Many and many Metal components are used in many fields, that makes more and more metal process factories to be built. In these factories, machined metal parts and die casting parts are produced largely. So most of metal machined parts are suit for machinery industry and electric communication field. However, Metal die casting parts sometimes are needed at mass production, the bulk goods has to be formed by metal casting die & mold. But people should take a good consideration of the cost of casting die, compare to machined metal parts, that has additional cost. After balancing the earnings and costs, people will make up their mind that they will make a metal casting die to process casting parts in mass production. So metal casting die & mold manufacturing is certainly made before mass production.
What is Casting Die & Mold ?
Casting die & mold is basic production tool, can produce rapidly prototype and mass production. Any casting production process, drive molten metal pour into a mold to shape metal part. Of course, The process is devided into two types of die casting processes, which are Manual die Casting and Mechanical die casting process. Depends on typically material of the mold, The mold may be Steel molds, Ceramic molds,plaster molds, Aluminum molds and Sanding casting molds.
1. Manual Casting Mold
A simple mold is the hollow cavity or form into which molten metal is poured into the casting molds to create a desired object. but the molds may be made from various materials, such as sand, metal, or ceramic. These molds are rough and simple structure.
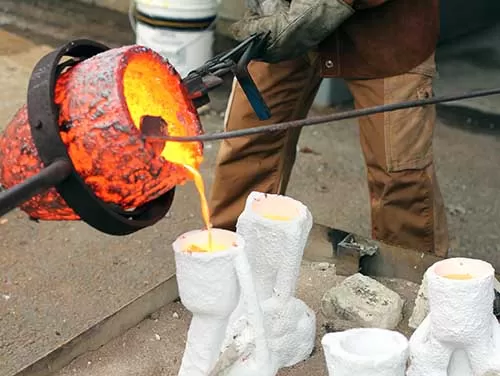
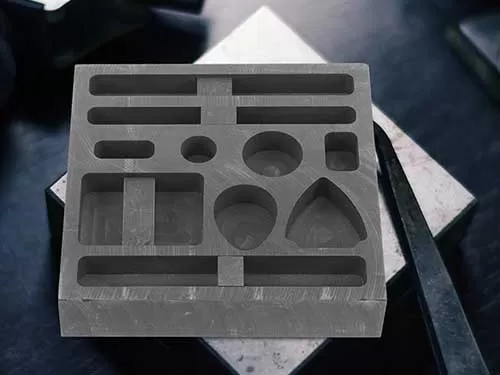
They are destroyed after each use. So they are often made from materials like sand, plaster, or other disposable substances. Such as Sand casting mold, plaster mold. Definitely a rough casting part can be formed when pouring molten metal into the mold. Once the metal cools and solidifies,the mold is then opened (or broken in expendable mold casting) to release the final product.
2. Mechanical Casting Die & Mold
As a specific casting process, means molten metal is injected into a mold by reasonable die casting machine under high pressure. Cooling and solidify the casting part and eject the part from mold. The molds are typically made from hardened tool steel. They withstand the high pressures and temperatures in die casting. Especially hot -chamber die casting machines are used to manufacture zinc alloy casting products with medium and small-sizes. But using cold-chamber die casting machines to product aluminum alloy casting components with large sizes. So we can process custom die casting parts completely.
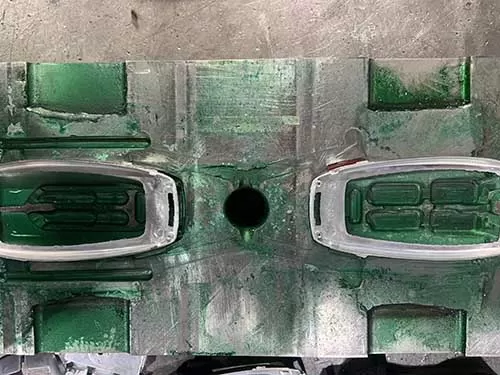
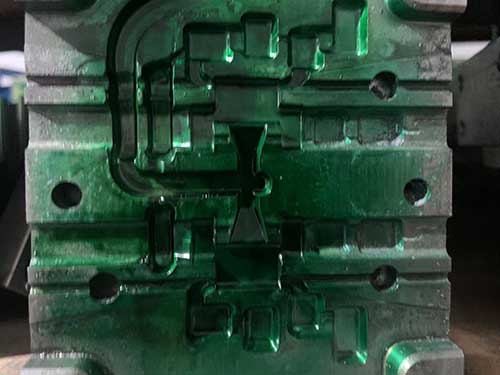
These casting dies processed in precision and quenced and enhance their durability and wear resistance, with excellent surface finish. Using them to provide high quality die casting parts in high efficiency during mass production and have a high volume production.
The Design For Casting Die & Mold
Designing for casting die & mold should ensure efficient production, good quality, and cost-effectiveness in die casting process. Since die casting process forces molten metal is injected into a mold (die), and solidify, cool and eject the shaped part from the mold. May involve several technical factors like material flow, cooling, and mold wear. Below are key points and considerations for designing for die casting.
1. Wall Thickness
Even wall thickness is crucial for avoiding these defects like shrinkage, warping, and voids. Uneven walls can cause ueven cooling, leading to casting part cold shut or warpped. Wall thickness Tolerance ranges: 1.5 mm to 5 mm (thinner walls are possible with the right design).
2. Draft Angles
Draft angles should be reasonable, which helps easy ejecting out the part from the die without damaging it. Once improper draft angles, the part may stick to the die and create defected part during ejection. We recommend that draft angles is 1° to 3° per side, which from our decades design experiences. More draft is necessary for deeper cavities.
3. Fillets and Radii
Avoiding Sharp corners when design the mold for casting parts. Designing some reasonable Fillets help ensure smooth flow of molten metal, reduce stress, and improve die life. Our engineers suggest that Minimum fillet radius from 0.5 to 1.5 mm, decided by part size and material.
4. Ribs and Bosses
Added Ribs can add strength and stiffness without significantly increasing weight. They can enhance the internal structure of the cast part only with using minimized material. Rib thickness should be 50-60% of the adjacent wall thickness. Bosses are for locking or fixing screws. Boss walls should not exceed 60-70% of the main wall thickness.
5. Undercuts and Complex Geometry
Additional sliding cores or side actions in the die, lead to increasing production complexity and cost. If undercuts are created, we should ensure the injection or casting part has a integrated structure and specific functionality.
6. Parting Line
The parting line generates with the line along which the two halves of the die close during die casting process. Minimize flashing (excess metal) and reduce material wastage is the vital point we focus on. Consistently improve and modify the mold, minimizing the crack of two halves while the die close seamly.
7. Ejection Pin Locations
Ejection pins push the cast part out from the die. Their locations should be considered carefully in the design process. Avoid these ejector pins damage the cast part, ejection pins are located in unvital area on the surface of the cast part, makes remain a good appearance and lower ejection mark on it.
8. Venting and Overflow
Designing Proper vent, extrude trapped air and gases from molten metal fills the die. Prevent defects such as porosity and incomplete fills can occur during die casting process. Designing reasonable overflow channels complete fill and smooth flow of metal, preventing air entrapment.
By following the above considerations, you can design high quality product model and precision casting dies for rapidly prototyping and mass production, reducing production challenges, lowering costs, and ensuring a high-quality end product. With mold design experience of dozen years, well-experienced engineering team design the precision casting die depends on the specific functionalities and applications.
Casting Die & Mold Manufacturing
Casting die & mold manufacturing is a complex and precise manufacturing process. It is executed by several steps, This requires specialized equipment, materials, and skilled-well technician. As one professional die casting manufacturer, we request making precision die casting molds to produce premium quality die casting components. Follow the below steps, and manufacture high quality casting die & mold.
1. Choose the Mold Material
Select high-grade tool steel or alloy steel for the mold to withstand high pressure, high temperature, and repeative wear from molten metal. Common materials include H13 steel,NAK80 steel for durability, thermal resistance and strong corrosion resistance.
2. Machining the Mold
Form the basic shape of the mold cavity using CNC milling or turning. Maybe Use EDM (Electrical Discharge Machining) or fine CNC machining for intricate features and detailed functionalities, such as detailed cavities and cores. Certainly Create channels for cooling, venting and overflow during casting.
3. Heat Treatment
Quenced the mold components to enhance hardness, wear resistance, and thermal stability. Meanwhile, You should control the die casting molds precision accuracy.
5. Polishing and Surface Finishing
Polish the mold cavity to achieve the required surface finish for casting part. Some molds maybe require having some texture and mirror effective on it. Commonly Apply surface treatments, such as nitriding or PVD coatings, to improve wear and corrosion resistance of the mold.
6. Assembly
Assemble the mold components, install the core, cavity, ejector pins, and guide pins on the mount of die casting machines. Test the fit and ensure proper alignment of the mold halves during die casting.
7. Test the Mold
Conduct a trial run on a die casting machine to test mold performance. Check for casting defects (e.g., porosity, misalignment), and make necessary adjustments until making a qualified first prototype and conform with industrial requirements. Metal casting die & mold manufacturing is over.
Conclusion
In summary, a casting die is essential manufacturing tool in rapidly prototype make and mass production. Casting die & mold manufacturing is complex process. Engineers should colloberate with tooling technician, process metal materials, form into specific configurations until have first sample trial. From design to manufacturing, we can provide professional visual moldel design and qualified final products because TangSheng Hardware Technolgy have well-experienced engineering and desigining team, advanced production equipment, can process high quality casting die & mold following the industrial standard.