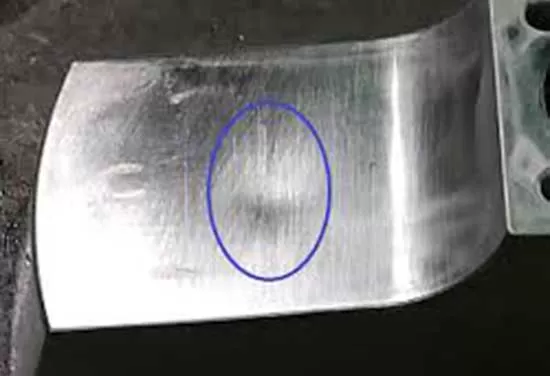
Solutions For Improving Zinc Alloy Part Warping Or Shrinkage
Adjusting Cooling Rates
Cooling channels in the die may be relevant to the defect result, we can optimize these cooling channels to achieve uniform cooling on the surface of the casting part. We check these cooling channels carefully and maintain them clear and throughout. If neccessary, added cooling channels may improve cooling effection. This helps the part solidify evenly, reducing deformation.
Taper or Draft Angle Adjustments
In some cases, Casting part warping was caused by ejection force. In order to reduce ejection forces, we can increase draft angles. This can help the part release without warping in term of without comproming the quality of die casting parts. The taper or bigger draft angles on the surface of casting parts can disperse the ejection stress ejection forces evenly to ejection points, and reduce part warping rates.
Adjustment of Alloy Composition
Zinc alloy composition may cause deformation of zinc die casting part, possible other metal elements ratios in zinc alloy. We should adjust the balance of zinc, aluminum, copper, and magnesium until process the qualified zinc casting parts. And we explore zinc alloy composition continuously and adjust the balance of zinc, and make our effort to meet more custom die casting parts projects.
Improving Gates and Runners
We can improve the gating and runner system to maintain even material flow and reduce shrinkage issues. Modify the gating system to address balanced material distribution across the mold. Right positioning gates on the mold can help minimize areas prone to shrinkage or air entrapment. Another one, keeping entry runners clear and throughout is very important.
Venting Improvements
Techinician can improve venting to let trapped gases to escape, and avoid the gas is stay and causes improper internal pressure and deformation. Improve venting locations in the die, ensure that air has a clear path to escape from all critical areas once the gas generates in the lumen of mold under high pressure. Overflow gas can be escaped during the zinc die casting process.
Cast Part Post-Casting Treatment
Our Engineers suggest that appling stress-relieving techniques such as heat treatment to the cast parts after ejection to relax any residual stresses. Execute post-processing steps such as heat treatment or machining may be added to the workflow. Depends on the extension of warping of the cast parts, we can treat these imperfection cast past until meeting the quality standards of client.
Die Surface Modification
Using a coating or texture to the die surface to improve the flow of the alloy, reduce friction and block forces during casting parts. Meanwhile, it also create a smoothness and even surface of the casting part, and improve part quality. Die surface repair and modification can prevent the warping and defects of the parts from die casting process.
Summary
The above points are considered before designing a set of reasonable metal casting die, good Solutions For Improving Zinc Alloy Casting Part Warping Or Shrinkage. In case die casting part warping or shrinkage during zinc alloy casting process, We should check the above link keys step by step and find good solutions to resolve the problem accordingly. We always produce custom die casting parts, the problem about the defects of casting parts may be often occurred . So we should face these problems at positive side, with our enrich production experience for decades, and try our best to resolve sudden accidents during die cating process.