Aluminum Die Casting is comparative common metal process technique in morden industrial manufacturing. By high precision die, in the term of high temperature and high temperature, cast the molten aluminum alloy into the intended functional and practical components, and meet the demand of different setors in various industries. So die casting manufacturers are known that they should improve consistently mass production rate and strengthen the quality control, and provide more high quality aluminum die casting parts. So Top tips For Reducing The defective Parts During Aluminum Die Casting Process, help suppliers realize their aims smoothly.
Common Defects And Good Solution
People found that there are the follow several common defects happens during aluminum die casting. To control the quality of the cast part and maintain a consistent mass prorduction in high efficiency, technician start from the below aspects to improve casting operation and ensure produce high quality aluminum die casting parts.
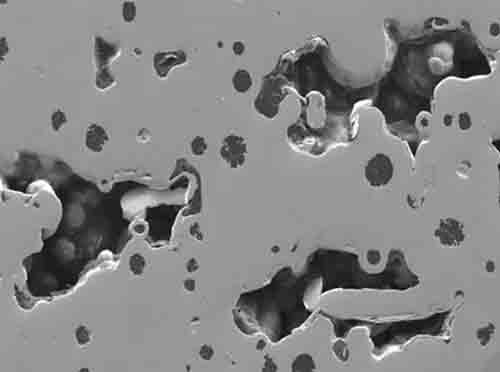
Porosity Defect

Cold Shut Defect
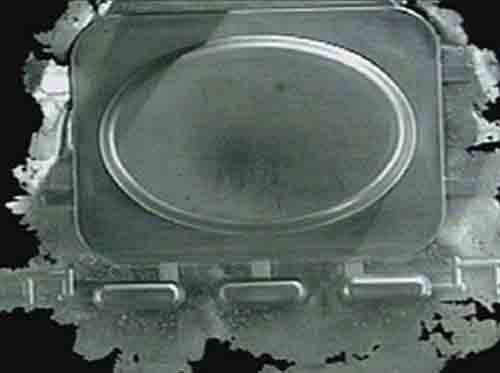
Excess Flash Defect
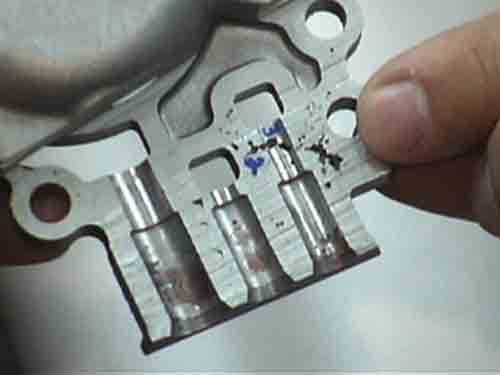
Shrinkage Defect
Defect types | Possible Cause | Solution |
---|---|---|
Porosity | Most Common defect, may be caused by gas entrapment, poor degassing, lead to an unstable part structure. | Improve venting channels, vacuum casting is best. |
Cold Shut | Low metal temp, slow injection, not fill the die fully before the molten aluminum solidification, ununiform cooling, lead cold shut and hot short. | Increase temp, adjust shot speed, ensure the molten alloy fills the die fully before solidification. |
Flash | Since excessive pressure, mold wear, more flash generates on the partline of the cast part. | Reduce clamping force and injection pressure, meanwhile, the wear die repolished and machined, ensure the die close seamlessly. |
Shrinkage | Uneven cooling, leads to the cast part wrapped and disformed, | Optimize cooling channels, the cast part surface can have an even cooling when it start solidifying. |
Top Tips For Reducing The defective Parts
To reducing the defective aluminum die casting parts during aluminum die casting process, and ensure offering more high quality cast parts, Die casting manufacturers should focus on the troubles in the casting process, Anylisis various parameters from die casting, involves of the casting die structure design and post-process operations. Continueously improve parameters of the die casting and minimizing post-process operations, reduces the defective aluminum die casting parts. Top Tips For Reducing The defective Partsmainly starts from the below aspects, enhance the quality of aluminum die casting parts. It is similar to Good Solutions For Improving Zinc Alloy Casting Part Warping Or Shrinkage.
Optimize Casting Parameters
- Control Injection Shot: Adjust the parameters of molten metal injection, ensure the molten metal fill the die fully before solidification. and gain an uniform cooling when the molten aluminum alloy start solidify.
- Adjust Inection Pressure: Get Injection pressure (500–1,500 bar) based on part geometry, and complete gain a fine surface and extrude trapped gas and reduces porosity.
- Use Die Lubrication: The release agent is sprayed on the core and cavity of the die when the cast part is sperated from the die, and avoid stick the die and ensure a good flow.
Optimize Mold Design & Maintenance
- Improve venting setting: Design approperiate venting channel, and extrude the trapped gas inside molten aluminum alloy, reducing prosity of cast part.
- Design reasonable draft angles: The reasonable draft angles for ejection helps the cast part separate from the die, and prevent stick the die and any wrapping from overheavy weight ejection power.
- Improvement of Cooling Channels: The cast part may produces deformation due to the big shrankage under ununiform cooling on the surface of it, improving cooling channels makes the cast part cooled uniformly.
- Regular Maintenance: After some time for die casting machine and dies, we should have a breakdown, keep a regular maintenance, check the wearness and misalignment of the die and the prameters of die casting machine, and ensures the process can produce in high efficiency mass products.
Control Melting & Metal Quality
- Select High Quality Aluminum Alloys: Depends on the applications and functions of the cast part, select high quality aluminum alloy, avoid worse part structure from Zn, Fe impurity.
- Degassing Method: Inser high pressure Nitrogen to remove hydrogen inside the molten aluminum alloy, and reducing porosity.
- Temperature Control: Depends on well-experience die casting, maitain the range from 650 to750°C, prevent the risk of cold shut and hot tear when cooling the cast part.
Process Monitoring & Automation
- Install Real-Time Sensor: Install some real-time sensor on the key operation positions, collect the key data, and as a powerful accessment.
- Strengthen Automation of The Casting Process: Automatic production line can reduce some errors caused by labor operaation, and ensure the steady of mass production and consistent quality casting part.
- The Advanced Inspection Equipment: X-Ray/CT Scanning is introduced, inspect internal defects in critical parts.
Post-Casting Best Practices
- Trimming and Deburring: As most common post-process, which is indispenable part in die casting factory. For the burrs and flashes on the surface of as-cast part, works should remove the burrs and flashes on the part.
- Heat Treatment: To improve the mechanical features of the cast part, in accordance with the requirements of the client, they may be done heat treatment, aim to the client application standard.
- Strict Quality Control: Every process of die casting process should conduct strict quality control, not exception of post-casting practices. Inspector should check all cast part so that ensure the mass product high quality.
Training & Documentation
- Operator Training: Management Clerks should a regular operator training, and depends on the status of mass production, make controlable operation documents and release operation regulations.
- Root Cause Analysis: If the problem is resolved completely, we should track the root cause the defective part, and analysis deeply the reason that cause the defective problem, and find best solution.
- Make Reward and punishment Regulation: The regulation can excitate workers to regulate their operations, and supervise their own behaviors, aim to the target of quality control.