The demand for miniature zinc alloy components has increased in recent years, driven by advancements Electronic and IoT Network industries. These Miniature zinc die casting parts are high precision, durable and cost-efficiency, just meet the specific requirement in these industries. So more and more die casting manufacturers invest die casting machines and automational production line to produce mass miniature part zinc die casting. The process of manufacturing these components requires advanced techniques to ensure high quality and consistency. Among the various methods available,Hot Chamber Die Casting Machines are For Miniature Parts Zinc Die Casting Process . This also is advantages for casting zinc alloy with hot chamber die casting machines.
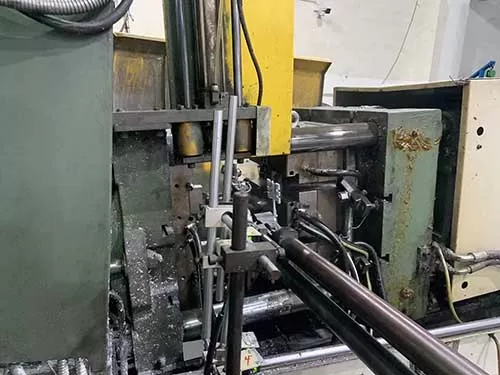
Zinc Alloy Die Casting Parts Process Step By Step
How Does Zinc Alloy Die Casting Work ?Firstly, zinc alloy is molten in integrated furnace reservior, filter impurity among the molten zinc alloy and keep preheated purified molten zinc alloy. Then using a high-pressure piston to force molten zinc alloy into a preheated steel mold, also known as a die, where zinc casting part shaped in term of achieving evenly cool and solidified. The mold opens, the zinc die casting parts are ejected out from the die. The process is fast cast cycle, includes the following key steps.
Preparation
Melting zinc alloy material in prepaired reservior by integrated electric furnace, and filter impurity inside molten zinc alloy by overflow, maintained at a controlled temperature to ensure molten zinc alloy perfect fluidity. The precison casting die is pre-heated to minimize thermal shock and ensure uniform cooling. We will have a good preparetion for zinc alloy die casting process.
Injection
High-pressure piston forces the molten alloy into the preheated mold, filling even the smallest cavities fully to produce detailed components. Because zinc alloy material have a good fluidity and a lower melting point, it is pressed into the cavities of precision mold and fill these cavities fully and made smoother surface finish casting part. And finish each zinc die casting cycle in few seconds.
Solidification and Ejection
The prehead casting die is cooled evenly and makes the molten zinc alloy solidification rapidly, shape zinc die casting part. Then the die opens automatically, the part is then ejected from the casting die. To prevent some defects of solidification from uneven cooling of zinc die casting part, we should design proper cooling channels and venting setting of the mold.
Advantages of Hot Chamber Die Casting Machines
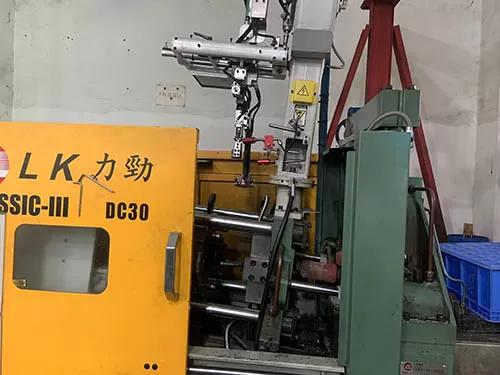
1. Accept Precision and Detail
Hot chamber die casting machines excel at producing parts with intricate geometries and precision dimensions. So they can produce in high volume high quality miniature components used in applications like electronics and communication equipment.
2. High Production Efficiency
The fast cycle times of hot chamber die casting machines enable the mass production of miniature parts without compromising quality. These due to the low melting point of zinc alloys.
3. Consistent Quality
The numberious control injection process ensures uniformity in dimensions and intricate zinc geometries. Zinc alloy low shrinkage ensure cast part dimensional steady. Advanced monitoring systems in machines reduce defects such as porosity and surface imperfections.
4. Provide Cost-Effective Manufacturing
The machines high Cost efficiency production minimizes labor costs and energy consumption. Zinc’s recyclability reduces material wastage, contributing to sustainability of zinc alloy. Zinc alloy low melting point reduce the cast cycle time, The ovrall manufacturing cost is lower, than other metal casting.
In summary, zinc alloy die casting machines are good at producing miniature zinc die casting components depend on their work principle, which belongs to hot chamber die casting machine. In additional one, zinc alloy special material ,can be forced into the mold under high pressure, and formed , solidify, cooling and ejected it out from the mold. The machine can process high quality and high precision zinc die casting components.
Why Hot Chamber Die Casting Machines are Suitable for Miniature Parts Zinc Die Casting Process
When knowing more about hot chamber die casing machines from the above information of the machines work principle and advantages, we think hot chamber die casting manchines is more suitable for producing miniature parts zinc die casting. That is the reason that the machines can process metal die casting components with high precision, lower cost in high volume in fast cycle. The following we will have key points to describe.
With interior furnace and gooseneck machenism
The integrated furnace can melt zinc in the zinc die casting, with high pressure injection process, though gooseneck machenism, under high pressure forces the molten zinc into the steel mold, shapes good surface finish zinc die casting parts. For its casting die had been designed in precision, so the part is high precision , a tight dimension tolerance.
Miniature Size and Complex Geometries
Zinc die casting components is focus on miniature and medium size due to zinc alloy metal is a low melting point metal material, good fluidity of melton zinc and a little shrankage. And ensuring their high quality standards in mass production. In another one, Complex geometries design is also a highlight of zinc alloy die casting component, added high pressure drive, and making the molten zin fill the cavities of casting die fully, shapes more perfecter geometries in die casting process.
Minimized Waste Material and Recylibity
Zinc alloy waste material is minimized during mass production due to good fluidity of molten zinc alloy. So this enables saving more excess material during die casting process. But we can’t exclude die casting component’s burr, flashing and part line in mass production. For these processed burr waste, we can reuse them, because zinc alloy material is eco-friendly and recylable.
Conclusion
Hot Chamber Die Casting Machines are For Miniature Parts Zinc Die Casting Process. It creates intricate designs with precision, efficiency, and cost-effectiveness makes them indispensable for manufacturers. Through advanced technology and innovative solutions, these machines continue to push the boundaries of what is possible in miniature zinc casting. As industries enlargement, the role of these machines in shaping the future of manufacturing will only grow, reinforcing their position as the ideal choice for producing miniature parts.