With the development of industry and society, Metal die casting industry have spread in many fields. Especially Zinc die casting process , as a new creative industry, gains rapid growth. But also The advantages of zinc die casting comparison to other metal ones, like aluminum, copper, iron, and stainless steel die casting. Here’s a breakdown of the unique benefits of zinc die casting, with examples highlighting its application across industries.
The Advantages of Zinc Alloys, Comparison To Other Metal Alloys
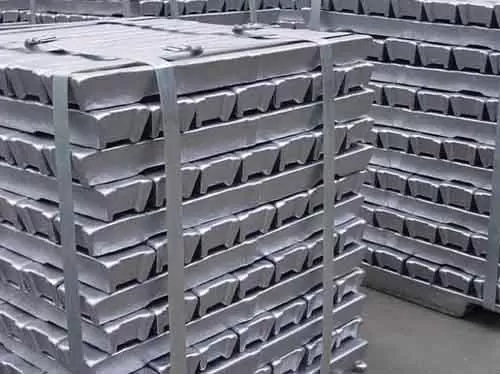
Superior Ductility and Thin-Wall Casting
Zinc’s specific ductility allows it to be cast into complex shapes with thin walls. But not feasible for other metals like iron or stainless steel. Zinc die casting is also ideal for intricate and lightweight designs of small and medium sizes. Especially in electronics and telecommunications, thin-walled enclosures for smartphones and tablets and smart devices, shielding against electromagnetic interference (EMI). With it, may create some wearable device enclosures which fit ergonomics design.
Strong Strength and Durability
Zinc alloys are strong strenght and can withstand high impacts and wear, making them suitable for durable components . Like Zamak, provide a significant features of castability and durability. Such as automotive door handles and locks. They withstand frequent use and wear. While being lighter than iron, steel and less prone to corrosion than copper. So zinc alloys have high corrosion resistance and more durable than other metal alloys.
Corrosion Resistance and Surface Finishing Versatility
Zinc die cast parts have excellent corrosion resistance, stronger than forming aluminum and steel due to zinc alloys unique metal properties. Additionally, zinc’s fine surface allows for a variety of finishes, from chrome plating to painting is easier than alumium alloy casting ones. Becasue zinc metal is a kind of great adhesive metal with substrate metal material in Plating. Such as in kitchenware and household appliances, zinc die-cast knobs, handles, and trim benefit from the corrosion resistance and attractive finish options.
Lower Melting Points
Its low melting point (around 420°C) can have energy savings in melting, fast and lower cost, compared to aluminum or stainless steel, which require higher temperatures. The molten zinc can solidify within a few seconds and finish one cast cycle, form a cast part, far beyond the other metal casting, such as aluminum, copper, iron and steel, which require more longer time to solidify for each cast cycle.
Recycling and Environmental Friendliness
Zinc is a fully recyclable material with low environmental contamination. Recycled zinc still keep its properties, contributing to sustainable production and reuse. In the automotive sector, Many zinc die casting components that can be fully recycled, follows circular economy initiatives and meeting industry sustainability goals.
Dimensional Accuracy and Stability
Zinc die cast parts have a precise dimensions and stability due to its small shrankage when cooling and solidifying. Zinc parts retain their size and fit. Unlike aluminum, which can experience dimensional changes due to bigger shrankage when the part experiences a big gap between high and low temperature. In medical devices, where precision is critical for housings and supports. Zinc die casting components just fit within the device to ensure safety and functionality.
Advantages Of Zinc Die Casting Process, Comarison To Other Metals One
Hot chamber die casting is well-suited for processing zinc (or zinc alloy) parts because zinc has a relatively low melting point. The process offers rapid cycling and hig volume production. These desired designed zinc die casting components have been used in a large scale in our every corner in daily life, and durable and cost-efficiency. This is Advantages of Processing zinc die casting parts with hot chamber die casting machine.
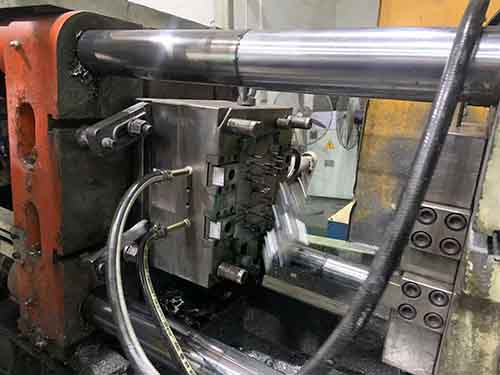
1. Lower Melting Points Furnace and Unique Injection System
The hot chamber die casting machine has a pool of molten zinc alloy directly connected to the casting chamber. Zinc’s low melting temperature (around 420°C). This keeps the stable temperature the melting source. Through Gooseneck mechanism, directly injecting the molten zinc into the die, not like aluminum alloy casting, and require to ladle out from the saperated melting pool, and fall into the injection hopper.
2. Fast Cast Cycle And Less Mold Maintenance And Repair
The high-pressure piston force molten zinc into the die cavity at speeds. Melton Zinc can cool and solidifity quickly, the die to be opened after just a few seconds. the cast part ejected from the die. This fast cast cycle time due to the zinc alloy low melting points, which require less heat dissipation than other metal such as aluminum or iron, require more cooling time. The casting die receive wears and impacts times at lower temperature extend its life, reduce mold maintenance and repair.
3. Cost-Effective Mass Production
Lower energy consumption, fast cast cycle, automatic production line and rigid quality management regulations will ensure high quality of zinc die casting parts and mass production cost-effective. Especially automotive components mass production, our factory follows strictly IATF16949 quality standard, and produce high quality automotive parts in high efficiency.
4. Create Fine surface Finishing, Minimizes Post-Process
We choose high precision tooling steel casting die and advanced die casting machine with computer numerical control system to process tight tolerance dimensional cast part. And eusure that each cast part generates fine surface finishing, aim to minimzing post-process. Especially some small size of metal parts for automotive components,such as sensor sheilding and electronic connectors.
5. Ensure Tight tolerance Dimensions Of Small and Medium Size Part
Zinc alloys are typically suitable for small and medium size cast parts. The casting die core and cavity requres more smaller tooling steel block, compared to the one for large size cast part. But its design is very precise, and ensure the tight tolerance dimensions of zinc die casting part. And integrated instructure of part is strength enough, durable and portable.