Zinc alloy die casting components become more and more commoner in people eye-sight, more manufacturers have gone into zinc casting industry. What they are discussing most is that how they can produce high quality zinc alloy die casting components to meet the demand of the market in recent days. This is an issue of production technique, involve of work experience, labor cost, suitable die casting machine and process method. It is so complex and integrated things. Most experts think that Hot Chamber Die Casting is The Key Technique Of Zinc Alloys Casting. It also effectively resolve the key problem of how to producing high quality zinc alloy casting components.
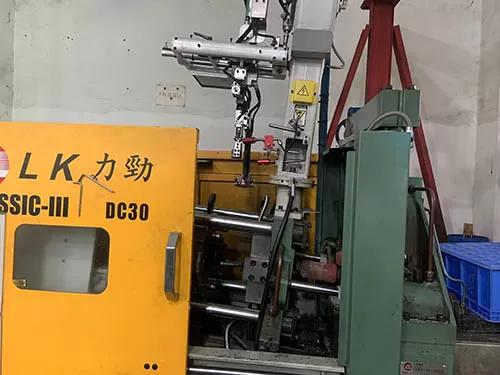
What is hot chamber die casting ?
The hot chamber die casting is a typical manufacturing technique used to produce casting metal parts. By injecting molten metal into a mold cavity under high pressure, solidify intended shape parts with smooth surface finish and tight tolerance dimensions. It is commonly used for metals with low melting points, such as zinc, magnesium, and certain lead and tin alloys.
Characteristics of Hot Chamber Die Casting
Interior Furnace
With interior furnace, preheating the casting metal into molten metal. This molten metal is ready to be directly supplied to the die casting chamber. Heat power with electricity power, and eco-friendly and clear, and temperature is stable and melt cast metal fully.
Injection Mechanism
A plunger or piston forces the molten metal through a gooseneck and into the mold cavity. Carrying with the “gooseneck” is submerged in the molten metal with good fluidity. The plunger seals it during the injection process. Under high pressure and ensure the die casting part has a smoother surface finish.
Quick Cooling and Solidification
After injection, the molten metal rapidly cools and solidifies in the mold cavity when the overall casting part is cooled uniformly, shaping the part. This is due to zinc material low melt points and require lower temperature and heat energy, which can cool and solidify quickly.
Part Ejection
Once solidified, the die opens, the casting is ejected from the mold or die by ejector pins. The operation actions are fully automated, controlled by digital program. Proper angle draft design is neccessary and ensure the fine cast parts seperate from the casting die smoothly and reduces defective parts.
Fast Cast Cycle
The process is highly automated and fast cast cycle, allows a rapid production of part cycle. It is suitabel for a high volume production, raising production rate and products quantity without any compromising high quality. Automatic production line saves more labor cost and reduces humen hurt largely.
Advantages of Hot Chamber Die Casting
- High Efficiency Productive rate: The integrated design allows quick and continuous production cycles.
- Precision and accuracy: Produces parts with excellent dimensional accuracy and fine surface finishes.
- High Efficiency for Small to Medium Parts: Ideal for mass production of small to medium-sized parts with thin walls.
- Material Unique Properties: Well-suited for metals with low melting points and high fluidity, such as zinc and magnesium alloys.
Hot Chamber Die Casting is Key Technique for Zinc Alloys Casting
Producing Zinc Alloy Casting Components Needs Key Technique: Hot Chamber Die Casting Process ,The hot chamber die casting process is key technique for manufacturing high-quality zinc alloy components. This process offers high efficiency and precision, making it the ideal method for producing intricate and small and medium sizes of zinc parts. The Technique Of Supporting Casting Zinc Alloy With Hot chamber Die Casting Machines had become so essential.
Why Hot Chamber Die Casting is Key Technique for Zinc Alloys Casting
- Low Melting Point and Good fluidity
Zinc alloys, with their relatively low melting points, are perfect for the hot chamber process. The integrated melting system ensures a seamless flow of molten metal into the mold cavity. With additional melton zinc’s good fluidity, ensure the surface finish of die casting is more smoother , compare to other melton metals. - Fast Casst Cycle
Equipped with interior furnace, preparing for stable melton zinc in the melton pot, makes the rapid solidification and automated operation enable the production of a high volume of components with consistent quality. - Precision and Complexity
Zinc alloys have excellent fluidity, Under high pressure ensures the creation of parts with thin walls, complex geometries, and fine surface finishes, critical for automotive, communication, and other industries. - Material Efficiency Zinc’s recyclability and minimal waste generation in modern manufacturing. It also conform with goals of sustainability and cost-efficiency in global green health environment.
- Lower production cost: zinc alloy has a lower melting point, lead to saving more thermal energy during heating the metal. Meanwhile reducing the die casting cooling and solditifying time during processing the die casting part. Whenever production time ,or energy consumption, these save more production cost.
Other Key Techniques in Hot Chamber Die Casting
- Optimized Mold Design: Designing cooling channels for uniform solidification. minimizes defects like porosity or warping.
- Precise Temperature Control: Maintain stable temperatures for zinc alloy fluidity,avoid overheating to prevent tool wear.
- Fine Surface Finishing: Ensure components have fine surfaces ready for post-processing like plating or painting.
- Tooling Quality: Choose durable high speed steel materials for molds and gooseneck systems to withstand repeated cycles without deformation or damage.
- Quality Control Measures: Executes rigorous inspections to detect casting defects and ensure dimensional accuracy.
By Properly using the hot chamber die casting process, we can produce high-performance zinc alloy components that meet the demands of diverse applications while maintaining cost-effectiveness and sustainability. The above helps us to explain the reason that Hot Chamber Die Casting is Key Technique for Zinc Alloys Casting in detail. Other key techiques are neccessary if the consistent high quality mass production should be conducted.
Conclusion
Choosing Hot Chamber Die Casting Process to Produce Zinc alloy Casting Components. We will produce high quality zinc alloy die casting component, which is not only suitable for client’s requirements and functionality, but also can raising production effective and production quantity. As this technique advancement, we can be satisfied with custom demand and special requirements from business partner and individual and personalized order. Under at lower cost, producing a high volume high quality zinc die casting components for industry and market all over the world.