Technician is all known that plastic injected objects always carry some burr and nozzle redundant material when the plastic part is formed by molding tool or die under high temperature and pressure. These imperfection burr and redundant nozzle material should be removed. People are customized to calling: “PiFeng” in Chinese. So the process is Plastic parts deburring process.
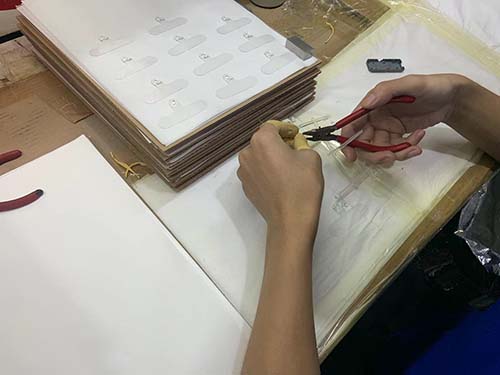
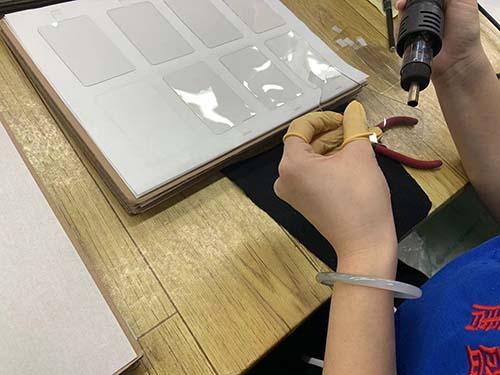
What is plastic parts deburring?
Plastic Parts Deburring is the process of removing small imperfections, sharp edges on the plastic parts, or burrs that are left on parts after injection. It makes the final product smooth, safe to handle, and aesthetically pleasing and smooth to installment. Compare to metal die casting part deburring process, it is more mild.
Which are Methods for Plastic Parts Deburring
1. Manual Deburring (Hand Tools)
In general term, workers use hand tools like knives, scrapers, or abrasive pads to remove burrs manually. Simple, cost-effective for small batches, and require the requirement of appeal appearance. But time-consuming and not suitable for large-scale production.
2. Mechanical Deburring (Tumbling/Vibratory Finishing)
The plastic parts are placed in a vibratory or tumbling machine that contains abrasive media. As the machine vibrates or rotates, the abrasive media polishes the surfaces of the parts, removing burrs in the process. It is suitable for bulk processing, highly efficient for a high volume production.
3. Thermal Deburring (Deflashing)
The heat burns off or vaporizes the burrs on the part without unaffect its functionality. This kind of deburring process is simple and rude. It is effective for removing small burrs and flash on the part. The process is high cost, and only suitable for specific types of plastics.
4. Cryogenic Deburring
The parts are cooled using liquid nitrogen to make the plastic brittle, and then blasted with a media like plastic beads or other abrasive material. The specific treatmemt is highly effective for plastics, particularly for soft or elastomeric materials. It is suitable typically for complex shapes and internal features. It is expensive due to the cost of liquid nitrogen and equipment. So it is not suitable for all types of plastics.
5. Ultrasonic Deburring
Uses high-frequency vibrating abrasive liquid to gently remove burrs from the part surface. It is excellent for fragile parts and complex geometries. Not suitable for large burrs.
6. Laser Deburring
Use a laser beam melting or vaporizing the burrs without damaging the base material. It’s highly precise through computer systems. Focus on high precision and difficult-to-reach areas, with no physical contact. But it is expensive and requires specialized equipment.
7. Chemical Deburring
Submerging the plastic part in a chemical solution, and dissolves the burrs on the plastic part. The chemical reaction removes excess material on the part. The special process is suitable for large quantities and delicate or intricate parts. Needs careful handling of chemicals solution and appropriate disposal.
Factors to Consider When Choosing a Deburring Method
- Type of Plastic: Certain methods (like thermal or chemical deburring) are suitable only for specific plastic types that can withstand heat or chemicals without degrading and damage the plastic part.
- Part Geometry:Some small plastic part with complex shapes have some hard-to-reach areas, they is more suitable for processes like cryogenic or ultrasonic deburring.
- Part Quantity: For small batches, manual or mechanical deburring might be sufficient. If mass production, these processes like thermal or cryogenic are more efficient.
- Cost: Some methods like laser or cryogenic deburring can be expensive. So the scale of production should justify the cost.
- Tolerances and Surface Finish: Some processes, like mechanical tumbling, may affect the surface finish or tight tolerances of the part. Choose the best deburring method can ensure the high quality and accurate dimensions of part.
Conclusion
In summary, plastic parts deburring process in production to ensure the quality, safety, and functionality of the final product. The right deburring method depends on factors such as part complexity, material type, production volume, and cost considerations.We should adpot the reasonable deburring mothod to treat these plastic parts to meet the demand of market and requirement detailed of client.