In fact, we can see two types of common formed aluminum alloy parts, which are die cast aluminum and extruded aluminum parts. Depends on the demand of functions and applications of the parts, various shape aluminum alloy parts are processed to meet their utilizations in different fields. The two types of alumium process are different manufacturing processes, manufacturers choose the right manufacturing process to produce high quality aluminum alloy formed parts. What is The Difference Between Die cast Aluminum and Extruded Aluminum? Learn about it carefully to help us to handle the aluminum part process and quality control.
Difference Between Die Cast Aluminum And Extruded Aluminum
From the below several aspects, we are known that these two types of aluminum processes are significant differences in manufacturing process methods, selection of alluminum alloys and applications.
Aspects | Die Cast Aluminum | Extruded Aluminum |
---|---|---|
Manufacturing Process | molten aluminum injected into a mold under high pressure. Suitable for high-volume production, and small-to-medium parts | heated solid aluminum extended through a die to form long shapes. Ideal for linear profiles, such as rods, tubes, channels. |
Strength & Durability | Micro-porosity, reduces strength. Often heat-treated for better properties. | Stronger due to work hardening during extrusion. Better structural integrity. |
Cost & Production Efficiency | High initial tooling cost, Economic for mass production. | Lower die costs, but post-processing adds expense. More cost-effective for long, uniform shapes. |
Selection of Aluminum Alloys | ADC12, A380, A356 | 6061, 6063, 7075 |
Surface Finish Options | As-cast, anodized and painting in common condition | Process, anodized and painting. |
Precision Tolerancy | High Precision Process, Thin wall is acceptable. | Low tolerancy process, thick wall process. |
Common Applications | Engine blocks,Electronic housings (laptops, phones),Automotive transmission cases,Power tool bodies,Household appliances | Aluminum frames (windows, doors),Heat sinks,Structural beams ,Pipes & tubing,Automotive rails. |
Die Cast Aluminum And Extruded Aluminum Parameter
Die Cast Aluminum Alloy Parameter
Aluminum Alloys | Composition | Tensile Strength | Yield Strength | Elongation (%) | Hardness (Brinell HB) |
---|---|---|---|---|---|
A380 | Al-8.5%Si-3.5%Cu-0.5%Fe | 315–330 | 160–170 | 2–4 | 80–85 |
ADC12 | Al-10-12%Si-2.5-3.5%Cu | 300-320 | 150-165 | 1-3 | 75-80 |
A383 | Al-9.5-11.5%Si-2-3%Cu | 310-325 | 155-170 | 2-4 | 80-85 |
A360 | Al-9-10%Si-0.4-0.6%Mg | 290-310 | 140-155 | 3-6 | 75-80 |
A413 | Al-11-13%Si | 280-300 | 130-145 | 2-5 | 70-75 |
Extruded Aluminum Alloy Parameter
Aluminum Alloys | Composition | Tensile Strength | Yield Strength | Elongation (%) | Hardness (Brinell HB) |
---|---|---|---|---|---|
6061-T6 | Al-1.0%Mg-0.6%Si-0.28%Cu | 310 | 275 | 12 | 95 |
6063-T6 | Al-0.7%Mg-0.4%Si | 240 | 215 | 12 | 73 |
6005A-T6 | Al-0.5%Mg-0.6%Si | 270 | 240 | 10 | 80 |
6082-T6 | Al-1.0%Mg-0.9%Si-0.7%Mn | 310 | 260 | 10 | 95 |
7075-T6 | Al-5.6%Zn-2.5%Mg-1.6%Cu | 570 | 505 | 11 | 150 |
Aluminum Alloy Die Cast Process Vs. Extruded Aluminum Alloy Process
Aluminum Alloy Die Cast Process
- Process Overview: Molten aluminum injected into a steel mold under high pressure. Form Complex 3D shapes, thin walls, fine details. remain high precision small and medium sizes casting parts.
- Material Properties: Good corrosion resistance, superior heat dissipation, common alloy aluminum, A380, ADC12, A413.
- Cost & Tooling : Intial High tooling cost, economical for high volume production.
- Applications for Industries: Automotive, Electronics, Consumer Goods, Mechanical Components, Medical equipment and Homehold hardware.
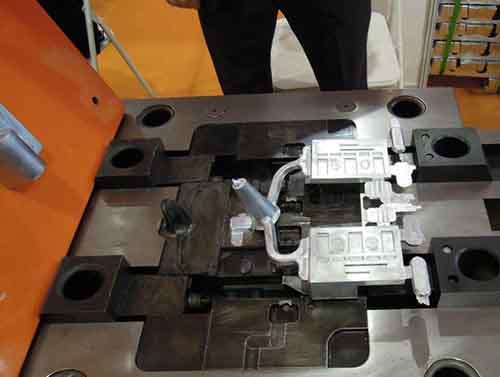
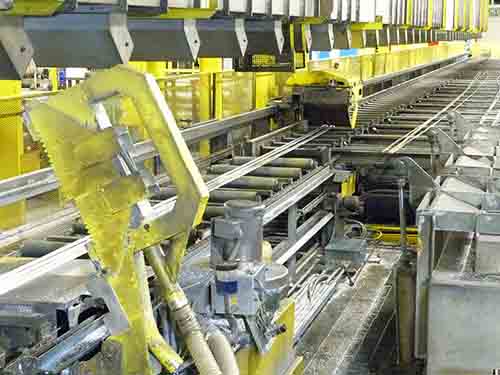
The Aluminum Alloy Extruded Process
- Process Overview: Solid aluminum billet heated and forced through a die. Form intended aluminum parts.
- Material Properties: High ductility, strong corrosion resistance and best thermal conductivity. Common aluminum, 6061, 6063, 7075
- Cost & Tooling: Low die cost, but more post-process is neccessary. Post-process cost is higher.
- Applications for Industries: Automotive, Decorative panel and trimming, Window and door frame.