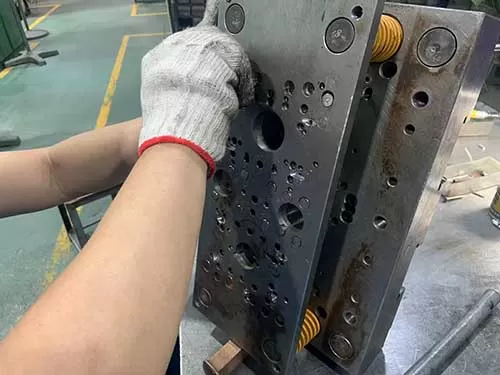
After Plastic injection molding tools have been used for some time, there are some problems on products and molding tools. Maybe injected plastic parts deformed , or these molding tools can’t be used smoothly. At this time, these molding tools should be modified or repaired. Optimizing Plastic Injection Molding Tools for High Efficiency: Maintenance and Repair should be done. So Plastic Injection Molding Tools Maintenance And Repair is indispensable part after the plastic mold have been used for a long time. Rather than zinc casting die mainenance and repair.
- Regular Inspection and Monitoring
- Preventive Maintenance
- Repair and Refurbishment Strategies
Regular Inspection and Monitoring
Maintaining plastic injection molding tools should have a regular inspection. When the plastic injection molding tools are used for a long time, some potential problem happened, such as the mold must be weared off, the cavity stick the plastic part, injected plastic part warp. When the mold is inspected during a break down, the following key points is considered available.
Key Points | Inspection Method |
---|---|
Surface Wear Inspection | Look for any scratches, indentations, or surface corrosion and residues on the mold’s cavity or core. These defects can affect the quality of the final product. |
Check Parting Line | Inspect the parting line to ensure it is the best optimized partline without impact appearance. Excess flash on the part line is dicovered, the mold should be repaired until minimizing the flash. |
Test Vents and Ejector Pins | Vents are clear to avoid pressure buildup. Ejector pins should be alignment with the opening mold, are functioning smoothly when injection molding proceeds. |
Check Cooling Channels | Check the cooling channels, as clogged channels can cause uneven cooling and lead to the part wrapped. Keep cooling channels on the mold are smooth and provide even cooling throughout on the suface of the plastic injected part. |
Preventive Maintenance
Preventive maintenance means that people implement some preventive methods to avoid some predictable troubles depends on their enrich work experience. Depends on the tool’s usage frequency, material type, and operating conditions, we found some defects of the mold and adopt preventive methods to troubleshoot the problems. The follow are detail steps for the maintenance task.
Lubrication measure
Regularly lubricate moving parts, such as ejector systems and slides. It avoids excessive wear of the mold and ensure smooth operation in die casting process.
Regular Cleaning the mold
Keep the mold cavity and core clean, with no any residual plastic or debris on it after each injection cycle. Once any residues can cause defects in the final part and lead to mold damage and imperfect injection part. In further impact the mold life time and plastic part quality.
Uniform Temperature Control
Monitor and maintain consistent mold temperatures during production, because uneven temperature on the mold can cause the part wrapped and shrankage. So keeping uniform temperature can produce a smooth molten plastic flow. And fully filling with plastic molten flow into the mold, improving plastic part quality and extending mold life.
Polishing and Coating
Regular polishing the mold surfaces, and maintain their smoothness and remove any debris deposited on the surface of the mold, prolong the mold life time and durability. Sometimes we will apply specialized coatings such as hard chrome plating or PVD (Physical Vapor Deposition) coatings to enhance wear resistance and corrosion resistance of the mold.
Repair and Refurbishment Strategies
No matter how well-maintained a mold is, it always require repair due to natural wear and tear. However, prompt and precise repairs can significantly extend the tool’s lifespan and ensure high quality of part. From the below several key issues to start.
Damage Assessment
When large defects parts appears in mass production, we may consider of mold damage, a thorough assessment should be conducted. We use precision measurement devices or non-destructive testing (NDT) methods like ultrasonic or dye penetrant testing to detect the core and cavities of the mold. Troubleshooting the problem of mold damage.
Welding Repairs
For minor cracks or surface damage, welding is a common repair technique. If neccessory Our skill-well technicians can use laser welding or TIG (Tungsten Inert Gas) welding to repair the damaged areas. After welding, re-machining or re-polishing may be necessary until the mold recovered completely.
Component Replacement
After the mold has been used for a long time, some worn or damaged components such as ejector pins, guide bushings, or springs can be replaced by new ones. Resore the mold run smoothly and quickly, alignment and close and open action and minimizing production downtime.
Refurbishment
In cases these wore components have degraded the mold’s performance, a full refurbishment procedure is started. This involves of disassembling the mold, inspecting all components, and repairing or replacing parts, the mold is then reassembled, re-polished, and tested until it can make qualified standard products.
Tracking Mold Usage and Performance
Building a mold maintenance log or software system to track mold usage and performance. By using The effective way, and ensure timely maintenance and repairs. It includes the follow points.
Cycle Count
Monitoring the number of cycles (injections) the mold, and recorded by the computer system. Depends on these cycle counts, can predict mold maintanence time. Some molds may require maintenance at interval few thousand cycles.
Defect Rate
Tracking the number of defective parts produced by a mold, can highlight the mold performance and the reasons of defect parts . Also assess the value of the mold in mass production and loss and profit of enterprise.
Conclusion
In conclusion, proper plastic injection molding tools maintenance and repair is essential to achieving high efficiency and minimizing costly downtime. While conducting regular inspections, preventive maintenance, prompt repairs, and accurate tracking of mold performance. Use planned strategies to extend the life of molds and maintain product quality. By adopting these practices, manufacturers can ensure that their plastic injection molds operate at peak performance, reducing costs and enhancing overall productivity.