Various custom die casting parts become more and more popular since industry development had a qualitative leap. So the technique of die casting process still improvement and innovation under practise production. More demands of high precision die casting parts from more industries, More manufacturers require providing high quality custom die casting parts to match with the requirements of specific and personalized. But it requires a metal die casting manufacturer to handle technical expertise, efficient processes, and strict quality control links. As the below, how to provide high quality custom die casting parts? Let us have an article to introduce more about it .
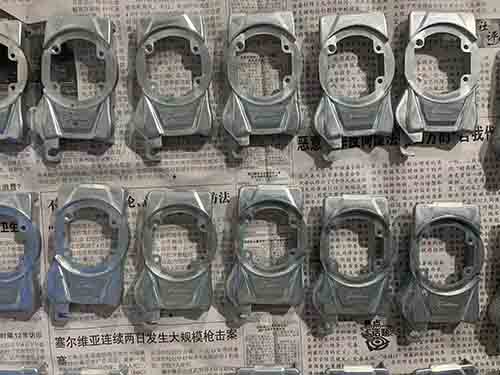
What is Custom Die Casting Parts ?
Custom die casting parts means through the die casting process to meet specific design, functional, or performance requirements provided and provide qualified custom components with die casting process. Unlike standard parts, custom parts are tailored to fit unique requirements and specifications, often requiring specialized molds, materials, and production processes.
Characteristics of Custom Die Casting Parts
Tailored Design
Customization design for client requirements , involves unique dimensions, geometries, and functions. It can need complex shapes, thin walls, or intricate details. Designer and engineers have a continuous improvement and modification for product and mold until fitting the spefications of customer completely.
Special Material Requirements
Casting specific metals or alloys (e.g., zinc, aluminum, magnesium), The casting die withstands repeative wear and high temperature during mass production. The special Material of the die casting part should conform with custom part’s functionality, practise applications and being assembled reasonably.
Precise Tolerances
High precision to ensure the part fits seamlessly with other components in an assembly smoothly. If neccessary , some custom parts may be processed by cnc machining process to meet the specific requirements of tight tolerance.
Surface Finishing
Some advanced finishing processes like powder coating, polishing, or plating for enhanced appearance and durability. Some reasonable process methods to achieve client demand. To minimize further post-process, we can polish the surface of the cores and cavities of the mold, and enhance smoothness on surface of die casting part and ensure as-cast surface finish fine.
Applications of Custom Die Casting Parts
Custom die casting parts are widely used in many industries, such as automotive, communication, consumer electrics, medical devices, mechanical equipment and furniture fields etc. With innovation of improvement of die casting process, more precise and durable die casting component will fit the demand of industrial development. As the following have a detail description.
Automotive
Engine components, brackets, housings, and decorative trims in interior parts. These products divide into two type castings, and aluminum and zinc alloy die castings, small and medium sizes are made of zinc die castings , but larger sizes components belong to aluminum die castings.
Electronics
With the growth of personalized requirements, Heat sinks, enclosures, and connectors design will have a big change. custom die casting parts include of aluminum and zinc alloy die casting components, will transfer into meeting unique requirements in electronic industry.
Industrial Equipment
Pump housings, gears, and structural components will become personalized and custom. Their design and production all need be customized. With consistent creation and improvement of the functions of industrial equipment, machinery manufacturers need more tailored die casting components to raise its production capability and production effective.
Aerospace
Lightweight and durable components are favor of aircraft systems. They are commonly made of alloy aluminum material in order to have more lightweight. With the development of aerospace explore, more airchrafts need be invented, custom lightweight components should be designed and produced.
Medical Devices
Precise parts for medical instruments and devices. These devices require some precise die casting parts and also fit the functionalities and applications of these medical devices. And making manufacturer provide more custom die casting components to meet the demand of creative medical devices.
Supplying High Quality Custom Die Casting Parts Guide
We are as one experienced custom die casting parts manufacturer, have the below ability so that can proceed custom die casting project and meet in sufficient to some unique requirements of design , production, quality control and production improvement.
1. Tailored Design
Collabrate closely with customers to develop part designs that meet functional and aesthetic requirements. Use DFM (Design for Manufacturability) to optimize designs for die casting. We can utilize CAD and simulation tools to analyze mold flow, shrinkage, and thermal parameter and predictive defects resolved ahead before production.
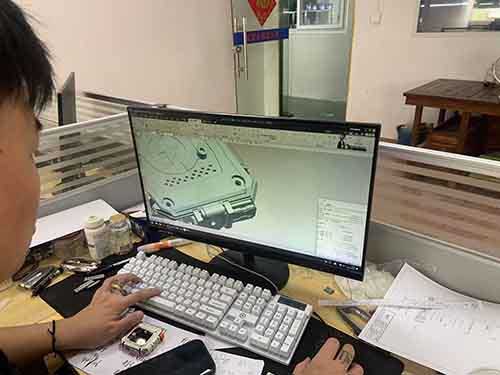
2. Material Selection
Choose premium metal/alloy according to the part practise’s applications, durability, and cost considerations. The compnay offers expert guidance on material properties like strength, corrosion resistance, and machinability.
3. Precision Mold Making
The precision molds are made from high-grade steel and using advanced machining methods like CNC machining and EDM to ensure durability and accuracy. We design molds tailored to specific customer requirements, achieve tight tolerances and complex geometries.
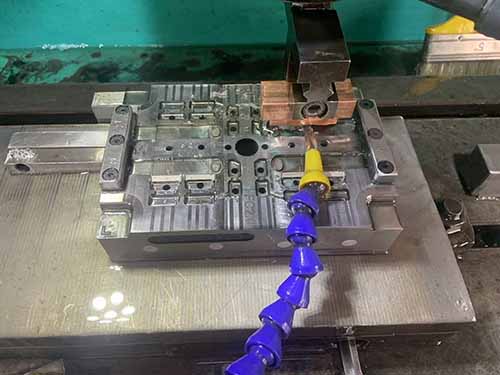
4. High effetive Die Casting Processes
Adopting state-of-the-art die casting machines to ensure consistent pressure, temperature control, and fast cycle times during die casting process. Apply process optimization techniques to minimize porosity, defects, and material wastage within the process. Incorporate multi-slide die casting or other advanced methods to process complex and high-precision parts.
5. Surface Finishing and Secondary Operations
TangSheng Hardware Technology offers various die casting surface finish options such as polishing, powder coating, anodizing, or electroplating to enhance aesthetics ,corrosion resistance and durability. Address secondary machining processes (such as drilling, tapping, or CNC machining) for tight tolerances.
6. Stringent Quality Control
Use advanced inspection equipment like CMM (Coordinate Measuring Machines), X-ray testing, and spectrometers, We ensure parts meet specifications and industrial quality standards. Follow ISO or IATF standards for automotive, aerospace, or other industries. Execute stringent quality management regulations for each process link.
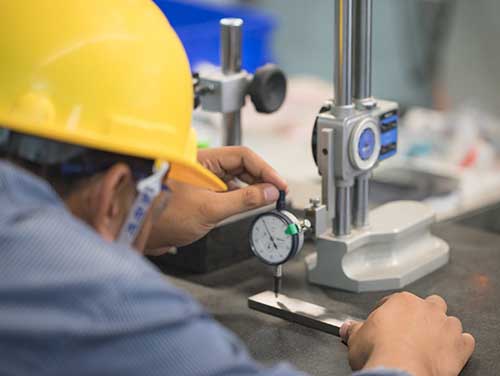
7. Continuous Improvement
Training, R&D, and advanced technologies to stay competitive and meet the latest market and industry needs. With appearance of some problems during trial production, products improvement and mold repair is indispensable. Worker operation skills are improved consistently.
By focusing on these aspects, a metal die casting manufacturer can consistently deliver high-quality custom die casting parts to exceeded customer. As a professional zinc die casting manufacturer with a meatured engineering team, these strategies could align well with your capabilities and goals!
Conclusion
Being known from the above information, how to provide high quality custom die casting parts ? A manufacture should have a mature die casting technique, powerful design engineering team and strict production process management system. What’s more, it also need have the ability for creation and improvement of product in trial stage to meet client special requirements and help client to realize from a design concept to practical project.