Aluminum Alloy Die Casting is one type of common manufacturing process in modern iudustrial production. Injecting the molten aluminum alloys into the preheated steel die under high pressure,then cool the steel die, and make the molten aluminum alloys solidify, and the die open, the shaped aluminum part is ejected out from the die. Aluminum allloys melting points are higher, so the process cast cycle is longer than zinc die casting process one. It belong to cold chamber die casting technique.
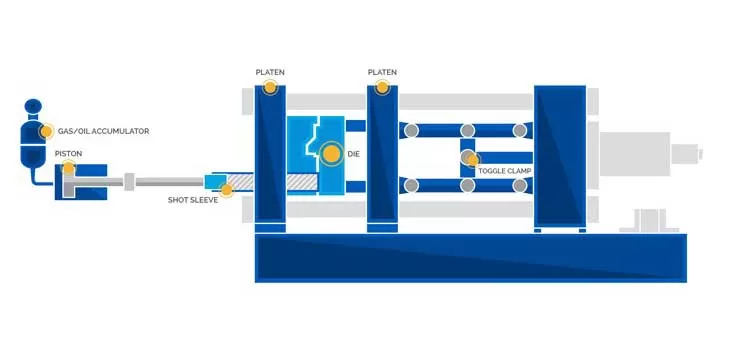
Overview Of Aluminum Alloy Die Casting
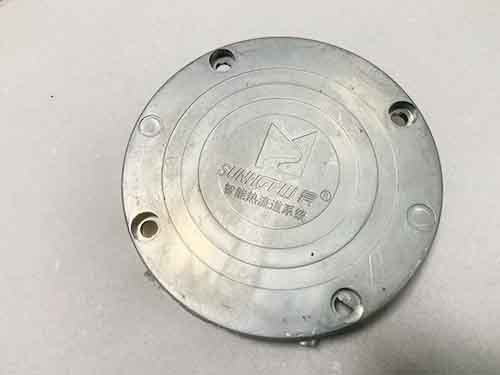
The Features OF Aluminum Alloy Die Casting
- High Precision & Complexity
- Excellent Strength-to-Weight Ratio
- Good Corrosion Resistance & Thermal Conductivity
- Smooth Surface Finish
- High Production Efficiency
Common Aluminum Alloys Used
- ADC12 (A383) – Popular for its excellent castability and mechanical properties.
- A380 – Offers good strength, thermal conductivity, and corrosion resistance.
- A360 – Known for high corrosion resistance and pressure tightness.
- AlSi10Mg – Used in automotive and aerospace for its strength and lightweight properties.
A Wide Range Applications
- Automotive :
- Electrics
- Consumer Goods
- Aerospace and Aircraft
- Communication And Internet
Advantages & Disadvantages Of Aluminum Alloy Die Casting
As one type of common manufacturing method in industrial process, which also has both strength and limitation on production. So the advantages and disadvantages of aluminum alloy die casting listed on the follow.
Advantages
â—† High Production Efficiency
The production process method belong to automatic steamline production, using advanced die casting machine and high precision steel casting die to process high qualiy die casting parts in high volume production. Either minimizing the material waste or saving more labor cost in the duration of aluminum alloy die casting process. and result in a high production efficiency.
â—† Excellent Dimensional Accuracy & Surface Finish
The high precision casting die can offer accuracy dimensional cores and cavities of the die and fine surface finish of the core. when the molten aluminum all is injected into the die, under high pressure, the solidified aluminum die casting part generates a fine surface finish, and minimizing post-process. Also the aluminum die casting part has an excellent accurace dimensions and fine surface finish.
â—† Lightweight & Strong
The aluminum alloy die casting part is very lightweight due to small density of aluminum,but it is strong strength and durable. So they can be used in some specific fields, such as aerospace and aircraft, portable smart devices and homehold appliances. They are very light, and enable reduce the whole weight and easy to be moved and running well.
â—† Good Corrosion & Heat Resistance
The heat dissipation of aluminum material is supporior, so the aluminum alloy parts have been used for this purpose, which prevents high temperature damage from mechanical part frictions and electric components generating heat energy. The aluminum part can transfer the heat energy towards air and other medias quickly and reducing the risk of high temperature. Good corrosion properties is the character of aluminum alloy, The aluminum may be oxidated and deposited oxnodized layer on the surface of the aluminum part, and form a profer protective layer, and endure acid and solt substance and moisture and harsh environment corrosion.
â—† Complex Geometries
The aluminum alloy casting die is made of high quality steel material and ensure the aluminum casting part accurate dimensions and fine surface finish. By cnc machining, EDM maching, grinding, polishing and more precision processes, especially the core and cavities of the die. Then forms complex geometries of the cast part.
â—† Cost-Effective for Large Volumes
After the precision casting die passed a trial process and test, the mass production for die casting parts starts. Cost-effective for large volumes is lower, automatic steamline production and advanced die casting machines can reduces average production time of each part and minimizing the aluminum alloy waste.
â—† Provide Good Thermal & Electrical Conductive Parts
The aluminum material has natural thermal and electrical conductivity. The aluminum die casting parts are used for heat sink, enclosure and housing for electric control module. The alumnium part can transfer hear energy towards the air and other substance quickly and keep an appropriate temperature level. And ensure the core module smoothly running. So aluminum alloy die casting can provide good thermal and electrical conductive parts.
Disadvantages
â—† High Initial Tooling Cost
Producing precision alumium casting parts in term of high precision steel casting die, ensure a consistent high quality standard. The die is made of high speed steel. So skilled-well engineers should consider that spending more expenses for processing a set of high precision casting die firstly before mass production. This is high initial tooling cost.
â—† Porosity Issues
Aluminum alloy is mutil porossity metal, when molten aluminum alloy is solidified, much entraped air inside of molten alumiunm alloy need exhausted, much pin porosity generates on the surface of die casting part. To trim its further surface finish, we suggest improve the surface bond of the part by plating zin metal layer.
â—† Less Ductility
Aluminum ductility is less than zinc alloy, so aluminum alloys are used for large size die castings across many industries. Of course the wall of die casting part is thicker to balance the cast part integrated structural steady, and spend longer time to cool and has a big shrankage in each cast cycle. Its less ductility due to aluminum natural metal properties.
â—† Not Ideal for High-Stress Applications
Aluminum metal is soft, so the aluminum alloy die casting part can’t withstand high stress applications. It may deform and damage in condition of heavy stress. These alumium parts are only very light, they are portable, and applied to the purpose of lightweight and portable. Such as toys gearing and decorative and trimming components in aerospace and automotive industries.