To meeting the demand of the market in the world, more and more die casting manufacturers begin to engage in production of various metal die casting components, involves of aluminum alloy die casting, zinc alloy die casting , copper die casting and stainless steel die casting. The die casting process can create diversity metal die castings with different molten metal and meet various requirements of industrial manufacturings. Today we will have a detail explanation about die casting process and advantages of die casting.
What is die casting process ?
Die casting process is a metal casting process where forces molten metal into the designed casting die and formed. The casting die or mold may be hard steel, Cermaic, plaster and Sanding. Creating cavities in the die or mold using two pieces dies (like a permanent mold). The die casting process depends on different process technique in accordance with different material and craft process requirements.
In order to ensure that die casting parts have complex geometries design and tight tolerance dimensions, Die casting manufcturer often introduce advanced die casting equipment and make high precision high quality steel mold, added with advanced die casting technique to produce a high volume cast parts with consistent quality in high efficiency. Mechanical die casting process is higher effective manufcturing process and also create more smoother die castings surface finishing, compare to manual die casting process. Two main types of die casting technology included.
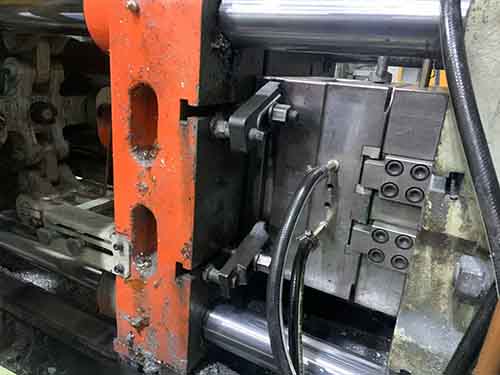
Hot-Chamber Die Casting
Integrated with the molten metal pot. Through gooseneck mechanism, pushing the molten metal into the heated die under high pressure, and cools and solidifies and forms the intended shape die casting part. It is primarily used for metals with low melting points like zinc, magnesium, and lead. The die casting process is favor of producing high precision,small and medium sizes die casting components with fine surface finish. Such as zinc alloy die casting parts. Hot Chamber Die Casting Is The Key Technique For Zinc Alloys Casting
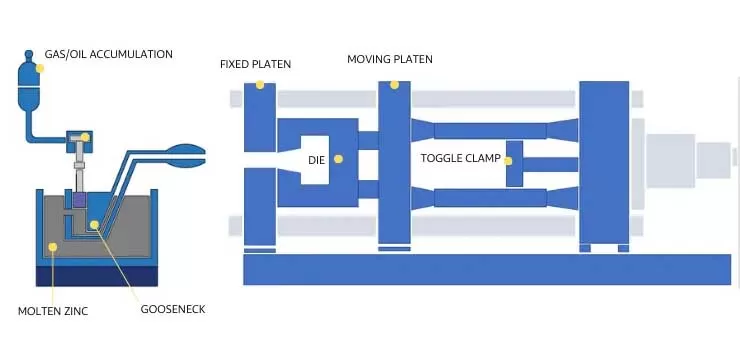
Cold-Chamber Die Casting
Ladling the molten metal into a cold chamber where it is then injected into the die under high pressure. Metal melton pot is apart from the die casting machine, becase the pot high temperature affects the machine temperature rigidly. This is suitable for metals with higher melting points, such as aluminum, copper, and some magnesium alloys. The die casting process is suitable for making aluminum die casting parts.
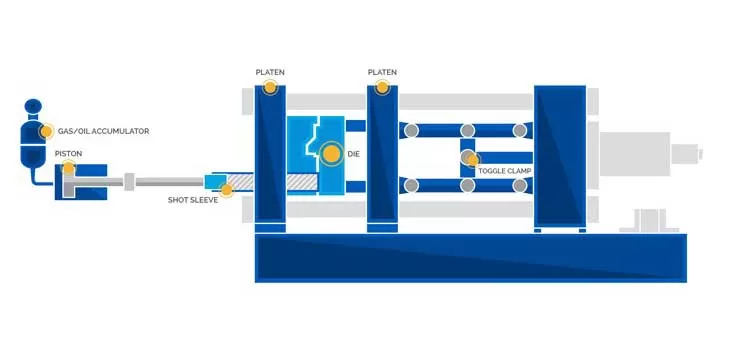
Advantages of Die Casting
Die Casting is a high efficiency and versatile metal manufacturing process, with high precision die, advanced die casting machines and unique casting technology. Die casting manufacturer produces diversity die castings with high quality, and ensures the tight tolerance dimensional requirements and smooth surface finishing. Here are the key benefits of die casting.
Advantages | Deteail Description |
---|---|
High efficiency And High Speed Mass Production | Computer numical control die casting machines, high precision casting die and automatic production lines will offer high efficiency and high speed mass production. |
Tight Tolerance Dimensional Casting Parts | The casting die is processed and manufactured by precise cnc machining center and EDM. Especially the cavities of the die precision extension is up to 0.1um, so the tight tolerance dimension of the part ensured. |
Smooth Surface Finishing Process | The core of the casting die is polished delicately and ensure the surface finish of the cast part. Under high pressure, the good fluidity melton metal flow fine surface finishing. |
Complex structural Casting Pars | The complex structure design of part needs more complex casting die. With advanced 3d software, engineers can design more complex functional casting die, ensure producing high quality complex structural casting parts. |
Thin Walled Casting Parts | The high precision casting die, strong fluidity molten metal and computer numical control die casting machine will promote die casting manufacturer to process thin walled casting parts. |
Reduced Waste Material During Die casting Process | The precision die casting process can save more waste material during casting process. This due to the volume of the injection molten metal is controlled by numical system. |
Cost-Effective In Large Volumes | Rely on automatic prorduction lines, high speed mass production and follows the standard quality management system, ensure high quality, avoid reworking, Cost-effective in Large volumes. |
Conlusion
Overall, die casting combines the benefits of cost-effectiveness, precision and durability. This makes it a preferred method for manufacturing a wide range of components. Die casting manufacturers can process diversity metal die casting parts with different metal alloy. In order to ensuring high quality casting parts in mass producution, engineers and production technician should have a colloberation work, and have a high efficiency in large volumes. This is just advantages of die casting.