If you have been using zinc casting die to process zinc alloy casting parts , you must encounter some similar problems, such as flashes of zinc casting parts become more thicker, on the surface of parts appear more uneven areas , some porosity. At time time, you should think that zinc casting die requests to be repaired and modified in time. So as a professional die casting factory, zinc casting die maintenance and repair should be done in regular time.
Zinc Casting Die Maintenance And Repair Step by Step
Zinc Casting Die Maintenance And Repair is neccessary in regular time during busy mass production. For prolonging die life and consistent quality. When Metal Casting Die & Mold Manufacturing is produced,we also considered of a reasonable lifespan. But in order to avoid some accidents happens, proper maintenance and repair which can ensure that the final parts meet desired specifications. Here are the key points and attention issues for regular maintenance and repair of zinc casting dies.
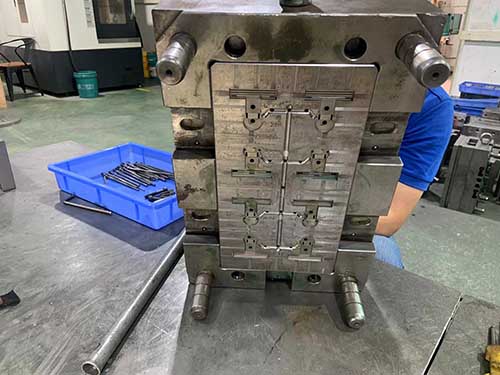
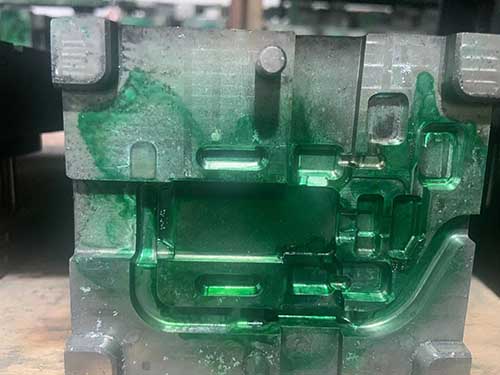
1. Regular Cleaning
After ech die have been used for some time, using soft brushes and non-abrasive cleaners to remove residue on the cores and cavities like lubricants, metal fragments, and oxidation. Ensure that the die works well to finish perfect die casting parts, and avoid casting defects or excessive wear.
2. Inspect for Wear and Damage
Inspection before and after every production run. Focusing on cavities, cores, parting lines, ejector pins, cooling channels and venting channels. And adjust operation parameters any time. Once warping or misalignment of ejector pins, Burrs or flash on parting lines occurred, the right solution is adopted to resolve these problems.
3. Lubrication
Lubricate is indispensable, especially before each production cycle. operator should lubricate these moving parts like ejector pins, slides, and cores. Avoid residues leaved on the cores and cavities, and leads to defects in the castings or malfunction of moving parts.
4. Thermal Management
Die cooling system is functioning efficiently to maintain proper temperature. integrated furnace can preheat melton metal and maintain a steady temperature which have a good fluidity metal. In another one, Die cooling system applies consistent cooling and heating to avoid hot spots and uneven thermal expansion that may damage the die.
5. Repairing Cracks and Damages
On the surface of as-cast part, there is thicker the parting line during the die casting production. we can repair it with welding techniques followed by cnc machining. Ensure the repair are compatible with the original die material to prevent other damages and defects from casting.
6. Storage of Dies
Clean and dry the die thoroughly before storing. Use anti-rust oil spraying or coatings all surfaces to prevent corrosion. Store dies in a clean, dry in normal temperature environment. Display these dies on the steel shelf and mark the serial number on them, always use protective padding.
7. Documentation and Tracking
Write a detailed record of each die’s maintenance, including inspections, repairs, and performance during production runs. Track the die running record, until the die is replaced by another one. These documentation help us to evaluate the die value in mass production and profits creation.
8. Die Components Fitting and Assembly
For technician for die components assembly, Installed die components is high precise, and they should fit each other and assemble together. improper assembly can lead to flash, excessive wear on parting lines and damage of die, and even affect the quality of the casted parts.
9. Ejector Pin and Slide Maintenance
To ensure the part eject out from the die smoothly, we should inspect ejector pins and slides . If neccessary, we may replace or repair bent, worn-out, or jammed pins.
Through above these key points, Zinc casting die Maintenance And Repair , which prolongs their lifespan and improves the quality of the die-cast parts produced. Regular maintenance, proper care, and timely repairs can save costs and prevent unexpected accidents happened.
Also Hire Well-skilled Mold & Die Technicians
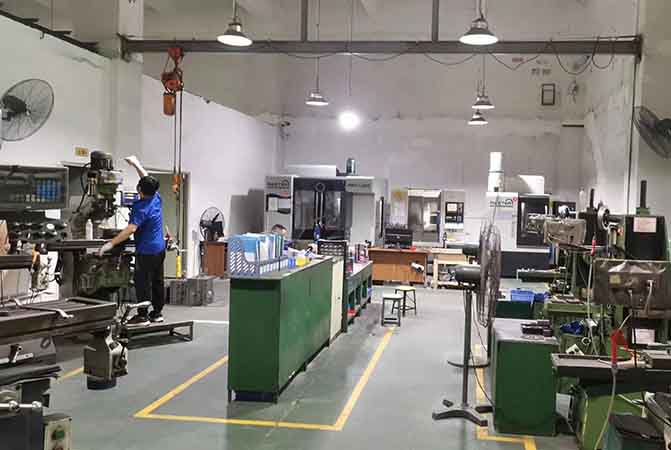
In addition to the above key points mentioned earlier, employing well-skilled mold and die technicians is crucial for Zinc casting die Maintenance And Repair. These technicians ensure that the dies are running in top working condition. Here’s why skilled technicians are essential. And their advantages as shown.
Expertise in Die Design and Functionality
Skilled technicians understand the intricacies of die design. Including parting lines, cavity structure, cooling systems, and ejection principle. With their expertise knowledge, they troubleshoot complex issues during production. They can also read and interpret technical drawings, and make accurate repairs or modifications once the accidents occurred.
Precision in Repairs
Technicians have enrich experience in welding, grinding, and polishing. They can repair cracks, worn-out areas, and other damages in precision. Skilled welders can repair the die’s surface without introducing stress points. And prevent further cracks or failures in the future.
Operate Accurate Tooling and Machining
For complex repairs or modifications, technicians may operate high-precision CNC machines, EDMs (Electrical Discharge Machines), and other tools to process and repair the cores and cavities of the die to meet tight tolerances for die casting parts.
Custom Modifications and Improvements
Over time, a die may need to be modified to improve performance and prolong its life. Skilled technicians have abondant work experience in die modification and improvements. So they can implement some custom projects with their successful operation cases to finish custom modifications and improvements for the die and process.
Handling Complex Issues
Such as excessive flashing, dimensional inconsistencies, or surface defects problem appears, skilled technicians can troubleshoot and resolve these issues efficiently. They can also balance the effects of thermal fatigue, erosion, and other forms of die degradation, and resolve the present troubles quickly.
Maintaining Safety Standards, Minimizing Body Hurt
Skilled technicians are comply with safety protocols strictly when handling, repairing, or maintaining heavy and complex dies. Similarly operating die repair, die assembly and trial die. Following the safty regulations, reducing the likelihood of accidents during the production process, minmizing body hurt from improper operation.
Conclusion
In order to ensuring zinc casting die maintenance and repair can save repairing time and enhancing production efficiency, Employing well-skilled mold and die technicians, as a fundamental aspect of ensuring the longevity and reliability of zinc casting dies. These technicians play a key role in the Zinc casting die maintenance and repair, in maintaining of the production line, reducing downtime, and improving the quality of die-cast parts. For a professional die casting manufacturer, Building a team of skilled technicians is essential to achieving consistent, high-quality zinc alloy die casting production.