In order to improving aesthetics and extending durability of plastic parts, people have a good idea that coating another material layer on these original surface and make the appearance of the plastic parts look like is perfect and beautiful or others practical applications. Plastic parts coating process is also often used for improving aesthetics and extending durability of plastic parts. Compare to metal casting parts coating processes, it is different a little. Today We have a general introduction for plastic parts coating processes.
What Is The Plastic Part Coating ?
The plastic part coating means using a layer of material onto the surface of the plastic part, typically to protect it from corrosion, enhance its durability, improve aesthetics, or provide other functionalities . There are several methods for applying material coatings, To different types of material, the part being coated. Below are the most common plastic part coating processes.
1. Dip Coating
In the dip coating process, the object is dipped into a vat of liquid plastic or polymer solution. Some plastic or polymer ions transfer to the surface of substrate, the coating is cured or solidified, then evaporation. Dip coating is finished. Plastisol (PVC), polyethylene, epoxy, or acrylic as coating material is used for the process. The plastic parts can be coated by dipping. Execute the follow steps one by one.
- The substrate is preheated to help the plastic adhere better.
- dipping the substrate into the plastic solution.
- After dipping, the object is cooled, form hard plastic layer on the surface of the plastic part.
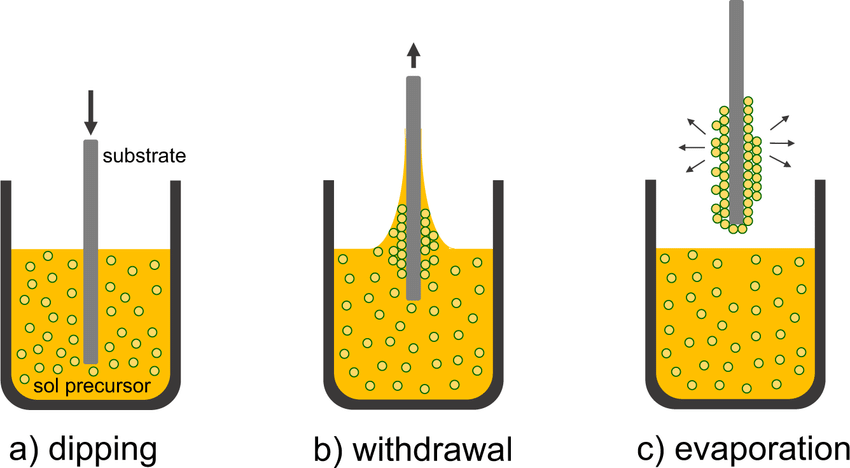
2. Powder Coating
Powder coating means spraying a powdered plastic or polymer onto an object and then heating the object to melt and cure the plastic into a uniform layer on the surface of the part. Like the polyethylene, nylon, epoxy, polyester, and polyurethane are often widely used for the process.
- Electrostatically charged, and spraying powder particles (which are also charged) onto the surface of the parts.
- Place them into an oven and heating and melts the powder, forming a smooth, even layer.
- The melted plastic is cured to create a durable protective film on the surface of plastic part.
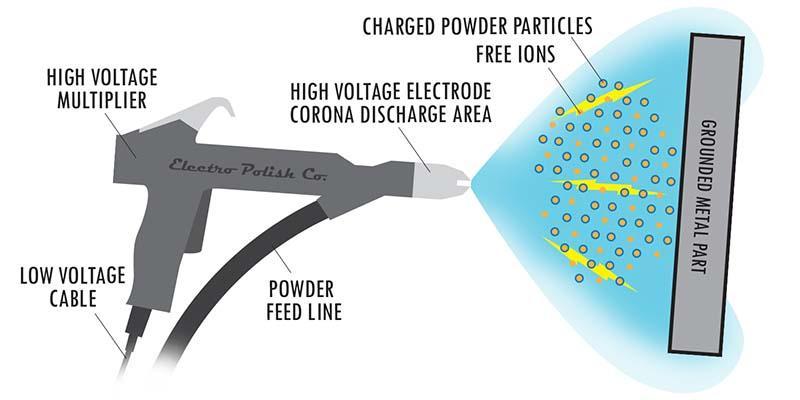
3. Fluidized Bed Coating
An object is preheated and dipped into a bed of fluidized plastic powder. Heated object melts fluidized plastic powder, and forms a coating layer on the surface of the object. Commonly Polyethylene, PVC, PTFE (Teflon), or nylon, which is used as coating material.
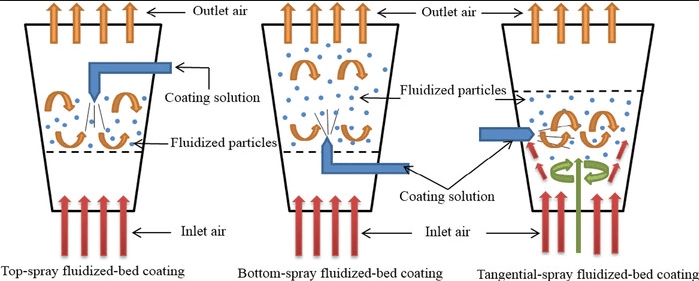
4. Physical Vapor Deposition (PVD)
This is the vaporization of material in a vacuum, which then condenses on the plastic surface, forming a thin coating layer. The process is beneficial for wear resistance, aesthetic finishes, and reflective surfaces of the plastic parts, It is high-quality, thin, and durable coatings.
5.Chemical Vapor Deposition (CVD)
A process is chemicals react,in which the coating layer is formed , and deposit on the surace of the part. It is utilized in Semiconductor industries, wear-resistant coatings. It can create uniform coatings with excellent adhesion and material properties.
6.UV Coating And Flame Spraying
UV-curable coating is applied to plastic parts’ surfaces, and then cured using ultraviolet light. Optical lenses, electronics, automotive interiors are coated in this way. Fast curing, enhancing scratch resistance of the plastic parts.
7.Hot Stamping
Using a heated die to press a coating (like foil or pigment) onto the surface of a plastic part. It can stamp Logos, labels, decorative finishes on consumer goods. Form creative sharp, clean designs with metallic or glossy finishes.
8. Electrostatic Coating
This process means spraying plastic particles onto an electrically charged object. The electrostatic attraction makes the particles stick to the object uniformly before the plastic is cured.
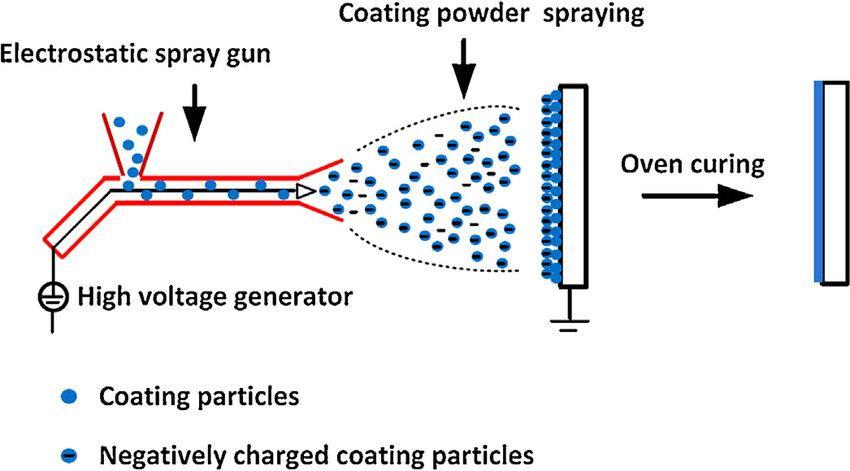
Conclusion
In Summary, Plastic parts coating process is widely used in industries like automotive, electronics, consumer goods, and construction. It can offer corrosion resistance, aesthetic enhancement and decorative advantages and other functionalities. The above each of processes can be selected based on the specific requirements of the plastic part in terms of durability, aesthetics, or functionality. They also provide more benefits to our society progress and industry creation.