Nowadays, zinc die casting is used widly in many fields, especially automotive, communication and consumer goods. The great reqirements from market at home and abroad will need more zinc die casting manufacturers to produce high quality zinc die casting parts and components to meet the demands cross various industries and fields. Just you are one of zinc die casting factory, how to produce high quality automotive parts zinc die casting? We will guide you to have a good solution undergoing.
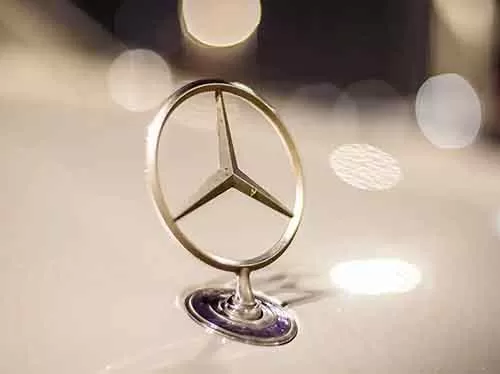
Table of Content
- Applications Of Automotive Components Zinc Die Casting
- Producing High-Quality Zinc Die Cast Automotive Parts Guideline
- Conclusion
Applications Of Automotive Components Zinc Die Casting
Automotive component requires tight tolerance dimension, strong integrated structure and excellent mechanical properties, and endure wear and corrosion in harsh environment and worse weather. The specific requirement for automotive application normalizes manufacturing standard for various automotive components. Especially for die casting manufacturers, they should follow the automotive industrial management system, and normalize mass production and quality inspection regulations, and ensure making high quality automotive components in high efficiency. Of course, applications of automotive components zinc die casting are widely, this due to zinc metal properties. what’s more, they have been used in many sectors in automotive industry.
The Advantages of Zinc Alloys
- Good fluidity molten metal Material: Molten Zinc alloys material has a good fluidity, which allows for rapid filling of the mold fully. This process creates components with intricate shapes and fine details surface finish.
- Rapid Cooling and Solidification: Zinc has a low melting point (around 420ยฐC or 788ยฐF), so it cools and solidifies quickly. This shortens cycle times enables faster production speeds and shorten mass production time compared to other metals like aluminum or iron.
- Durability and Strength: Zinc alloys have good strength, toughness, and wear resistance. They are very durable. Especially some specific automotive components withstand harsh environments and marine bench salt corrosion.
- Cost-Effectiveness: Zinc alloys low melt points,fast cast cycle and less energy consumption makes zinc die casting a cost-effective. Also its secondary process produces little waste, and offers long-lasting mold durability.
- Excellent Corrosion Resistance: Zinc alloy has natural corrosion resistance due to aluminum element contained inside. So zinc die casting components can be used widely across diversity fields in many industries. Such as automotive, electronics, consumer goods and appliance and homehold furniture industries.
- Form fine surface finishing: Zinc alloys are all composition metal that is basic of zin element, ~90% zin element content, decides that the molten metal form fine surface finish when casting zinc die casting component.
Applications of Automotive Components Zinc Die Casting
Zinc die castings have obvious strength, tight tolerance dimensional accurancy, low cost and durability due to zinc alloys material unique properties and precision high speed steel die. People find that the typical low cost die casting process can be used for many fields in automotive industry.
- Interior And Exterior Decorative Components: Car Logos, Ornaments, Wireless Charger bases and portable fold frames.
- Security System Components: Safe belt buckes, Airbag cases, brake blades.
- Engine Components: Engine protective cover, engine housing and main chassis for engine.
- Transmission Components: Transmission housing, gearbox housing and stop lever.
- Monitoring System Components: Sensor Housing, Heat Sink and Electromagnetic Interference Shielding.
- Fuel Tube Fittings and Faster: Fuel filter, tube valve and tube fittings.
- HeadLight Serial: Headlight Housing, fixture chassis.
Overall, zinc die casting is a versatile, efficient, and reliable method to produce high-quality components in various sector in many industry. Especially Its Cost-Effectiveness attracts zinc die casting manufacturer. But zinc die casting process is handled by The Technique Of Supporting Casting Zinc Alloy With Hot chamber Die Casting Machines, and require hire skilled experience technician to address it.
How to Produce High-Quality Zinc Die Cast Automotive Parts
As a professional zinc die casting manufacturer with a well-skilled engineering design team, and want to produce premium quality zinc die-cast components for the automotive industry, you should have an advanced understanding of zinc alloys, precision casting techniques, and stringent quality control measures. Also you are similar with specific functionalities and applications of automotive components. Hereโs a structured approach to help you achieve excellence in this field.
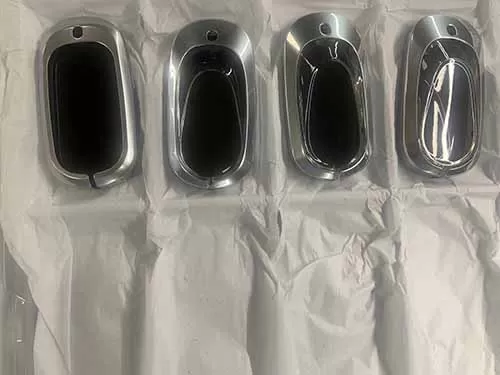
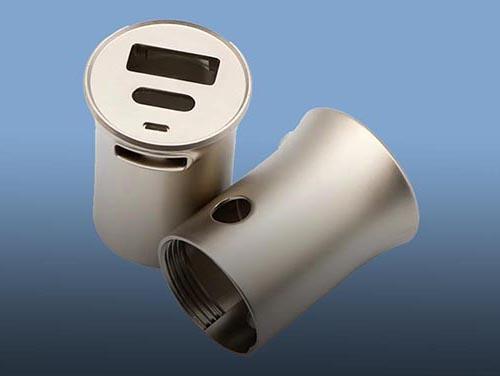
Selecting the Right Zinc Alloy
Zinc alloys are ideal for automotive parts due to their excellent strength, durability, and corrosion resistance. Common zinc alloys, such as Zamak 3, Zamak 5, and ZA-8, each has distinct characteristics. Depends on application and function of the automotive component, die casting manufacturer choose the right zinc alloy to cast it.
Items | Chracters |
---|---|
ZAMAK 2 | Zinc (~96%), Aluminum (~4%), Copper (~3%), Magnesium (~0.05%), Which is highest strength and hardness among ZAMAK alloys |
ZAMAK 3 | Zinc (~96%), Aluminum (~4%), Magnesium (~0.05%), Copper (minimal),with excellent dimensional stability and castability. Most commonly used alloy, used for Consumer goods, automotive components, and electronics. |
ZAMAK 5 | Zinc (~95.5%), Aluminum (~4%), Copper (~1%), Magnesium (~0.05%). With higher strength and wear resistance than ZAMAK 3. It is suitable for parts with mechanical stress, such as gears and brackets. |
ZAMAK 7 | Zinc (~99.99%), Aluminum (~3.9%), Magnesium (~0.02%), having Improved ductility and impact resistance. Thin-walled components with intricate designs fit it. |
ZA-8 | Zinc (~91%), Aluminum (~8%), Copper (~1%). Suitable for both hot and cold chamber die casting. Can process thin-walled and precision components. |
ZA-12 | Zinc (~88%), Aluminum (~12%), Copper (~0.5%). Offers higher strength than ZAMAK alloys. For Bearings, bushings, and heavy-duty industrial parts. |
ZA-27 | Zinc (~73%), Aluminum (~27%), Copper (~2%). It is highest strength among zinc alloys but limited to gravity casting due to high aluminum content. Structural components, wear-resistant parts use it. |
Making Precision Tooling Design and Maintenance
Precision tooling is cornerstone for high-quality zinc die casting. Design precision tooling systems to ensure consistent casting quality, We should be account for these detail factors, like uniform wall thickness, smooth transitions. Appropriate fillets can prevent common defects like warping or stress fractures. Zinc die casting components design guide will as a good referrence. Implement regular maintenance schedules to your dies, it avoids wear and tear that could lead to quality issues. Refer to Zinc casting die maintenance and repair
Maintain Temperature Control and Consistency
Maintain consistent temperature control throughout the die casting process is crucial. Monitor and maintain an ideal temperature range for the die, molten metal. And adjust injection speed. This prevents defefctive issues such as porosity, shrinkage, and gas entrapment. Pre-heating dies helps in creating a uniform casting environment, reducing thermal shock and improving the surface finish of the part.
Using Advanced Casting Technique
Handling advanced casting technique, which is hot chamber die casting technique .This is best choice for automotive zinc parts due to the smooth finish and precise tolerances it provides. Starting vacuum systems to remove trapped air improves casting density and reduces porosity, enhancing the structural integrity of the part. Multi-slide die casting allows more complex shapes and thin-walled parts, which are often required for lightweight automotive applications.
Surface Treatment and Finishing
The automotive industry requires parts with superior finishes for both aesthetics and corrosion resistance. Zinc die cast components can be satisfied of their demands, electroplated zinc die castings are for corrosion resistance, which are exposed to various environmental conditions. Powder coatings or automotive-grade paints provide durable, color-consistent finishes that protect against wear and harsh weather. For components that need a mirror-like surface, polishing offers high-quality finishes.
Follow Rigorous Quality Control and Testing
Quality control is essential in automotive parts production to meet industry standards. Consider these methods. Techniques like X-ray inspection and ultrasonic testing can help detect internal defects without damaging the parts. Conduct mechanical tests to evaluate stress thresholds, impact resistance, and corrosion resistance, which are critical for automotive applications.
Complying with Industry Standards and Certifications
Lastly, compliance with industry-specific standards, such as ISO/TS 16949 for automotive quality management, is essential for meeting global automotive manufacturing requirements. Certifications ensure reliability and quality control, enhancing credibility with automotive clients.
In summary, By complying with the above common guidance, you can ensure the quality of zinc die-cast automotive parts, meeting and exceeding the industryโs rigorous standards.
Conclusion
Overall, Producing high quality parts zinc die casting needs that the manufacturer are similar with diveristy zinc alloys and select the right composition zinc alloy. With precision casting techniques, automative production streamline and stringent quality control rules. Our company posses a well-skilled engineering design team, professional zinc casting technique, matured production procedure, reasonable die casting parts surfce finish and rigid quality control system. With our dedicated services and capability, we will provide high quality automotive parts zinc die casting to our client and business partners.