As a professional custom die casting factory, offering comprehensive custom die casting services is essential to meet the diverse needs of clients.It includes custom design, such as designing 3d model in accordance with induvidual personalized and custom requirements in applications and functionalities. Then according to the model of product, design the mold or die for producing the product and manufacturing die. After fast prototype and testing the die, introducing advanced die casting machines and automatic production line to finish mass production in high effective. Track Client experiences and feedbacks, provide consideration after-sales services. In this article, we will explore custom die casting services and outline the steps your factory should take to excel in this competitive field.
Custom Product Design And Manufacturing Die
Custom Product Design
When Accept the picture and innovative conception from client, Our engineers and designer will communicate with them in detail, undersand their thought and ideas fully. With enrich work experience and practice of decades in product design, Our skilled-weel engineers can raise some feasible suggests to the client and present some successful business cases to client until agreement is reached between engineers and client. Then we begin to design the 3d mold for product and pass several modifications. At last, achieve the requirement of the client. And the 3d Model of the procuct is finished.
Mold Design
Mold design, which involves collaborating with clients to understand their specific needs and create a functional mold design. Advanced CAD software is typically employed to create 3D models of the molds,according to the designed 3d model of product. And Though visual die casting process simulation on the computer, and improve and modify consistently mold design.
Prototyping
Once the mold design is finalized, prototyping will be test the feasibility and functionality of the design. This designed prototype is formed using 3D printing machine and check its apperance, dimensions and applications and functionalities. Prototyping helps identify any potential defeats in the design and allows for adjustments of the mold design.
Material Selection
Choosing the right material is crucial for ensure high quality of casting parts and specific functional applications. Common materials used in die casting include aluminum, zinc, magnesium, and copper alloys. Each material has unique characteristics, such as strength, weight, corrosion resistance, and thermal conductivity. In accordance with the specific functional requirements, we will select the appropriate metal material to cast the components that client needs.
Mold & Die Manufacturing
After finalizing the mold design and material selection, the next step is die manufacturing. This process involves precision mold components, Especially the cavity and core of the mold. Most of casting dies are made of high-quality steel or aluminum, they can withstand wear resistance, longevity and repeative usage. The manufacturing process may include CNC machining, electrical discharge machining (EDM), and heat treatment to enhance the die’s performance.
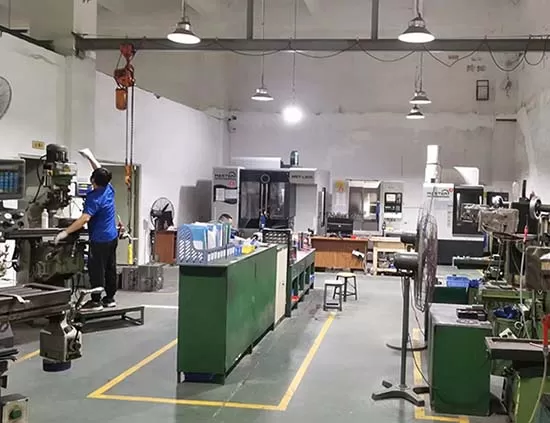
Casting die Parts Production Services
Once the dies are manufactured, and test die casting process and confirm the first sample, the mass die casting production can commence. Fllow the below key steps to finish the rough die casting components.
Melting The selected Metal Alloy
The selected metal alloy is melted in a furnace until it reaches the appropriate temperature for casting. This step requires careful temperature control to ensure the metal is fully molten and filter impurities inside it, and keep purified metal alloy molten material for a good prepairation for casting process.
Injection
The molten metal is injected into the preheated mold under high pressure, allowing it to fill the cavity quickly and completely. This process can be done using different techniques, including hot chamber and cold chamber die casting, depending on the material used. Zinc alloys is suitable for hot chamber die casting, Other metal alloys is for cold chamber die casting.
Cooling
After the mold is filled, the metal shaped part will be cooled and solidified. The cooling time depends on the material, part thickness, and mold design. The detailed areas of the casting part should gain even uniformly cooling temperatures, and avoid the warping and shrankage of the part because of shut down or uneven cooling temperature.
Ejection
Once cooled, the die can be opened, and the cast part is ejected from the die. To ensure the cast part is seperated from the mold smoothly and without any block and stick to the mold, we design the proper draft angles on the surface of the part.
Post-Casting Operations
To ensure the quality and functionality of the final product, several post-casting operations may be necessary:
Finishing processes such as sanding, machining, or polishing are often required to achieve the desired surface finish and dimensional accuracy. This step can also involve deburring, which removes sharp edges or imperfections from the cast part. Then to enhance the durability and other functional applications of cast part, we employ different coating methods to finish the functional final product. Like Plating , powder coating, painting and vanishing.
Inspection and Quality Control
Quality control is a critical aspect of custom die casting services. Implementing rigorous inspection protocols helps filtering defect products and ensure that each component meets the required specifications. By appplying techniques such as X-ray inspection, ultrasonic testing, and visual inspections, we can assess the integrity of the cast parts.
Assembly and Packaging
In many cases, clients may require assembly services for multi-part products. Our factory can offer assembly solutions, including inserting additional components, fastening, and packaging for shipment. All qualified cast parts delivered to the sythetics department to assembly and test until a final product package. Proper packaging is essential to protect the parts during transport and delivery.
Track Client Services
Attention of Client Experience
Frequently email and call to the client, and consult about the products application experience, and keep a friendly communication with the client, and maintain a long term friendly relationship with them.
Providing Technical Expertise
Offering technical expertise surpporting is crucial in guiding clients through the custom die casting process. Also Providing insights on material selection, design optimization, and production methods can help clients to realize their application functions of the casting parts at actual applications.
Continuous Feedback
we encourage continuous feedback from clients throughout the production process fosters trust and collaboration. This can involve regular updates on production status, product functional improvement and product design detail adjustment.
Investing in Technology and Innovation
To remain competitive in the custom die casting industry,we invest advanced technologies and innovative conception into our die casting process. This can include:
Automation: Integrating automation into the die casting process increase production rate and reduce production costs. However automated systems for material feeding, quality inspection, and robotic hands handling can optimize streamline operations and minimize human error.
Advanced Manufacturing Techniques: Exploring advanced manufacturing techniques, such as additive manufacturing for prototypes or hybrid casting methods. This can improve our factory’s capabilities and broaden the range of services offered, provide more custom die casting projects that being satisfied with the needs specifications.
Research and Development: Investing in research and development allows us to follow industry trends and emerging technologies, to develop new alloys, improving mold designs, or refining production processes to create higher-quality products and increased customer satisfaction.
Conclusion
Custom die casting services means a wide range of offerings, from design and prototyping to material selection, production, and post-casting operations. As a professional custom die casting factory, focusing on high quality,lead time and technological innovation for success in this competitive industry. By understanding the specific requirements of the custom die casting process, and continually adapting to meet client needs. This will make us become a trusted partner in delivering high-quality, precision-engineered components.