Die Casting Process becomes more and more popular in industrial manufacturing,because these die casting parts can be satisfied with some specific functional demand of the parts in many industries. If these parts are made, manufacturers design and manufacture the casting die, and process in high volume in high efficiency. The process involves several steps in die casting process, includes melting the cast metal, preparation of the mold, inject the molten metal, cools and solidifies the cast part, eject the part from the mold. As one of professional die casting manufacturers, TangSheng Hardware Technology offer guideline for die casting.
What Are The Steps In Die Casting Process?
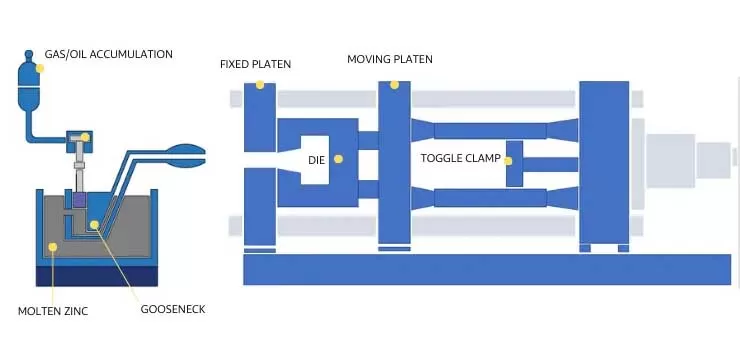
Hot Chamber Die Casting Process
The casting process is suitable for some low melting points metal alloys, such as zinc alloy, tin, lead and Bismuth. The features of it is fast cast cycle, high precision, low shrankage and recycled.
- Melting The Cast Metal
- Preparation Of The Casting Die
- Injecting The Molten Metal
- Cooling and Solidifying The Cast Part
- Eject The Cast Part out of From The Die
- Trimming And Finishing
- Inspecting The Cast Part And Quality Control
Alloy Type | Melting Range | Strength | Toxicity | Primary Use |
---|---|---|---|---|
Zinc (Zamak 3/5) | 385–480°C | High | Low | Automotive, electronics |
Tin (Sn-Ag-Cu) | 180–320°C | Medium | Low | Electronics, soldering |
Lead (Pb-Sb) | 250–350°C | Medium | High | Batteries (declining use) |
Bismuth (Field’s Metal) | 47–170°C | Low | Low | Prototyping, medical |
Cold Chamber Die Casting Process
The die Casting Process is favor of higher melting points metal alloys, such as Aluminum alloy, Copper, Iron, Stainless steel, Gold and Silver. The process maintain slow cast cycle, high precision, high shrankage and low ductility, suitable for large size cast parts.
- Melting The Cast Metal:j
- Preparation Of The Casting Die
- Injecting The Molten Metal
- Cooling and Solidifying The Cast Part
- Eject The Cast Part out of From The Die
- Trimming And Finishing
- Inspecting The Cast Part And Quality Control
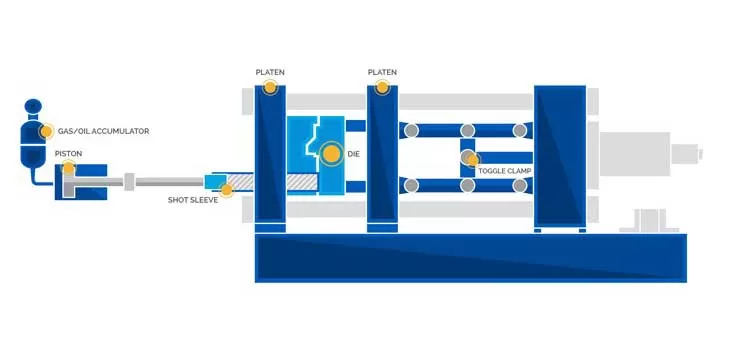
Alloy Type | Melting Range | Strength | Toxicity | Primary Use |
---|---|---|---|---|
Aluminum Alloy | 600-800°C | High | Low | Automotive, aerospace |
Brass | 885-995°C | High | Low | Electronics, decoration |
Stainless Steel | 1245–1530°C | Very High | Low | High precision and wear resistance parts |
Gold | 1064°C | Low | Low | Jewellery, gifts |
Silver | 960-1000°C | Low | Low | jewelery, electrics |
TangSheng Offers Guideline For Die Casting
TangSheng Hardware Technology is specializing for manufacturing metal components, which are made by die casting techniques tailored to meet specific requirements or unique designs. Client provide their drawing and design plan to their supplier, hand to their supplier to design the product that they desired. It contains the design of custom product model and creating precisoin molds or dies. Custom die casting projects have OEM and ODM services. Whenever, In accordance with customer’s specific requirements, Supplier should produce high-quality custom die casting components.
Tailored Solutions
The client present the design requirements and design plan to the supplier, and require the supplier to design the molds or dies to meet the specific requirements of the custom component, so that ensuring the component fits seamlessly into their desired application. This includes of aluminum and zinc die casting component design guides.
The Right Material Options
Among various materials like zinc, aluminum, magnesium, or their alloys materials, the manufacturers can choose the best alloy material to make custom die casting components for specific requirements.
Melting Metal Alloys And Prepairation For Die Casting Process
Inject The molten Alloy into The Steel Mold
Forming the Cast Part And Eject It
Post Process And Diversity Surface Finishes
These custom die cast parts can be finished with various surface finishes, afterwards, they need minimal post-process. Through additional treatments like polishing, plating, or painting to meet appeal decoration or functional needs.