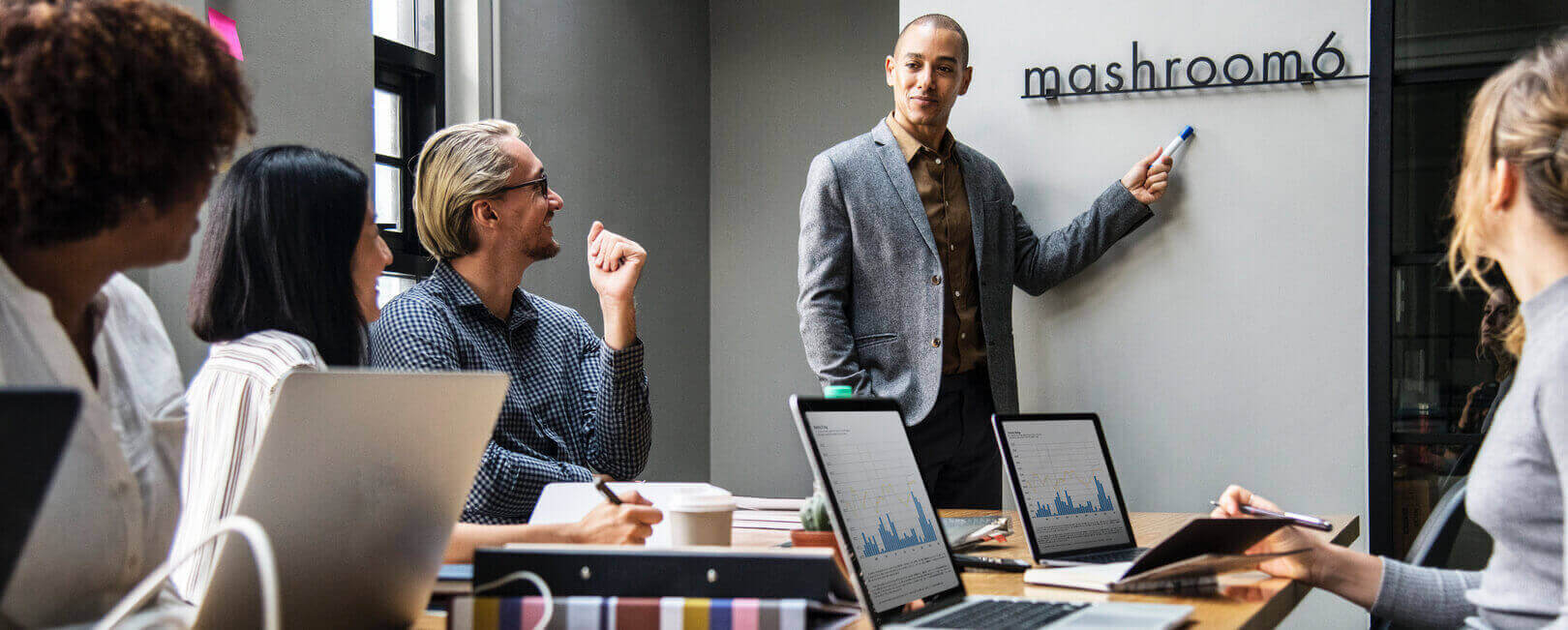
Injection Mold & Die Design And Manufacturing
Most metal casting parts and plastic parts are made by molding and die,so mold and die design and manufacturing is crucial. When a client requires developing a new style of product, The designer firstly design a 3d mold visual model and show it to client, until client got samples and had a confirmation. They may be needed of mass production, then the product should be made by mold or die. To meet client requirements, Engineers will design the mold or die. While Referring to some similar product designing experience. Our engineers will have various good solutions for designing this kind of mold or die to present our client for best choice. It’s known that Mold & die design and manufacturing is complex process, we will treat it carefully.
About Injection Mold or die design
This means that two kinds of injection mold designs,which include of plastic injection mold and metal casting die designs. Plastic injection mold design is decided by the applications and requirements of these plastic products. But metal casting die, which can process metal die casting products. Depends on different melting points metal, two types of die casting technology is used to process different metal alloys. That is Cold chamber and hot chamber die casting process.
What Is Plastic Injection Mold Design ?
Plastic injection mold design is the process of designing parts and molds for mass production of the plastic part in high efficiency. we should consider of these factors like the part’s functionality, appearance, manufacturability, and the characteristics of the plastic material . For the initial high cost of mass production, the mold that we design should keeps consistent quality in high effective mass production. The follow crucial points for plastic injection molding tools.
- Part Design
- Material Selection
- Mold Design
- Tooling Material Options
- Mold Flow Analysis
- Design for Manufacturability (DFM)
- Texture and Surface Finish
- Prototyping and Testing
- Technician skill access
What Is Casting Die Design?
Metal casting die design is the process of designing the 3d model of the part and the mold (or “die”) for casting intended metal shaped parts. It involves the product’s functionality, surface finish, strength and cast the metal part with reasonable mold. In metal die casting process, we consider of how to provide high quality products in mass production and minimize material wastage. And maitain a long term sustainable strategy for environmental protection. Metal casting dies are usually made from steel or other durable materials. They withstand repeated use under high temperatures and longer time wear.
Key Considerations for Metal Casting Die Design
Vital Points | level |
Die Structure and Components | ★★★★★ |
Thermal Management | ★★★★ |
Material Selection for the Die | ★★★★ |
Die Design for Manufacturability | ★★★ |
Tolerances and Dimensional Accuracy | ★★★★ |
Prototyping and Simulation | ★★★ |
Ejection and Post-Processing | ★★★★ |
Molds & Dies Manufacturing
Plastic injection molding die and metal casting die manufacturing are essential processes for providing plenty of industrial and daily products. They are all cast commonly by the mold or die. The quality of these molds or dies directly decide the precision, efficiency, and cost-effectiveness in the manufacturing process. Whenever plastic injection molding dies or metal casting dies, they should all have a strict production management, quality control system and skilled technique.
Plastic Injection Molding Tools Manufacturing
The tool in plastic injection molding contains two main halves: the core and the cavity. Complying with plastic injection molding die design drawing, we manufacture the core and the cavity of the mold ,Using which can form the desired plastic shaped part when injecting molten plastic into the mold. Let us to have a detail description for manufacturing the plastic injection molding tools step by step.

1. Material Selection
We choose high-strength tool steel or hardened steel that endure the high pressure and repetitive use in mass production. In special term,we consider that other materials such as aluminum may be suitable for prototyping or short production runs. But they are not wear resistance, compare to steel and hardened steel.
2. Machining the Mold
Firstly,The mold blocks are rough cutted , and using automatic grinding machine to treat and reach standand level flat before cnc machining. According to the design drawing, the mold blocks are processed into mold parts by CNC (Computer Numerical Control) milling or turning,even to grinding. Such as shaped core and cavity, ejector pins, cooling channels, and gate system. For intricate mold parts, EDM is neccessary, it can shape various precision mold parts, like sharp corners, fine details, or complex geometries.
3. Polishing and Surface Finishing
After machining, we should improve the die surfaces so that meeting the detailed finish of the molded part. Maybe Polishing fine surfaces to a mirror finish, or textured and pattern finish.
4. Mold Assembly and Test Runs
The mold core, cavity, and other components (ejector pins, cooling channels, slides, etc.) are ready well, then they have a trial assembly. Alignment of the mold halves, whether the mold run smoothly and the part molded meet some detailed requirements. Some adjustment are made if neccessary.
5. Heat Treatment
After finishing test runs, the mold may have a heat treatment to harden the steel. The mold may be quenched, and extends its durability and wear resistance. Repeatly use of the mold become safety.
Metal Casting Die Manufacturing
The die for metal casting requests stronger than those for plastic, withstand the higher temperatures of casting different melton metal and pressures during metal die casting process. The die experience repeative use for a long term on high temperature and pressure, it can deform or degrade. So the die of metal casting manufacturing is more complex than plastic injection molding tools. Today we mainly explain them about zinc alloy and aluminum alloy casting dies.
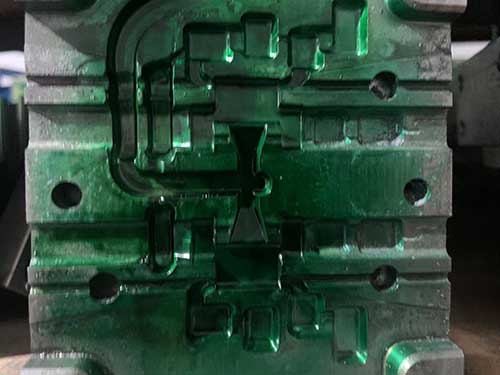
1. Material Selection
This kind of Metal casting dies are made from hardened steel or H13 tool steel or 8418,718. They have excellent heat resistance, toughness, and wear resistance. it should endure more high temperatures of molten metals like aluminum, zinc, or magnesium.
2. Machining the Die
The rough cutting mold block, should be treated and achieve a standand level flat before cnc machining. using automatic grinding machine to grind it until reach required quality standard. By CNC milling, turning, or drilling, process precisely the cavities, cores, runners, gates, and ejector systems for the casting die. So EDM is favor of intricate part shapes or small internal features for the die.
3. Heat Treatment
After machining, metal casting dies should be done heat treatment to extend hardness and wear resistance. The die can withstand thousands of casting cycles in mass production and reduce casting die maintenance and repair cost.
4. Surface Treatment
In order to enhance surface finish of die casting parts,polishing or texturing the surface of the die according to detailed requirements. Maybe coatings (like nitriding) to improve the die’s durability and resistance to thermal fatigue or erosion.To realize some texture finish of parts, on which engrave some words and pattern.
5. Assembly and Testing
The die components are assembled, alignment of the mold halves. Testing whether the die run smoothly, Adjust these components like ejector pins, cooling channels, cores, and slides, and have a process trial, and check the quality of the part is formed by die.
Plastic Injection Molding vs. Metal Casting Dies
Aspect | Plastic Injection Molding Die | Metal Casting Die |
Material | Tool steel, aluminum (for prototypes) | Hardened tool steel (e.g., H13) |
Operating Temperature | Low to medium temperatures (around 200°C) | High temperatures (up to 700°C or higher for molten metal) |
Manufacturing Process | CNC machining, EDM, polishing | CNC machining, EDM, heat treatment, surface coating |
Complexity | High for parts with undercuts, internal features | High, with added considerations for heat resistance |
Cooling System | Cooling channels for rapid cycling | Cooling channels, thermal sinks for heat management |
Common Defects | Warping, sink marks, flash | Porosity, shrinkage, thermal fatigue |
Cycle Time | Short, typically a few seconds per part | Longer, due to the need to cool molten metal |
Durability | High, but less stress from temperature | High, must withstand high thermal and mechanical stress |
The Molds & Dies Impregnation Phrase
In Mold & die design and manufacturing, whenever plastic injection molding or metal casting, they all require post-processing steps like impregnation and modifications. To enhance the formed part’s quality and performance. These dies should face the challenge of impregnation and modification during primary phrase in mass production.
Impregnation, which is a must pass phrase in beginning mass production. It involves filling microscopic pores or cracks in the material to improve its structural integrity. The improvement issue can prevent leaks, or increase its resistance to pressure or fluids. Used more in metal casting than plastic injection molding.
Impregnation in Plastic Injection Molding
When impregnation can be used, by adpoting resin impregnation to improve resistance to stress or wear. In some applications, Employing hermetic sealing (e.g., electronics housings), impregnation can prevent fluid or gas leaks.
Impregnation in Metal Casting
In metal casting, Impregnation is often used to fill the pores. and voids the porous of metal material occurred during the cooling and solidification process of formed parts,like engine parts, pumps, valves in automotive industry. So the impregnation can improves leak resistance in cast parts. And can fill the pores and reduce the defect of metal die casting and
Conclusion
Mold & die design and manufacturing involves detailed design, precision manufacturing. Plastic injection molding tools focus on forming high quality plastic part in each fast cycle under lower temperatures. Metal casting dies, which needs endure high temperatures and pressures. And need more complex design and manufacturing process.