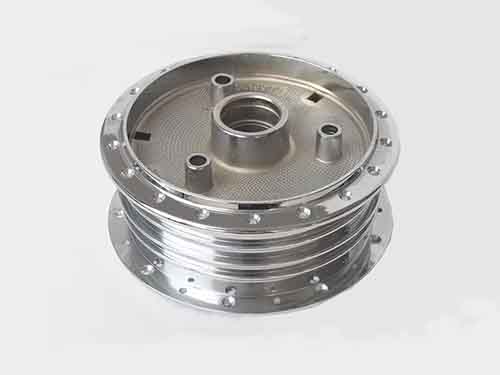
Aluminum Die Casting Part Plating
When aluminum die casting components are used largely, In order to extend these parts’ life span and durabilty in applications. It may have a good surface finish and better withstand corrosion and moisture environments in some hash weather. People thought of The special method, which is coating a layer of tiny light raw metal material on the surface of these aluminum die casting components by the principle of electrode, and achieve prolonging the part life span and enhance its durability. The pross is commonly called as plating on aluminum die castings.
What is plating on aluminum die castings ?
Plating on aluminum die casting means that applying a metal coating to cover the surface of aluminum die-cast components. This coating enhances the the part durability and other functionalities. such as improving its aesthetics, corrosion resistance, wear resistance, electrical conductivity.. Common plating materials include nickel, chrome, copper, and zinc.
Plating Process on Aluminum Die Castings Guide
Aluminum die castings plating process is a tedius process, and need of more steps, compare to zinc die castings plating one, its plating cost is higher. Because many pre-treatment processes should be done and ensure the aluminum diee castings plating durability and longer life span. To meet some specific functional requirements of aluminum die castings, these parts should be plated. Its plating process is the below information.
- Cleaning and Degreasing: Cleaning and removing oils, grease, and impurities from manufacturing on the surface of aluminum die castings
- Etching the oxide layer: Etching off the natural oxide layer deposited on the surface of parts, and roughens the surface for better adhesion.
- Pre-Treatment: By zincate process, depositing a thin zinc layer on the surface of parts, which enhances adhesion between the aluminum and subsequent plating layers.
- Copper/Nickel Strike Layer: Covering a thin layer of copper or nickel on the zinc layer of the part. This layer provides a strong bond between the aluminum substrate and the final plating material.
- Plating: The final desired metal layer, depends on specific requirements and functionalities of the parts, nickel, workers require plating chrome, or another material onto the part. The thickness and type of metal depend on the application requirements.
- Post-Treatment: Reinforce the plating layer durability, another steps, such as passivation, polishing, or additional coatings process available.
Advantages and Benefits of Plating On Aluminum Die Castings
- Improved Corrosion Resistance: Protects the aluminum part from harsh environment.
- Decoration Appearance: Provides an aesthetic appeal, decorative effection.
- Increased Durability and Prolonging lifespan: Ehance wear and tear to resist, prolong the part’s lifespan.
- Functional Properties: enhance electrical conductivity where needed.
In summary, plating aluminum die-cast parts requires specific technique in surface preparation and process control to achieve a high-quality, durable finish.The surface finish method enhances the properties of durability and corrosion resistance of aluminum die castings and enables these parts to use more industrical fields and specific environments.
The Difference Between Plating On Aluminum Die Castings And Zinc Die Castings
Plating on aluminum die castings and plating on zinc die castings involve similar principles but differ significant process steps. Let us explain The Difference Between Plating Aluminum Die Castings And Plating Zinc Die Castings with the table.
Operation Steps | Aluminum Die Castings Plating | Zinc Die Castings Plating |
---|---|---|
Surface Preparation | Removing a thicker and stable oxide layer on aluminum part before plating. Zincate process means depositing a thin layer of zinc, which improves adhesion for plating layers. | A thinner and less stable oxide layer form on the zinc part, which is removed by the cleaning process often involves light acid etching or alkaline cleaning. |
Adhesion Challenges | Adhesion is more challenging due to the material’s inherent oxidation and porosity. Pre-treatments, making strike layers are crucial for ehance adhesion for plating. | Zinc material is as a strong adhesion for plating.Direct plating is possible in many cases, though a copper strike enhance adhesion for complex applications. |
Material Porosity | Aluminum is more porous, which can trap contaminants and gases, leading to plating defects like blistering or peeling. Zincate process makes vacuum impregnation before plating. | Zinc alloys are generally less porous, and have the fine seal surface. This reduces the risk of plating defects and eliminating the need for vacuum impregnation in most cases. |
Coating Types and Applications | Typically plated with nickel, chrome, or other metals to enhance appearance, corrosion resistance, or conductivity. Commonly they are weightlight and used in aerospace, automotive, and electronics. | Often plated with chrome, nickel, or copper for both functional and decorative purposes.Widely used in automotive parts, consumer goods, and communication devices. |
Cost and Efficiency | More expensive due to additional pre-treatment steps and material challenges.Longer process times and more higher overall cost of final prorducts | Generally more economical and faster to plate due to simpler surface preparation and less porosity material. It is almost half of overall cost of aluminum die castings one. |