Zinc die casting of development have an increasely trend in current metal casting industry, the scale of their applications are also enlarging continuously in many fields. This will be due to zinc alloy special properties, cost-efficiency and having a high volume in production. Compare to other castable metal, such as aluminum alloy, iron, copper and stainless steel, zinc die casting is ideal for miniature parts manufacturing, Why ? The below we will explore zinc die casting’s advantages and benefits in detail.
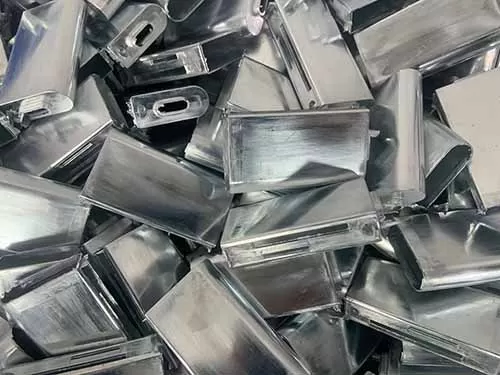
Content List
- What is Zinc Die Casting
- Zinc Die Casting Is Ideal Solution for Miniature Parts Manufacturing
- Contact Us
What is Zinc Die Casting ?
Zinc die casting is a manufacturing process in which the melting zinc alloy is injected into a steel mold under high pressure. By special die casting technique, the process produces high-precision and durable metal parts with a smooth surface finish. What’s more, Zinc die casting is also a highly efficiency, can create intricate metal components. Especially its tight tolerances, strength, and aesthetic quality are guaranteed. So zinc die casting is favor of processing miniature casting parts.
Key Factors That Decides Zinc Die Casting Quality
Zinc Alloy Material
Zinc die casting is based on zinc alloys, which is a family of diversity alloys that combine zinc with aluminum, magnesium, and copper, called as Zamak alloys. Include of the below items.
- Zinc (Zn): The base metal of the alloy, zinc has a low melting point and good fluidity. and easy to be casted. Suitable for casting complex shapes. It’s also naturally corrosion-resistant, and create integrated structural cast part with intricate design and smooth surface finish.
- Aluminum (Al): Adding aluminum to zinc alloy can increase the alloy’s strength and hardness while also enhancing its resistance to corrosion. Aluminum also helps improve the casting quality, allowing for precise details in the finished part.
- Copper (Cu): Copper strengthens zinc alloys hardness and improves the alloy wear resistance. However, adding too much copper can reduce the alloy’s ductility, so the copper element amount is not over.
- Magnesium (Mg): Magnesium increases the alloy’s strength and corrosion resistance while improving its stability over time. It also helps reduce the chances of brittleness. Mg-Zn alloys are lightweight, high-strength materials with unique properties, making them useful in aerospace, automotive, and biomedical applications.
Die or Mold Performance
The high quality steel mold is made up of two halves, which are pressed together to shape zinc parts during the casting process. Definitely the Metal Casting Die & Mold Manufacturing is a complex procedure. The mold is designed to create the shape of the desired part. So dies in zinc die casting should be highly durable, repeatvie usage, and conduct high-volume production. So die or mold performance decides the quality and quanity of part in zinc die casting.
High-Pressure Injection
In the die casting process, molten zinc is injected into the die under high pressure, usually ranging from 10,000 to 30,000 psi. The pressure forces the molten metal to quickly fill the die cavity, and shape the part in cooling and solidifying in a few seconds. This high-pressure enables create smooth suface finish and complex structure with tight tolerances.
Zinc Die Casting Is Ideal for Miniature Parts Manufacturing
Zinc die casting has been an high effective method for producing intricate, high-precision parts across various industries, including of automotive, electronics, medical devices, and consumer goods. Advantages of zinc die casting can manufacture small, complex parts with fine details and tight tolerances. This is particularly important if creating miniature parts with both strength and dimensional accuracy. Why Zinc Die Casting is Ideal for Miniature Parts ? The below several points verify the real reason.
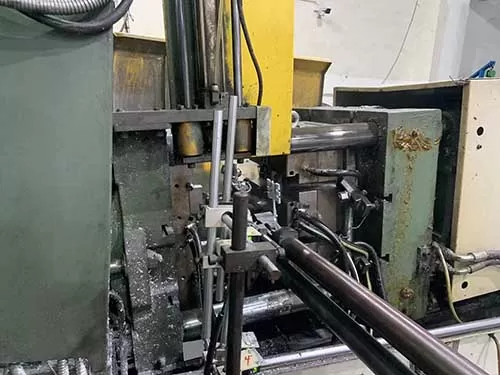
High Dimensional Accuracy and Precision
Zinc die casting can produce components with high dimensional accuracy. Zinc alloys have a low shrinkage rate as they cool, ensure manufacturers to achieve more tight tolerances components zinc die casting . The process can consistently produce parts with precision down to 0.1 mm. So zinc die casting is focus on the production of miniature parts zinc die casting. This eliminates the need for secondary machining processes in many cases, reducing overall production time and cost.
Capability for Complex Geometries
Zinc die casting excels at producing parts with intricate shapes and detailed features, focuses on miniature components. Even for parts with complex geometries, thin walls, and fine details, zinc die casting can efficiently create specific requirements and fuctional custom die casting components. Many miniature parts used in the automotive, electronics, and medical industries. Such as small slots, holes, and threads, which zinc die casting handles exceptionally well.
High Strength and Durability
Zinc alloys have a strength-to-weight ratio, highly suitable for miniature parts that need to withstand mechanical stress and environmental wear. Zinc parts also offer excellent corrosion resistance, these components can maintain high performance when they are exposed to moisture or corrosive environments. For example, miniature automotive or electronic zinc die casting components can endure vibration, impact, and wear, even though gas and fuel corrosion. Zinc Die Casting Is Ideal for Miniature automotive parts.
Fast Production Cycles and Cost Efficiency
Zinc die casting is a rapid manufacturing process, especially when producing large quantities of parts. Its high-speed injection of molten zinc into molds results in a few seconds. So manufacturers can produce large volumes of miniature parts quickly and cost-effectively. The combination of speed and material efficiency makes zinc die casting becomes best choice for mass production of miniature parts. Additionally, the die casting process has relatively lower material waste compared to other casting methods, such as sand casting.
Superior Surface Finish
Zinc die casting generally creates a smooth, high-quality surface finish right out of the mold. Especially for miniature parts, which need to meet strict aesthetic and functional requirements. When a good surface finish reduces the need for post-casting finishing processes, further more manufacturing costs and production time is saved . In another one,the smooth surface quality also makes it easier to apply additional treatments or coatings if needed, such as powder coating, plating, or painting. This is valuable when creating miniature parts that require specific finishes for corrosion resistance or visual appeal.
Conclusion
Zinc Die Casting Is Ideal for Miniature Parts Manufacturing. Its excellent dimensional stability, complex shape capabilities, strength-to-weight ratio, and cost-effectiveness makes zinc die casting best choice for producing high-quality miniature parts in a range of industries. As technology advances and the demand for smaller, more intricate components increases. Zinc die casting will continue to play a pivotal role in industrial manufacturing .For manufacturers seeking to produce small parts with exceptional quality and efficiency, Zinc Die Casting Is Ideal for Miniature Parts Manufacturing.