Zinc die casting components electroplating is a process that enhances their lifespan and durability by covering a thin metal coating layer on their surface. It can prevent corrosion and rust on the surface of zinc die casting component from acid and oxidation. This makes these component strong corrosion resistance and more durable, bring more benefits to our life and work. The article will tell you that Zinc Die Castings Electroplating Brings More Benefits And Advantages.
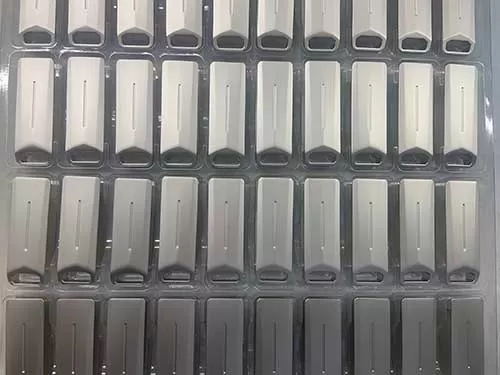
What is Zinc Die Castings Electroplating Process?
Zinc die casting electroplating process is a surface finishing process that coating on the surface of die-cast components with a thin layer of metal by electrode. This process enhances the performance, appearance, and durability of the components by applying a protective and decorative metal layer, such as nickel, chrome, or gold. The thickness of The elctroplating metal layer thickness is decided by the time that the components dipped in the electrolytic pool.
How the Process Works
Preparation of the Zinc Die-Cast Components
The component is thoroughly cleaned to remove dirt, grease, and oxides with degreasing, acid cleaning, or mechanical polishing to ensure a clean and reactive surface. Keep a bond surface for coating metal plating layer, have a good preparation of the Zinc Die-Cast Components.
Electrolytic Process
The cleaned components (cathode) is submerged in an electrolytic solution (electrolyte) that containing metal ions of the desired coating material.
By employing a direct electrical current , transfer the metal ions in the solution to deposit uniformly onto the surface of the zinc die-cast part. Then dry them using thermal equipment.
Post-Treatment
After plating, the components are rinsed and dried. Additional reinforcing treatments may be executed such as polishing, passivation, or applying a protective topcoat to enhance the final finish glossy and matte surface and performance. and make the plated components more durable.
Common Metals Used for The Process
- Nickel: By plating nickel layer, produces excellent corrosion resistance and wear protection. Often used as a base layer for chrome plating.
- Chrome: When plating chrome, shapes a hard, shiny, and highly durable finish on the surface of products. Common in automotive and decorative applications. These components are high wear resistance, hard surface and corrosion resistance.
- Copper: By coating a thin layer of copper, it has conductivity enhancement and as a base layer to improve adhesion for other coatings.
- Gold/Silver: Mainly Enhances conductivity, tarnish resistance, and aesthetic value. Often used in electronics and luxury products.
- Zinc (Zincating): It is a sacrificial layer for enhanced corrosion protection, especially in outdoor or marine applications, extend these components life span.
Zinc Die Castings Electroplating Brings More Benefits And Advantages
Benefits and advantages for electroplating zinc die casting components reflects the below listed points as the follow:
Increasing Corrosion Resistance, Extend Components Life Span
Electroplating creates a protective barrier that shields the zinc component. It can prevent corrosion from environmental factors,such as moisture, oxygen, and industrial chemicals. Particularly zinc die casting components in automotive, marine, and outdoor equipment where exposure to harsh environments frequently, And extending the components life span.
Improved Surface Hardness
Coatings like nickel or chrome adds hardness to the component surface. This makes the components wear resistance and more durable in high-stress and frequent wear and tear applications. These electroplated zinc die casting components can withstand repeative impact and keep its original shapes. The enhancement of hardness on the surface of component can be used for automotive and communication industries and fight frequent wear and corrosion against collision and harsh environments,
Enhanced Aesthetic Appeal
Electroplating provides a smooth and fine surface with various finishes (e.g., shiny, matte, or colored). These aesthetic appeal appearance components are used widely in consumer electronics, automotive interiors, and decorative components. Particularly zinc die casting components electroplated have a glossy, colored and matte final surface, present aesthetic appeal appearance.
Better Electrical Conductivity
Electroplated components used in communication and electronics. By electroplating with metal material like gold, silver, or copper enhances conductivity and ensures optimal performance and applications of zinc die casting components. Especially electric connector, which provide better electrical conductivity.
Electroplating Zinc Casting Components Guide
To guarantee that the electroplating process acheives high-quality and durable zinc die casting components, the following practices and controls should be implemented during zinc die casting components electroplating. This is the vital factors of zinc die casting component surface finish properly. As the follow is zinc die casting components electroplating guideline.
Surface Preparation
Proper cleaning and preparation of the zinc die casting component to achieve a strong bond between the base metal and the plating layer. This includes degreasing, acid cleaning, and surface activation. This is the base of creating high quality electroplating layer. Zinc surface creates a good adhesive layer to bond with the plating coating layer.
Plating Material Selection
The choice of electroplating material (e.g., nickel, chrome, or gold) should match with the component’s intended application and desired properties.
- Nickel Plating: Extend these zinc die casting components life span and enhance thier durability.
- Chrome Plating : Decorate these zinc die casting components and make them aethetics appeal and a good appearance, and enhance their wear resistance and corrosion resistance and extend their life span.
- rare metal Plating(like silver, gold and copper): To meet the specific requirements of functions and applications of zinc die casting components, mostly used for electric connector, which create a good electric conductivity for these components.
Controlled Plating Thickness
Consistent and appropriate coating thickness ensures optimal protection. With no compromising dimensional accuracy or not any additional cost. We can use non-destructive testing (NDT) methods like X-ray fluorescence (XRF) to measure coating thickness and verify uniformity. Execute adhesion tests with typical adhesive tape to ensure the durability of the electroplated layer under mechanical stress.
Post-Plating Process
Implement post-treatment processes such as polishing, passivation, or additional coatings to enhance properties like corrosion resistance or aesthetic finish. To reinforce electroplating layer practise and avoid varnish and peeling, These zinc die casting components may be done post-plating process if the functions and applications of them isn’t compromised.
Conclusion
Zinc die casting components electroplating bring more benefits and advantages for various industrial applications, especially automotive, communication and consumer electronics. The unique metal zinc alloy provide a bond layer for coating other metal coating material. So zinc die castings plating experience a more simple process and finish plating final process.