Since zinc die casting parts are applied widely in automotive industry,The demand of custom automotive parts zinc die casting are increasing accordingly. As the advancement of automotive manufacturing, Personalized and customized requirements are consistently raising. So automakers are also looking for qualified supplier to meet those specific requirements of vehicle custom design. Finding top custom zinc die castings manufacturer in automotive industry is crucial for automotive manufacturer. What is top custom zinc die casting parts manufacturer in automotive industry? The below we guide them to find the qualified supplier.
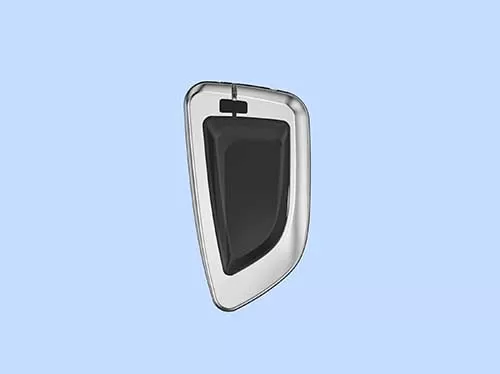
Content of Table
- Key Considerations For Find Top Custom Zinc Die Castings Manufacturer
- How to Source the Best Custom Zinc Die Casting Parts Manufacturer
- Conclusion
Key Considerations For Top Custom Zinc Die Castings Manufacturer
When looking for top custom zinc die castings manufacturer, critical factors should be evaluated. These factors like quality control, material properties, supplier capabilities, design and engineering support, and production efficiency. We have a classified introduction as a guidline.
Quality Control and Compliance
Automotive parts must meet rigorous standards for durability, safety, quality authorized system and premium performance. When selecting a supplier, it’s essential to ensure that the supplier adhere to international quality standards such as ISO 9001, IATF 16949, and TS16949. These certifications guide the supplier to follow strict quality control rules, conduct regular inspections at every stage of the production process. From raw material procurement to final product inspection. ensuring that each part produced meets the required specifications. The supplier is also had the right social responsibility to employees and retired workers.
Material Selection and Alloy Customization
Zinc alloys used in die casting has several grades, each specific characteristics that make them suitable for different automotive applications. Any time auto makers can select the appropriate zinc alloy material to cast high quality automotive components. Zinc alloy customization is neccessary. Such as the follow items.
Material Items | Character |
---|---|
Zamak 3 (Zn-Al) | This is one of the most commonly used zinc alloys due to its good mechanical properties and ease of casting. It is ideal for parts that require high strength and corrosion resistance. |
Zamak 5 (Zn-Al-Mg) | This alloy has better creep resistance and is used for parts that will undergo high temperatures or mechanical stress. |
Zinc-Aluminum Alloys | These alloys combine the best of both metals, offering higher strength, better casting characteristics, and resistance to wear and fatigue. |
As a custom zinc die casting supplier, who can recommend the best zinc alloy based on the part’s function and applications, with the environment testing experience, and mechanical properties inspection capability. The right zinc alloy can enhance the performance of the part and improve the overall product’s durability. Exception of the above zinc alloy customization, the specific requirements of casting parts also need to achieve custom quality standards.
Engineering and Design Support
Choosing a supplier that provides engineering and design support, seeking top-quality custom zinc die casting parts. Every one knows that an experienced supplier can help optimize part designs for casting, ensuring that the parts are not only cost-effective to produce but also perform optimally in their intended application. Suppliers should offer expertise in designing parts and optimization for zinc die casting. This involves of designs to reduce material waste, improvement of mold design, and guarantee of the correct mechanical properties. Casting Simulation Testing Analytisis, which can help predict stress points, optimize geometry, and repair designs and mold optimation before prototyping. Suppliers should offer rapid prototyping services, allowing manufacturers to test and refine designs before proceeding to full-scale production.
Production Capacity and Lead Time
Automotive manufacturers need to evaluate the supplier’s production capacity and ability to meet delivery deadlines. Large tons of automotive parts require suppliers with robust production capabilities and an efficient supply chain system. The supplier should have state-of-the-art die casting machines, including cold-chamber and hot-chamber machines, to meet varying part sizes and complexity. Suppliers should be able to design and manufacture durable molds that can withstand high-pressure casting cycles while ensuring part precision and quality. It’s important to ensure that the supplier can meet lead times and maintain flexibility to treat unforeseen changes in demand or design adjustments.
Cost Efficiency and Pricing Models
Cost control is a critical consideration for any automotive manufacturer. They should evaluate supplier total cost of production, which includes tooling costs, part material costs, production cost and quality control measures, and post-production services. A supplier’s pricing model must be transparent, Auto maker allows manufacturers present the cost breakdown. Involving of order volume, design complexity, and zinc alloy selection. According to different situation, automaker should have a proper pricing tolerancy. By building a long-term relationship with a supplier, manufacturers can negotiate better pricing and reduce overall production costs.
Prototyping and Testing
Prototyping is a crucial step in ensuring that the custom zinc die casting parts meet the required specifications and function as customer desire. Before committing to full-scale production, manufacturers should request prototypes to test the part’s mechanical property and conduct environment testing. Mechanical Property Testing will evaluate whether the parts can withstand the required stresses, strains, and environmental conditions. Environment Testing For parts exposed to high temperatures, thermal testing can verify their resistance to heat-related degradation and corrosion reistance Of automotive parts are often exposed to moisture and salts environment.
How to Source the Best Custom Zinc Die Castings Manufacturer
Finding the right supplier for custom zinc die casting parts involves extensive research and due diligence. Here are some tasks to help source top suppliers. We will start in four view degrees.
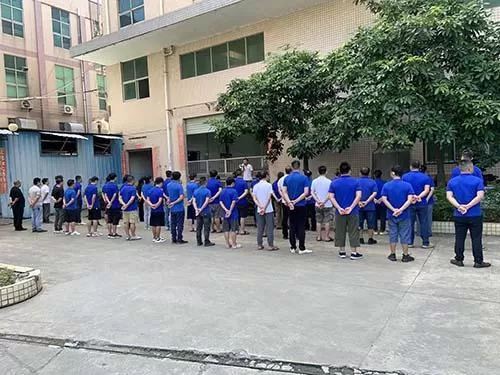
1. Industry Research
Automaker can attend trade shows and industry conferences focused on die casting and automotive manufacturing. Events like the Diecasting Congress & Exposition or the Automotive Manufacturing Summit provide opportunities to meet suppliers. Also visit some premium exhibition booth for showing die casting components , at site learn more about part design and production capability.
2. Supplier Audits and Site Visits
Conducting supplier audits and visiting their facilities, and supplier prorduction site and quality control rules. Firstly automaker can visit a site of manufacturer, overview of the enterprise. Then contact to the supplier, By visit the manufacturer at site, carry custom design and intension to discuss technical requirements directly with the engineering team.
3. Supplier Reviews and References
Before selecting a supplier, ask for references and case studies from the zinc casting manufacturer and learn more about work experiences in specific field. This will give you insights into the supplier’s reliability, customer service, and ability to meet deadlines and employees’ social responsibility.
4. Online Supplier Directories
Visit Platforms like ThomasNet or Alibaba provide searchable databases of die casting suppliers worldwide. These directories often present these manufacturers quality authorized system, production facilities and details about the supplier’s products and services.
Conclusion
Top custom zinc die castings manufacturer can provide high-quality, durable, and cost-effective automotive components to automakers. They can focus on key factors such as material selection, engineering support, production capacity, quality control, and cost efficiency to offer premium services to automakers. As professional zinc die casting maufacturer, TangSheng Hardware Technology will privode Quality Control and Compliance, Material Selection and Alloy Customization, Engineering and Design Support, Cost Efficiency and Pricing Models and Prototyping and Testing.